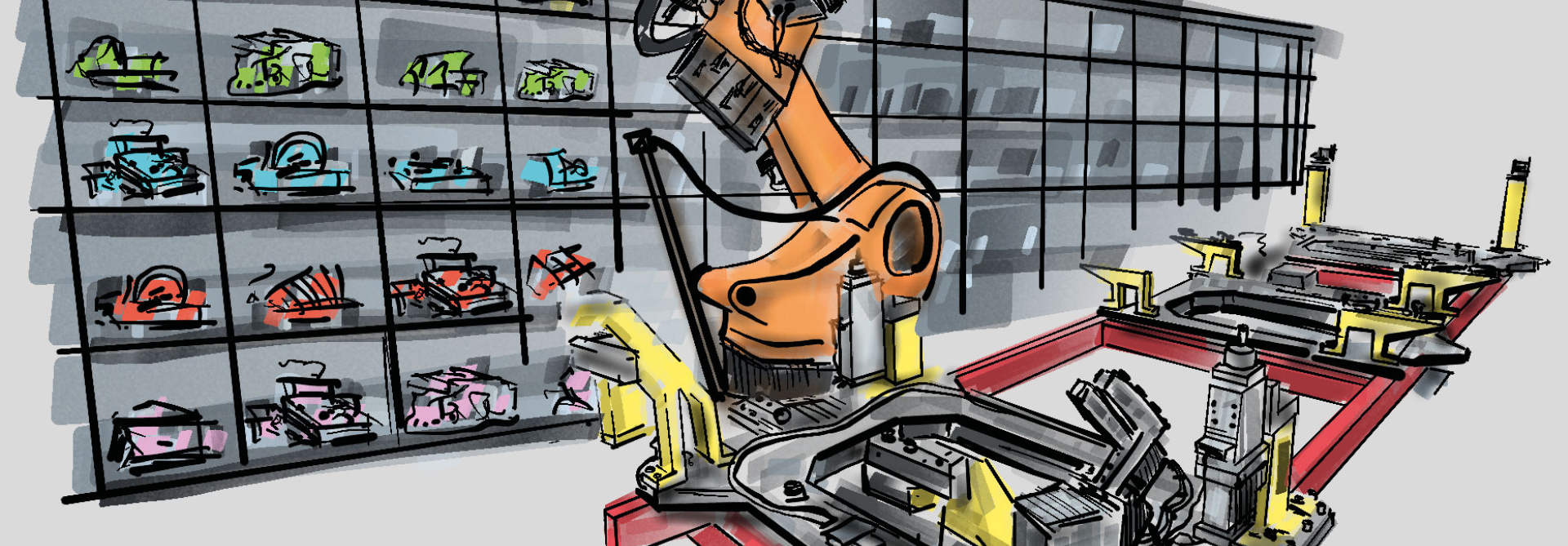
Das eine tun und das andere nicht lassen – Wie Flexible Manufacturing hilft, die Mobilitätswende voranzutreiben
- Erwin Fandl
- September 10, 2024
- 10-min Lesezeit
Die Mobilitätswende kann prinzipiell als gesetzt gelten: Die Zukunft ist elektrisch, der klassische Verbrennerantrieb wird zum Auslaufmodell. Doch die derzeit sinkende Nachfrage nach batterieelektrischen Fahrzeugen in Europa und das weiterhin bestehende Interesse an herkömmlichen Verbrennungsmotoren legen nahe, dass ein vorsichtiger Ausstieg aus der ICE-Technik sinnvoll ist. Das haben namhafte Hersteller verstanden – und in jüngster Zeit ein vorsichtiges Bekenntnis zur Fortführung der ICE-Produktion abgegeben.
Dennoch ist es für die gesamte Automobilindustrie eine Frage des Überlebens, Fahrzeuge mit alternativen Antrieben zu entwickeln und auf den Markt zu bringen. Ideal aufgestellt ist ein Hersteller, der je nach Nachfragesituation rasch und vor allem flexibel reagieren kann. Denn die Marktlage kann sich sehr schnell ändern, etwa wenn neue gesetzliche Vorgaben in Kraft treten. Eine schnelle Reaktion auf die jeweiligen Marktbedingungen ist aber kaum möglich, wenn Produktionslinien auf die Fertigung von Elektrofahrzeugen ausgerichtet werden.
In solchen Fällen kann ein externer Fertigungspartner helfen. Dieser übernimmt entweder die Produktion von Elektrofahrzeugen, um die bisherige Produktion nicht zu beeinträchtigen. Oder er setzt die Produktion von herkömmlichen Fahrzeugen mit Verbrennungsmotoren fort, wenn die Hersteller-eigene Fabrik bereits auf Elektrofahrzeuge umgestellt wurde.
Es ist wichtig, einen Fertigungspartner zu finden, der flexibel genug ist, um den Anforderungen gerecht zu werden. Ein solcher Partner ist Magna in Graz, der als Multi-OEM-Auftragsfertiger über langjährige Erfahrung verfügt und mit innovativen Prozessen sämtliche Antriebsstränge, von ICE über PHEV bis BEV, in einer Montagelinie integrieren kann.
Aber nicht nur in der Montage, sondern auch in den Technologien Karosseriebau und Lackiererei sowie in der gesamten Supply Chain bietet Magna maßgeschneiderte Lösungen zur Integration und Fertigung unterschiedlicher Plattformen an.
In den folgenden Artikeln stellen wir dar, wie wir auch Ihr Programm vollumfänglich realisieren können und damit der perfekte Partner für die Mobilitätswende sind:
Kapitel 1: Warum flexible Produktion in der Automobilindustrie überlebenswichtig ist
KapiTel 2: So sorgt ein Multi-OEM-Auftragsfertiger für Flexibilität im Karosserierohbau
Kapitel 3: Nadelöhr Lackieranlage: Vielfalt in Losgrößen von 1 bis 280.000
Kapitel 4: Schlüsselwort Flexibilität: Fahrzeugmontage in der Multi-OEM-Fertigung
Kapitel 5: Resilienz und Nachhaltigkeit: Die Logistik eines Multi-OEM-Auftragsfertigers
WARUM FLEXIBLE PRODUKTION IN DER AUTOMOBILINDUSTRIE ÜBERLEBENSWICHTIG IST
Die Nachfrage nach Individualität ist ungebrochen, wodurch die Automobilindustrie zunehmend auf kleinere Stückzahlen, höhere Anzahl an Karosserievarianten und verkürzte Modellzyklen setzen muss. Gleichzeitig erhöht sich die Innovationsgeschwindigkeit, insbesondere im Bereich der alternativen Antriebstechnik sowie der Konnektivität und der ADAS-Systeme.
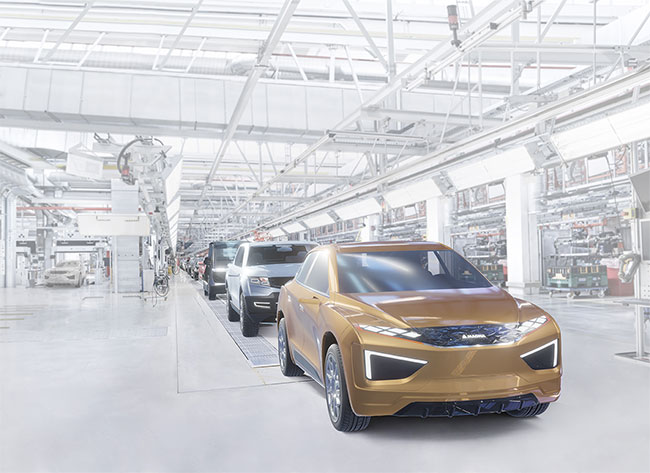
Die Mobilität ist im Wandel – und das auf verschiedene Weisen. Nicht nur die Produkte selbst ändern sich, wie steigende Marktanteile bei Fahrzeugen mit alternativen Antriebssystemen zeigen, sondern auch die Einstellung in der Gesellschaft zur Mobilität, etwa durch das allgemein höhere Umweltbewusstsein. Das alles führt zu sich wandelnden Anforderungen und Erwartungen bei Autokäufern, bei denen die neuesten Fahrassistenz- und Infotainment-Features klassischen Fahrzeugattributen wie Leistung und Fahrverhalten inzwischen starke Konkurrenz machen. Die Automobilindustrie muss also ihr Produktangebot so ändern, dass es zu den Herausforderungen der Zukunft passt und auch in der Produktion entsprechend neue Wege gehen. Als Lösung dafür bietet sich flexible Produktion bei einem erfahrenen Herstellungspartner an.
Nötige Veränderungen in der Automobilindustrie
Derzeit drängen nicht nur viele neue Anbieter (New Entrants) insbesondere aus dem asiatischen Raum mit elektrischen Autos in den europäischen Markt; auch die etablierten OEMs arbeiten mit Hochdruck an der Transformation ihrer Modellpalette. Manche von ihnen haben vielleicht auch die Geschwindigkeit des Wandels unterschätzt. Diese hat durch die Verwerfungen der letzten Jahre von Covid-19 bis zu den jüngsten geopolitischen Ereignissen und die dadurch bedingten Lieferengpässe noch einmal zugelegt.
Der Trend zu kleineren Stückzahlen
Insgesamt geht die Tendenz zu geringeren Stückzahlen je Fahrzeugsegment, die zudem schwieriger vorhersagbar sind. Angesichts der vielen Marktneuzugänge bleiben die Absatzzahlen nach der Einführung eines neuen Fahrzeugs weniger lang stabil, weil ein neues Modell technologisch schneller veraltet ist: Die Volumina flachen schneller ab, der gewohnte Sieben-Jahres-Modellzyklus ist nicht mehr selbstverständlich. Außerdem spaltet sich der Markt immer weiter auf. Einerseits werden immer mehr unterschiedliche Karosserievarianten auf einer Plattform entwickelt, um den Wunsch der Kund_innen nach Individualität zu erfüllen. Andererseits werden auch mehr Nischenmodelle und Sonderserien entwickelt und aufgelegt, etwa um das schon nach wenigen Jahren nachlassende Kaufinteresse wieder zu wecken.
All diese Zusatzversionen können mit ihren zumeist eher geringen Stückzahlen den Ablauf der Produktion in den auf Großserien ausgerichteten Werken der OEMs stören: Nischenmodelle sind schwierig in eine bestehende Linie zu integrieren, die grundsätzlich auf hohe Stückzahlen eines Modells ausgelegt ist. Zudem ist oft schwer abzuschätzen, ob das neue Fahrzeug bei den Kund_innen gut ankommt – oder ob unkontrollierbare äußere Einflüsse insgesamt zu einer Abschwächung des Marktes führen. Die Produktion muss also skalierbar sein, was in den Stammwerken der OEMs nicht immer ohne weiteres möglich ist.
Auch viele New Entrants der Automobilindustrie starten zunächst mit relativ kleinen Stückzahlen am Markt. Für sie ist eine skalierbare, flexible Produktion besonders wichtig, um nicht unnötig hohe Kapazitäten aufbauen zu müssen. Sie müssen jedoch weiterhin in der Lage sein, einer unerwartet höheren Nachfrage schnell nachkommen zu können.
Megatrend Elektrifizierung – und die beste Reaktion darauf
Einer der wichtigsten globalen Megatrends in der Automobilindustrie ist das derzeitige Bemühen um Nachhaltigkeit und CO2-Reduktion. Daraus resultierend ändern sich zusehends die Marktanforderungen vom traditionellen Verbrennungsmotor hin zu alternativen Antrieben und batterieelektrischen Fahrzeugen.
Die etablierten OEMs wählen dabei unterschiedliche Wege, um diese Herausforderung zu bewältigen. Die Entwicklung neuer, elektrisch angetriebener Fahrzeuge ist nur der erste Schritt, den die meisten traditionellen Hersteller schon gegangen sind. Die Herausforderung ist nun, die neuen Elektrofahrzeuge in ihre bestehenden Produktionsabläufe zu integrieren. Dabei bauen manche OEMs komplett neue Fertigungsanlagen für diese Modelle, während die Verbrenner auf den vorhandenen Fertigungsanlagen weiterlaufen, um das traditionelle Marktsegment weiter zu bedienen. So verdienen die Hersteller mit den konventionell angetriebenen Fahrzeugen weiterhin Geld und sind somit in der Lage, die Investitionen in Entwicklung und Produktion von batterieelektrischen Fahrzeugen zu finanzieren.
Andere OEMs rüsten bestehende Werke so um, dass dort nur noch E-Autos gebaut werden können und die Produktion von Verbrennern an diesen Standorten eingestellt wird. Dieses Vorgehen ist nicht ohne Risiko, denn das bisherige Kaufverhalten zeigt, dass die Zulassungszahlen von E-Autos volatiler zu sein scheinen und dass der Verbrenner nach wie vor nachgefragt wird. Je nach Marktsegment und Markt ist der Verbrenner weiterhin die präferierte Antriebsart für viele Kund_innen. Deshalb geht der Trend zur Entwicklung von Universalplattformen, bei denen die Fahrzeugarchitektur sowohl einen konventionellen als auch einen alternativen Antrieb abbilden kann. Dieser Ansatz erfordert allerdings Kompromisse, da die unterschiedlichen Antriebsarten mit ihren spezifischen Anforderungen ein unterschiedliches Packaging erfordern. Außerdem sind tiefgreifende Veränderungen und Anpassungen in den Prozessen, Produktionsanlagen und Lieferketten notwendig, um eine Integration in die vorhandene Fertigung und damit flexible Produktion sicherstellen zu können.
Auftragsfertiger als Problemlöser
Den Ausweg kann dem OEM hier ein externer Produktionspartner bieten. Auftragsfertiger sind durch ihre hohe Flexibilität in der Lage, auch kleinere Stückzahl effizient und in hoher Qualität zu produzieren. So hat Magna jahrzehntelange Erfahrung darin, unterschiedliche Fahrzeuge auf einer Linie zu produzieren. Damit können verschiedene Programme mit kleineren Stückzahlen eine Linie auslasten und damit wirtschaftlicher hergestellt werden. Bis zu einem gewissen Grad ist es dabei auch möglich, die Produktionskapazität zwischen den unterschiedlichen Produkten auszubalancieren, um die Produktionslinie auch im Falle einer nicht erfüllten Stückzahlerwartung bestmöglich auszulasten.
Für einen Multi-OEM-Fertiger wie Magna ist die Fähigkeit dieses ständigen Ausbalancierens Teil des Geschäftserfolgs. Sinkende und schwankende Volumina können bei einem OEM schnell zu Kapazitätsunterauslastungen führen und die Fertigung von Modellen ineffizient und kostenintensiv machen. Auch die Strategie einiger OEMs, Modelle mit einem geringen Deckungsbeitrag aus dem Programm zu nehmen, führt zu geringerer Auslastung der Werke. Deshalb kann es für einen OEM auch sinnvoll sein, beispielsweise die Auslauffertigung eines nach wie vor profitablen Modells nach außen zu geben. Ebenso interessant kann die Auslagerung der Fertigung sein, wenn der OEM etwa die Akzeptanz für Fahrzeugkonzepte oder -segmente testen will, ohne dafür eigene Kapazitäten bereitstellen zu müssen.
Flexible Produktion als ideale Voraussetzungen für New Entrants
Für Neueinsteiger in der Branche ist die Produktion bei einem externen Partner besonders interessant. Mit einem Auftragsfertiger erhält das Unternehmen Zugang zu einer bereits eingerichteten Produktionsstätte, inklusive der Belegschaft, mit eingespielten Prozessen und bestehender Supply Chain. Für ein größeres Projekt übernimmt ein in der flexiblen Automobilproduktion erfahrener Fertigungspartner auch die komplette Industrialisierung: Planung und Aufbau der Fabrik, die Etablierung der Prozesse, den Aufbau der Infrastruktur und die Festlegung passender Qualitätsstandards. Dadurch hat der Neueinsteiger nicht nur weniger Risiko in Bereichen, in denen er selbst noch wenig Erfahrung hat; sondern er kann auch schneller auf dem Markt sein. Und er kann sich auf Kernaufgaben wie Markenbildung, Werbung, den Aufbau von Vertrieb und Servicenetz und nicht zuletzt die Akquisition von Investoren fokussieren. Somit fallen einige Risikofaktoren weg, die immer wieder zum Scheitern von Startups im Automotive-Bereich führen. (Link zu Warum scheitern Startups in der Fahrzeugindustrie im ersten Jahr? 5+1 Gründe)
Magna vereint bereits seit vielen Jahrzehnten mehrere Fahrzeugprojekte von unterschiedlichsten Herstellern mit verschiedenen Anforderungen und Stückzahlen unter einem Dach, denn Flexibilität ist die größte Stärke des Zulieferers. Die Belegschaft, die Infrastruktur und die Prozesse sind auf OEM-übergreifende Fertigung ausgerichtet. Je nach Automatisierungsgrad der jeweiligen Modellreihe fertigen die Mitarbeiter_innen in der Produktion mit kürzeren oder längeren Takten mit unterschiedlichem Arbeitsumfang. Auch in der schnellen Integration in Kundensysteme und -prozesse ist die Belegschaft sehr erfahren. Für den Fall, dass Magna möglichst eigenständig arbeiten soll, besteht ein bewährtes System hauseigener Prozesse und Standards – was gerade New Entrants helfen kann, schneller auf den Markt zu kommen.
Es wurden bereits Multi-OEM-Projekte mit Stückzahlen von jeweils 10.000 bis über 100.000 Fahrzeugen pro Jahr realisiert. Mit dem Werk in Graz ist Magna auch der weltweit erste Auftragsfertiger, der eine breite Palette von Antriebstechnologien von verschiedenen Herstellern auf derselben Produktionslinie fertigt. Die Flexibilität zeigt sich weiterhin in der Lackiererei, wo die unterschiedlichsten Anforderungen von verschiedensten Kund_innen in einer gemeinsamen Anlage erfüllt werden.
Magnas „Flexible Manufacturing Solutions“-Initiative
Um die Fertigung im Magna-Werk in Graz noch flexibler und zukunftsfähiger zu gestalten, wurde eine Transformation unter dem Namen "Flexible Manufacturing Solutions" eingeleitet. Ziel ist es, bis zu vier Plattformen und acht Derivate unabhängig von Antriebsart und Stückzahlschwankungen auf einer Linie zu produzieren. Dabei strebt Magna an, der schnellste und effizienteste Partner für Programme mit mittleren (15.000 - 50.000 Fahrzeuge pro Jahr) und niedrigen Stückzahlen (< 15.000 Fahrzeuge pro Jahr) in Europa zu sein.
Mehr Plattformvarianten pro Linie im Karosseriebau möglich
Mit einer Reihe von Maßnahmen wird die Flexibilität im Karosseriebau noch weiter erhöht. Durch die Integration flexibler Fügestationen können mehrere Modelle auf einer gemeinsamen Linie gefertigt werden, ohne für jedes Modell einen eigenen Karosseriebau aufbauen zu müssen. Ein erster Schritt in der Flexibilisierung des Karosseriebaus war die Einführung des "Modular Flex Framing". Das System ermöglicht es künftig, bis zu sechs verschiedene Karosserievarianten in einer einzigen Station zu rahmen.
Herzstück ist ein flexibler Framer, der in rotierenden Speichern bis zu drei modellspezifische Adapter hält und diese passend für das jeweils nächste Fahrzeug in der Linie in Position bringt. Fährt zum Beispiel ein Sedan in die Linie, werden automatisch die entsprechenden Adapter eingesetzt, um den Sedan zu fertigen. Folgt darauf etwa ein SUV, werden die Adapter wieder automatisch getauscht und das SUV gefertigt.
Zusätzlich wird in Zukunft ein geometriebildender „Modular Flex Geoskid“ zum Einsatz kommen, der einen vollautomatisierten Austausch der geometriebildenden Vorrichtungen ermöglicht. Anstelle modellspezifischer Transportschlitten werden flexible Systeme eingesetzt. Ein universeller Rahmen wird automatisiert mit spezifischen Adaptern bestückt und ermöglicht so einen schnellen Wechsel zwischen verschiedenen Modellen. Zusammen erhöhen diese Maßnahme die Anzahl von Karosserievarianten pro Linie von zwei auf bis fünf – bei Erweiterung sogar zu sechs
Innovation als Schlüssel
Innovative Lösungen stellen dabei konstante Produktqualität sicher. Ein Beispiel hierfür ist die „Automated Body-in-White Fixture Control“. Die geometriebildenden Transportschlitten sind eines der wichtigsten Elemente beim Aufbau der Geometrie der gesamten Rohkarosserie. Geometrische Abweichungen führen dazu, dass auch die produzierten Rohkarosserien von den Maßen abweichen, was sogar den weiteren Montageprozess des Gesamtfahrzeugs behindern kann. Um dies zu verhindern, müssen die Transportschlitten periodisch überprüft werden – allerdings sind diese während des laufenden Betriebs nicht zugänglich und müssen somit außerhalb der Linie überprüft werden.
Anstatt dieser sehr aufwendigen periodischen Überprüfung vermisst Magna nun jede Fahrzeugkarosserie in einer eigenen Messstation. Mit einem smarten Algorithmus wird aus den Messdaten extrapoliert, ob die Transportschlitten innerhalb der Toleranzen sind. Diese deutlich engmaschigere Prüfung sorgt dafür, dass Abweichungen vorrausschauend erkannt und abgestellt werden. Nacharbeit an Karosserien, die diese Toleranzen nicht einhalten, wird somit stark reduziert.
Flexible Produktionsmöglichkeiten in der Lackiererei
Schon seit Jahren lackiert Magna alle Fahrzeuge, die am Standort Graz vom Band laufen, in einer gemeinsamen Anlage, unabhängig vom Hersteller oder der genauen Plattform. Dabei ist ein hoher Grad an Individualisierung möglich – von maßgeschneiderten Lackdesigns über besondere Lackeffekte (z.B. Perleffekt, Klarlack, Mattlack), kontrastierende Farben für Dächer und Türen bis hin zu Sonderfarben. Auch Niedertemperaturlackierung, z.B. für besondere Effektlackierungen oder das Lackieren von Anbauteilen, etwa für Sonderserien, ist möglich. An Stückzahlen deckt die Lackiererei alles von Einzelstücken (auch als Losgröße 1 bezeichnet) bis zur Großserie alles ab, und das unter Einhaltung sämtlicher Qualitätsstandards der jeweiligen Automobilhersteller.
Optimierung der Logistik durch Nähe zur Montagelinie
Die Logistik rückt im Grazer Magna-Werk näher an die Montagelinie, um die steigende Modell- und Teilevielfalt optimal handzuhaben. Heutige Industriestandard-Lösungen sind oft nicht effizient genug und benötigen zu viel Platz. Das neu konzipierte automatisierte Lager- und Bereitstellungssystem bei Magna in Graz zur Sequenzierung stellt den Mitarbeiter_innen die Teile in der richtigen Reihenfolge und mit den richtigen Ausstattungsvarianten nahe am Band zur Verfügung. Es reduziert einerseits Gehwege für die Logistiker_innen und andererseits den Platzbedarf für die Sequenzierung. Diese Maßnahmen ermöglicht es, dass bisher externe Sequenzierumfänge nun bandnah auf dem Werksgelände sequenziert werden, wodurch sowohl die Transportbedarfe reduziert als auch die Kosten pro Fahrzeug gesenkt werden.
Die reduzierten internen Transporte unterstützen auch die Nachhaltigkeit am Standort Graz. Das Werk ist bereits seit 2022 CO2-neutral, die verbesserte Logistik trägt zu einer weiteren Verringerung der Emissionen bei.
Produktflexibilität auf Montagelinie wird erhöht
In der Montage ermöglichen flexible Fördertechnik, eine flexible Hochzeitsstation und erweiterte Testkapazitäten die Fertigung von bis zu vier statt bisher zwei Plattformen auf einer Montagelinie. Durch den Einsatz von austauschbaren, produktspezifischen Adaptern werden Unterschiede in den Antriebsarten, Plattformabmessungen und Aufbauformen berücksichtigt. Die erhöhte Tragkraft der Transportgehänge ermöglicht künftig auch die Fertigung von größeren und schwereren Fahrzeugen und trägt dem steigenden Anteil an Elektrofahrzeugen Rechnung. Die zusätzlichen Prüfstände am Ende der Linie stellen sicher, dass die erweiterten Fahrzeugfunktionen auf ihre Zuverlässigkeit abgesichert werden können.
Durch die Erhöhung der Flexibilisierung in den verschiedenen Bereichen der Produktion ist Magna in Graz weiterhin der ideale Partner für traditionelle und neue Automobilhersteller. Kund_innen profitieren dabei von langjähriger Erfahrung und verkürzten Integrationszeiten.
SO SORGT EIN MULTI-OEM-AUFTRAGSFERTIGER FÜR FLEXIBILITÄT IM KAROSSERIEROHBAU
Ein konventioneller Karosserierohbau ist auf hohe Stückzahlen pro Fahrzeugmodell ausgerichtet und bietet nur eingeschränkte Möglichkeiten, unterschiedliche Unterböden und Aufbauvarianten in den Fertigungsprozess zu integrieren. Ein flexibler Karosserierohbau hingegen bietet innovative Lösungen, um die Herausforderung der Variantenvielfalt bewältigen können.
Die Automobilindustrie ist im Umbruch; nicht nur die Umstellung auf alternative Antriebe, sondern auch die immer weiter differenzierten Endkundenerwartungen erfordern eher kleinere Stückzahlen pro Automodell. Wie lässt sich die Produktion auch kleiner Serien auf einer Großserienanlage kosteneffizient und hochqualitativ darstellen?
Hohe Flexibilität an der Linie bei einem Multi-OEM-Auftragsfertiger
Der Schlüssel liegt darin, mehrere kleinere Serien auf einer gemeinsamen Großserienanlage herzustellen. Dafür ist es notwendig, einen hohen Grad an Flexibilität in der Anlage zu haben. Es muss möglich sein, innerhalb der Fertigungszeit bzw. der Förderzeit von Takt zu Takt oder von Fertigungsschritt zu Fertigungsschritt auf ein anderes Modell umzurüsten.
Im Rohbau stellt sich weniger das Problem des Box-Maßes, also der Karosserieabmessungen und Volumina, im Gegensatz zur Lackiererei – zumindest im Pkw-Bau. Stattdessen besteht hier die Aufgabe, eine zuverlässige Aufnahme der Karosseriebasis bereitzustellen, die an jeden der auf der Anlage gefertigten Fahrzeugtypen angepasst werden muss.
Adaptierung der Aufnahmepunkte durch speziellen Transportschlitten
Sollen mehrere unterschiedliche Fahrzeugtypen auf der gleichen Rohbau-Linie laufen, besteht die wichtigste Herausforderung in den unterschiedlichen Aufnahmepunkten des Unterbodens. Diese werden nicht vom Auftragsfertiger festgelegt, sondern sie sind durch die Fahrzeugarchitektur vorgegeben.
Dabei gibt es auch unterschiedliche Konzepte, wie aufgenommen wird: Schrauben, Stecken und Verriegeln – die Hersteller verfolgen unterschiedliche Ansätze. Ein Multi-OEM-Fertiger muss mit allen unterschiedlichen Aufnahmekonzepten umgehen können. Das in OEM-eigenen Großserienanlagen übliche Konzept der modellspezifischen Aufnahmevorrichtungen, oft umgesetzt als Bodenspannvorrichtung, ist also nicht umsetzbar, wenn der Karosseriebau unterschiedliche Modelle herstellen soll.
Dazu wurde bei Magna eine besondere Art eines modularen, flexibel adaptierbaren Aufnahmesystems entwickelt – der flexible Geo Skid.
Entwickelt wurde er aus dem bei Magna schon seit über 20 Jahren eingesetzten, Geo Skid genannten Fertigungsschlitten. Dieser entstand aus dem Bestreben, die Fertigungspräzision zu erhöhen. Dabei wird auf die Verwendung von Unterbodenspannsystemen verzichtet, um die Karosserie in den unterschiedlichen Stationen jeweils wieder neu zu zentrieren, denn jeder erneute Aufspannvorgang kann potenziell Ungenauigkeiten erzeugen. Stattdessen wird der Unterboden am Anfang des Rohbaus im Geo Skid fixiert, und der Skid wird in der jeweiligen Station festgesetzt.
Der modellspezifisch adaptierbare Geo Skid als Voraussetzung für freien Model-Mix auf der Karosseriebaulinie
Unterschiedliche Karosserievarianten auf einer Linie zu fahren – etwa Limousine, Kombi, Schrägheck oder auch SUV – wird heute auch im Hersteller-eigenen Karosseriebau umgesetzt. Dabei wird aber immer auf einem einheitlichen Unterboden aufgebaut. Die Herausforderung bei einer Multi-OEM-Fertigung besteht primär darin, mit unterschiedlichen Unterböden umzugehen. Es werden also Fahrzeuge auf einer Linie gebaut, die grundlegend nichts miteinander zu tun haben müssen – weder von der Fahrzeug-Grundarchitektur, noch von den Aufnahmepunkten her.
Daher ist hier ein Aufnahmesystem erforderlich, dass alle auf der jeweiligen Linie produzierten Karosserien beherrscht. Der patentierte flexible Geo Skid von Magna besteht prinzipiell aus einem einheitlichen Grundrahmen, an den die modellspezifischen Aufnahmen mit Nullpunkt-Spannsystemen spielfrei montiert werden und schon von daher die geometrische Präzision sicherstellen. Anders als bei den nur in einer Richtung variierbaren Schlitten, wie sie auch in einigen Werken der Hersteller für unterschiedliche Modellderivate eingesetzt werden, sind beim flexiblem Geo Skid alle Aufnahmepunkte verstellbar und können dem jeweiligen Produkt angepasst werden.
Magna ist mit diesem seit 2022 eingesetzten Konzept Vorreiter in der Automobilindustrie insofern einzigartig – auch wenn namhafte OEM bereits an ähnlichen Konzepten arbeiten, um in neuen Werken beispielsweise auf einer Linie die Fertigung von unterschiedlichen Fahrzeugen mit unterschiedlichen Antriebskonzepten zu integrieren.
Umfassende Automatisierung als Voraussetzung für flexiblen Karosserierohbau
Für jeden gefertigten Fahrzeugtyp ist auf der Linie – abhängig von den zu fertigenden Stückzahlen – eine bestimmte Menge an fertig adaptierten Geo Skids im Umlauf. Das ist nur durch umfassend integrierte virtuelle Planungssysteme und Simulationen möglich, allein schon, um den Rückfluss der Skids von Ende der Linie zurück zum Anfang sicherzustellen. Mit manuellen Konzepten wäre ein solch komplexer Fertigungsprozess gar nicht darstellbar.
Deshalb ist es erforderlich, dass jeder Fertigungsschritt in die Automatisierung eingebunden werden kann – von der Heranführung der jeweils benötigten Blechteile an die Linie über die Werkzeugwechselsysteme bis hin zur jeweiligen Füge- und Verbindungstechnologie: Punktschweißen, Kleben, Nieten oder auch Laserprozesse. Einzelne Skids können dabei aus dem Fertigungsprozess genommen und wieder eingeschleust werden – etwa, um die Skids umzurüsten und sie damit einem geänderten Modell-Mix anzupassen; oder auch, um Wartungsarbeiten ohne Unterbrechung der Fertigung durchzuführen.
Indirekte Toleranzüberwachung für höchste Fertigungspräzision und unterbrechungsfreie Produktion
Einen besonderen Stellenwert für die Herstellung hochqualitativer Endprodukte hat die präzise Einhaltung von Fertigungstoleranzen bereits im Karosserierohbau. Dabei hat Magna ein besonders smartes System zur fortlaufenden Überwachung der Fertigungspräzision entwickelt: Während des Produktionsprozesses sind die Fertigungsschlitten mit ihren Aufnahmevorrichtungen nicht zugänglich und können daher nicht vermessen und kontrolliert werden. Sie mussten daher traditionell in regelmäßigem Turnus aus dem Prozess genommen, im Messraum inspiziert und nötigenfalls gewartet werden: ein zeitraubender und kostenintensiver Vorgang.
Magnas Indirect Automated Body-In-White Fixture Controller spart dies und sorgt darüber hinaus für noch höhere Fertigungspräzision: Anstatt die Aufnahmerahmen selbst in festgelegten Intervallen aus der Linie zu nehmen und zu kontrollieren, werden im laufenden Produktionsprozess die produzierten Rohkarosserien mit Hilfe des intelligenten Systems genauestens vermessen.
So lassen sich schon Tendenzen zu Abweichungen der geometrischen Maßhaltigkeit vorausschauend erkennen, noch ehe sie zu ernsthaften Ungenauigkeiten führen. Jede Abweichungstendenz lässt sich auf den jeweiligen Geo Skid zurückverfolgen; so kann genau dieser Skid ausgeschleust, gewartet und rekalibriert werden.
Auf diese Weise werden die Aufnahmeschlitten nicht nur in festgelegten Intervallen, sondern faktisch kontinuierlich überwacht. Das zahlt sich nicht nur in Form einer konstant hohen Fertigungspräzision aus, die insbesondere für Endprodukte im Premium-Segment gefordert ist, wie sie bei Magna gefertigt werden. Gleichzeitig wird der Zeit- und Kostenaufwand im Prüfprozess reduziert und die eventuelle Notwendigkeit von Nacharbeit vermieden.
Räumliche Nähe aller Funktionen für die Fertigungsanlagen erlaubt schnelle Integration neuer Produktlinien
Eine besonders Stärke der Fertigung bei Magna ist die Konzentration von Planung, Entwicklung, Instandhaltung und Produktion an einem Standort. Die sehr straffe Organisation und die nicht nur räumlich, sondern auch organisatorisch kurzen Wege sorgen für verlustarme Kommunikation und ermöglichen die schnelle und flexible Umsetzung. Seit 1. Januar 2024 heißt dabei das Konzept: Anlage als Service. Somit kommen Planung und Instandhaltung unter einen Hut, also in einen Entwicklungsprozess. Das Ganze steht unter dem Stichwort „Nähe zur Produktion.“
Die kurzen Organisationswege vereinfachen auch die Integration neuer Produkte in die Fertigung. Gerade in der gegenwärtigen Umbruchsituation in der Automobilindustrie ist die Verkürzung der „Time to Market“, also die Schnelligkeit, mit der ein neues Produkt auf den Markt gebracht werden kann, ein entscheidender Erfolgsfaktor für den OEM.
Skalierbar und balancierbar: Die Vorzüge einer flexiblem Multi-OEM-Auftragsfertigung
Ein flexibler Fertigungsprozess hat daneben auch den Vorzug, während der Laufzeit eines Fahrzeugmodells flexibler auf veränderte Stückzahlerfordernisse etwa durch Nachfrageveränderungen reagieren zu können. Prinzipiell ist, technisch gesehen, die Fertigung ab der Loszahl Eins möglich – auch wenn bei sehr geringen Stückzahlen natürlich keine finanziell vertretbare Produktion möglich sein wird. Nach oben wird die realisierbare Stückzahl nur durch die technische Auslegung der Anlage limitiert – dargestellt in Einheiten pro Stunde – und durch die Anzahl der Produktionsschichten.
Bei Magna wird der Karosseriebau im Dreischichtbetrieb ausgelegt; das hat für den Hersteller den Vorteil geringerer erforderlicher Investitionen, als wenn nur in zwei Schichten produziert wird. Bei einem Zweischichtmodell müsste für den gleichen Fahrzeugoutput die Linie länger sein, was mit größeren Investitionen einhergeht. Bei Markt- oder Nachfrageänderung kann bereits im Karosseriebau, wie auch in den nachfolgenden Produktionseinheiten, relativ kurzfristig zwischen den einzelnen Produkten balanciert werden. Dabei muss der Rohbau nicht exakt entsprechend der Fertigungssequenz an der Montagelinie gefahren werden, sondern kann ein Stück weit entkoppelt laufen; denn die Rohkarosserien werden ja ohnehin vor der Lackiererei und vor der Montage gepuffert.
Dennoch ist die flexible Anpassbarkeit bereits im Karosserie-Rohbau ein essenzieller Baustein der flexiblen Auftragsfertigung; und die kann die Antwort auf die Herausforderungen sein, die sich dem Hersteller aufgrund zunehmend größerer Variantenzahl und kürzerer Modelllaufzeiten stellen.
NADELÖHR LACKIERANLAGE: VIELFALT IN LOSGRÖßEN VON 1 BIS 280.000
Eine hohe Oberflächenqualität ist unverzichtbar für einen guten visuellen Ersteindruck des fertigen Fahrzeugs. Die Lackiererei eines Multi-OEM-Fertigers muss dabei nicht nur eine Vielzahl von Fahrzeugtypen mit Multi-Material-Karosserien beherrschen und die dazu nötige Flexibilität bieten. Neben der Bewältigung größerer Volumen muss der Lackierprozess auch Sonderserien bis herunter zur Losgröße 1 in perfekter Qualität leisten können.
Die Fahrzeuglackierung spielt eine Schlüsselrolle für die Fertigungsqualität eines Autos – und so ist die Lackieranlage auch eine der zentralen Stationen in der Produktion. Der Lackierprozess birgt jedoch für einen Multi-OEM-Fertiger in all seinen Schritten, von der Vorbehandlung bis zum abschließenden Decklack, besondere Herausforderungen. Denn wenn zahlreiche unterschiedliche Baureihen auf einer Lackierlinie laufen sollen, spielen Vielseitigkeit, Flexibilität und Skalierbarkeit eine große Rolle; und dennoch darf die Effizienz ebenso wenig aus dem Blick geraten wie die Qualitätskontrolle.
Flexible Grundkonzeption der Anlage
Damit die Lackieranlage für eine möglichst große Anzahl an Produktlinien geeignet ist, muss sie zunächst über ausreichend große Boxmaß verfügen.
Dafür bietet die Lackierstraße bei Magna in Graz gute Voraussetzungen.
Dort sind die Stationen so konzipiert, dass sie auch für Fahrzeuge mit überdurchschnittlicher Aufbauhöhe und Länge geeignet sind. Dadurch können nicht nur SUVs und Minivans, sondern auch Offroad-Fahrzeuge effizient lackiert werden.
Um völlig unterschiedliche Karosserien bearbeiten und bewegen zu können, werden in Graz sogenannte Skids eingesetzt: Transportschlitten, die mit unterschiedlichen Aufnahmen versehen werden. Vormontierte Aufnahmelaschen werden mit aufgesteckten oder aufgeschraubten Adaptern bestückt, die fahrzeugspezifisch sind und sich jeweils nach den Aufnahmepunkten richten. Dabei gleichen diese Adapter auch unterschiedliche Aufbaumaße aus, um Dachoberkante oder Brüstungshöhe der Karosserien auf ein einheitliches Niveau zu bringen – nicht nur aus arbeitsergonomischen Gründen.
Unterschiedliche Arbeitsumfänge für unterschiedliche Produkte
Die unterschiedlichen Vorgaben der unterschiedlichen Hersteller, für die Magna produziert, können unterschiedliche Workflows erfordern – insbesondere, wenn je nach Fahrzeugprojekt zusätzliche Arbeitsgänge auszuführen sind. Deshalb muss die Lackieranlage so flexibel gestaltet sein, dass einzelne Arbeitsstationen hinzugefügt oder entfernt werden können, um den jeweils spezifischen Anforderungen der verarbeiteten Produktlinien zu entsprechen.
Dabei ist für eine Multi-OEM-Anlage ein modularer Aufbau der Arbeitsstationen vorteilhaft, denn dieser erleichtert es, bestimmte Abschnitte der Anlage speziell für die Anforderungen einzelner Hersteller anzupassen. Auf diese Weise können zusätzliche Arbeitsgänge oder spezifische Prozesse für bestimmte Produktlinien implementiert werden, ohne den gesamten Betrieb zu beeinträchtigen.
Sorgfältige Planung als Schlüssel zu Effizienz und Qualität
Um dabei teure und ineffiziente Rüstzeiten zu vermeiden, ist eine effizienzorientierte Planung und Koordination der Produktionsabläufe entscheidend. Die einzelnen Arbeitsgänge in der Lackieranlage müssen in der richtigen Reihenfolge und im richtigen Timing ausgeführt werden, damit die Produktion flüssig läuft – auch wenn sich die Umfänge unterscheiden. Dazu ist eine sorgfältige Abstimmung der Produktionspläne, des Materialflusses und der Ressourcen erforderlich. Das stellt sicher, dass die unterschiedlichen Anforderungen der Hersteller erfüllt werden, ohne die Qualität im Endergebnis zu beeinträchtigen.
Maximale Qualität durch strenge Kontrollverfahren
Eine Multi-OEM-Anlage muss hohe Qualitätsstandards erfüllen, weil sie für viele unterschiedliche Automobilhersteller arbeitet. Denn dabei sind unterschiedliche Lackierungsrichtlinien und -spezifikationen zu erfüllen. Strenge Qualitätskontrollen sind ein integraler und unverzichtbarer Bestandteil des Lackierprozesses: Um zu gewährleisten, dass die spezifizierten Qualitätsstandards durchgängig eingehalten werden, sind regelmäßige Inspektionen und laufende Tests ebenso in den Produktionsprozess eingebunden wie die Rückverfolgbarkeit eventueller Abweichungen.
Eigenes zertifiziertes Labor für Entwicklung und Prüfung der Materialien
Bereits die Qualität und Zusammensetzung der verarbeiteten Materialien muss den jeweiligen Anforderungen der unterschiedlichen Hersteller entsprechen. Magna kann auch diesen wichtigen Baustein eines optimalen Endergebnisses gewährleisten.
Im eigenen, zertifizierten Labor können in Zusammenarbeit mit den jeweiligen Lieferanten maßgeschneiderte Materialien entwickelt werden, die den individuellen Kundenanforderungen entsprechen. Zudem erfolgen dort alle wesentlichen Prüfungen. Dabei geht es nicht nur um das Lackmaterial selbst; Magna kann beispielsweise auch die verwendeten Klebstoffe für die Karosseriemontage im Labor prüfen: Eine Möglichkeit, die unter anderem für viele New Entrants attraktiv ist, weil diese möglicherweise noch keine eigenen Labore haben und diese Dienstleistung extern einkaufen müssen.
Unterschiedliche Prozesse für unterschiedliche Karosserien
In der Lackieranlage bei Magna werden neben 100%-Stahlblechkarosserien und 100%-Aluminiumkarosserien auch solche in Mischbauweise beschichtet. Zukünftige Herausforderungen liegen in der BEV-Architektur, wo speziell der Schwellerbereich besonders steif ausgelegt wird und verstärkt Gussteile integriert werden, um sowohl die Insassen als auch die unterflur eingebauten Batterien bei einem Crash optimal zu schützen. Die Mischbauweise aus unterschiedlichen Materialien wird somit noch komplexer. Das bedeutet, dass die Anforderungen sowohl für Vorbehandlung und KTL-Grundierung (Kathodische Tauchlackierung) als auch für den Trockner steigen und sich verändern; denn die Aufheiz- und Abkühlrampen müssen genau abgestimmt und kontrolliert werden, weil die Wärmedehnung der unterschiedlichen Metalle – Alu und Stahl – sowie die Karosseriebauverbindungen und Klebstoffe zu berücksichtigen sind.
Losgrößen von 1 bis 280.000
Die Multi-OEM-Lackieranlage bei Magna ist nicht nur in der Lage, Großserienprodukte effizient und hochqualitativ zu beschichten. Die Flexibilität der Prozesse stellt auch eine gute Skalierbarkeit für den Fall stark schwankender Produktionsvolumina sicher. Die Fähigkeit, kleine Stückzahlen und Sonderserien abzuwickeln – bis herunter zur Losgröße 1, etwa die Lackierung von Prototypen – unterscheidet die Grazer Lackieranlage von rein auf die Serienproduktion ausgerichteten Anlagen beim Hersteller selbst. Für diese Aufgaben gibt es in der flexiblen Lackieranlage zahlreiche Bypass-Linien und Sonderarbeitsplätze, an denen spezifische Tätigkeiten ausgeführt werden können, ohne dass die Serienproduktion beeinflusst wird.
Flex-Decklack-Konzept für Sonder- und Kleinserien
In der Decklack-Station sorgt die Möglichkeit einer Sonderfarbzuführung dafür, dass auch kleine Losgrößen und Einzelstücke in Großserienqualität lackiert werden können. Außer den 25 Ringleitungen, in denen die Decklacke in den Standardfarben aus den üblichen 300-Liter-Containern bereitgehalten werden, gibt es die Zuführung von Sonderfarben in 25-Liter-Gebinden, den sogenannte Hobbocks. Damit lassen sich bis zu acht unterschiedliche Sonderfarben pro Stunde lackieren, ohne den Serienprozess zu stören. Dabei helfen bewegliche Reinigungskolben in den Leitungen – ein sogenanntes Molch-System – den Lackverbrauch zu minimieren und Spülverluste gering zu halten.
Eine vorgelagerte Maskier-Station ermöglicht zusätzlich eine hohe Flexibilität bei Teilflächen- und Kontrastlackierungen, die individuelle Vorbereitung erfordern. Und auch bei der Finalisierung gibt es Variationsmöglichkeiten: Es können drei unterschiedliche Klarlacke appliziert werden – neben dem Standard-Klarlack eine kratzfestere Beschichtung und ein Matt-Klarlack, wie er immer häufiger nachgefragt wird.
Beste Farbtreue auch für Anbauteile bei Sondereditionen
Für Sondereditionen können nicht nur Karosserien und Blechteile, sondern auch Kunststoffanbauteile in der gleichen Lackieranlage lackiert werden. Karosserie und Anbauteile werden dabei direkt hintereinander mit dem gleichen Farbsystem aus dem gleichen Hobbock beschichtet; so ist sichergestellt, dass Qualität und Farbabstimmung der Anbauteile optimal zur Karosserie passen. Die Kunststoffteile werden danach in einen 80-Grad-Trockenofen gefahren, um das Material nicht zu überlasten. Diese Methode führt gerade in Klein- und Sonderserien zu einer sehr guten Farbgleichheit und Color-Harmony. Bei Anbauteilen, die in einem separaten Lackierprozess behandelt werden, ist dies schwierig zu erreichen und für Klein- und Sonderserien praktisch nicht umsetzbar.
Magna als One-Stop-Shop – Alles aus einer Hand
Weil in der Business Unit Lack bei Magna eine sehr breite Wissensbasis zur Verfügung steht, können neue Produktlinien sehr schnell und für den Kunden bequem und kostengünstig integriert werden. Das Team der Lackiererei kann auf Experten und Fokus-Gruppen für Simultanes-Engineering, Anlagen- und Prozessplanung, Fahrzeugsteuerung, Betriebsmittelkonstruktion und -fertigung, Applikationsexperten und natürlich eine sehr erfahrene Produktionsmannschaft zurückgreifen, was den Integrationsprozess vereinfacht und verkürzt. Die breit gefächerte und umfassende Eigenkompetenz deckt den gesamten Produktentstehungsprozess ab – von der Konzeptentwicklung über die Serienentwicklung bis hin zu Anlauf und Serienproduktion.
Mit dem Magna NET Zero Programm gerüstet für die Zukunft
Bei der Herstellung eines Gesamtfahrzeugs fallen für den Bereich Lackierung rund 70% der Energiekosten an. Insofern ist es eine große Herausforderung, auch diesen Produktionsbereich mit dem Magna NET ZERO Programm zu verbinden. Darin bekennt sich Magna zum Ziel, den gesamten Fertigungsprozess bis 2050 zu 100% nachhaltig zu gestalten. Zur Erreichung dieses Ziels im Bereich Painted Body wurde bereits jetzt ein Transformationsprozess namens Paint Strategy 2.0 begonnen. Es wird Energietransparenz geschaffen, Energieeffizienz in den Anlagen gefördert und auf erneuerbare Energien schrittweise umgestellt. So wird die seit 30 Jahren betriebene Lackieranlage fit für die Zukunft – mit der Vision, gleichermaßen Flexibilität, Wettbewerbsfähigkeit und Nachhaltigkeit zu erreichen.
SCHLÜSSELWORT FLEXIBILITÄT: FAHRZEUGMONTAGE IN DER MULTI-OEM-FERTIGUNG
Die Fertigstellung eines Fahrzeugs erfolgt natürlich erst in der Endmontage. Der Trend zur Individualisierung erfordert zunehmend Flexibilität, auch in Werken der OEM selbst. Bei einem Multi-OEM-Auftragsfertiger, wo verrschiedene Fahrzeugtypen unterschiedlicher Hersteller auf derselben Montagelinie produziert werden, nimmt die Vielfalt der Möglichkeiten eine noch größere Dimension an.
Der Fahrzeugmarkt ändert und segmentiert sich. Damit werden die jährlichen Stückzahlen pro Fahrzeugmodell geringer – und aufgrund der kürzeren Innovationszeiten auch die Baureihenlaufzeiten. Die Fertigung unterschiedlicher Modelle auf der gleichen Montagelinie kann ein Mittel sein, auch Fahrzeuge mit geringerer Stückzahlerwartung kosten- und zeiteffizient zu produzieren. Magna gehört zu den Pionieren auf diesem Gebiet.
Unterschiedliche Plattformen auf einer Fertigungsstraße
Der Begriff der Plattform ist im Wandel begriffen. Traditionell versteht man unter einer Plattform einen gemeinsamen technischen Unterbau, auf dem verschiedene Karosserieversionen realisiert werden können. Heutzutage unterscheidet man jedoch weiter zwischen der geometrischen Plattform, die beispielsweise die Karosseriebauweise und die Aufnahmepunkte auf der Fertigungsanlage für verschiedene Modelle gemeinsam hat, und der Elektrik-/Elektronik (E/E)-Plattform, die Gemeinsamkeiten im EOL (End-of-Line)-Testing aufweist.
Für die Integrierbarkeit unterschiedlicher Fahrzeugtypen in eine Linie ist dabei die geometrische Plattform der Ansatzpunkt. Wesentlich dabei ist das sogenannte Boxmaß, definiert aus Länge, Breite, Höhe und Gewicht des Fahrzeuges, sowie die Aufnahmepunkte am Unterboden: Wenn Fahrzeuge nach einer ersten Beurteilung in diese „Box“ passen, können diese auch in eine Montagelinie integriert werden.
Dabei hat Magna die Produktionsanlagen in der Fertigung dahingehend optimiert, unterschiedliche Fahrzeuge maximal flexibel aufzunehmen und durch den Montageprozess zu steuern. In ähnlicher Weise deckt die Prüftechnik in den beiden Multi-OEM-Montagelinien in Graz ein breites Spektrum an Kunden- und Systemanforderungen ab. So lassen sich auch unterschiedliche E/E-Plattformen verarbeiten – und weitere Plattformen mit relativ geringem Aufwand integrieren.
Grenzen der Integration: Nicht alles technisch Mögliche ist wirtschaftlich sinnvoll
Grundsätzlich setzt, wie erwähnt, das Boxmaß die Limits, welche unterschiedlichen Plattformen in eine Linie integriert werden können. Dabei lassen sich Fahrzeuge, die sich in Abmessungen und Aufnahmepunkten zu stark voneinander unterscheiden, nur mit hohem Aufwand in eine Fördertechnik integrieren. Bei Magna in Graz unterscheiden sich die beiden Multi-OEM-Montagelinien deshalb auch in ihren Flexibilitätsausprägungen, was etwa Fördertechnik, Hochzeit und EOL-Testing angeht.
Nicht alles, was technisch machbar erscheint, ist aber auch wirtschaftlich sinnvoll. Daher gibt es auch hinsichtlich Flexibilität Einschränkungen. Wenn Fahrzeuge sich im Fertigungsinhalt stark unterscheiden, führt dies zu großen Unterschieden bei der jeweils erforderlichen Fertigungszeit: Man spricht hier von Spreizung. Zusätzlich potenziert sich diese Spreizung mit der notwendigen Aufbaureihenfolge – wenn z.B. gleiche Fertigungsumfänge konzeptbedingt an komplett unterschiedlichen Stationen eingebaut werden müssen.
Ein weiterer Umstand betrifft die Teileversorgung, also die Logistik: Unterschiedliche Fahrzeuge benötigen unterschiedliche Teile an derselben Station. Die Anstellfläche ist allerdings auf die Stationslänge begrenzt; das macht zumeist aufwändige Vorsequenzierungen erforderlich. Bei Magna wurde mit dem automatischen Sequenzierlager aber auch dafür eine passende Lösung gefunden.
Nicht zu unterschätzen ist die Veränderung aktueller und zukünftiger Fahrzeuggenerationen hinsichtlich ihrer E/E-Architektur. E/E-Funktionen müssen durch den gesamten Montageprozess programmiert, kalibriert und getestet werden – auch hier sind unterschiedliche Hersteller-Spezifikationen zu berücksichtigen.
Getrennt und gemeinsam: die Hochzeit von Body und Antriebsstrang
Die Hochzeit – das Zusammenfügen von Antriebsstranggruppe und Karosserie – ist ein Kernprozess in der Montage. Je nach Antriebsart wird dieser Fertigungsschritt unterschiedlich durchgeführt; und je nach Hersteller gibt es unterschiedlichste Philosophien, die es auf einen gemeinsamen Nenner zu bringen gilt.
Auch hier wird bei der Multi-OEM-Fertigung nach dem Grundsatz „so viel wie möglich gemeinsam – so viel wie nötig getrennt“ verfahren. Um möglichst flexibel zu sein, sind beispielsweise die Achsvormontagen für jede Art von Antrieb direkt der Hochzeit vorgelagert; Kernprozesse wie das Fügen von Antriebsstrang und Karosserie und Verschrauben erfolgen in der automatisierten Hochzeit. Abhängig vom Batteriekonzept kann das Fügen der Batterie(n) ebenfalls gleich in der Hochzeitsstation erfolgen – oder wenn nötig in einer separaten Station.
Im Prinzip ist die Fertigung von Fahrzeugen unterschiedlicher Grundarchitektur sogar auf einer Linie umsetzbar. Dies gilt beispielsweise für Body-on-Frame-Fahrzeuge und solche mit selbsttragender Karosserie. Natürlich gibt es dabei gewisse Einschränkungen, die durch das Boxmaß bestimmt werden – dieses definiert die Kompatibilität von Länge, Breite, Höhe, Gewicht und Aufnahmepunkten. Aber gerade bei dieser Kombination muss natürlich der wirtschaftliche Aspekt noch stärker beachtet werden.
Modularität ermöglicht gemeinsame Montage trotz unterschiedlicher Fertigungstiefe
Wenn die auf einer Linie montierten Fahrzeuge eine unterschiedliche Fertigungstiefe aufweisen, kann das zu einer unwirtschaftlichen Spreizung führen, weil die unterschiedlichen Montagumfänge unterschiedlich lange Arbeitszeiten erfordern.
Auch diese Herausforderung ist aber lösbar: Die Lösung liegt in einer modular gegliederten Montage. Bei Magna in Graz gibt es in den Montagehallen diverse Möglichkeiten der bandnahen Vormontage für die Fahrzeugtypen, bei denen die Fertigungstiefe höher ist. So halten diese zusätzlichen Arbeitsgänge den Arbeitsfluss an der Linie nicht auf.
Umgekehrt gibt es über die Werkslogistik auch die Möglichkeit, vormontiert zugelieferte Module an die Linie zu liefern. Je nach Wirtschaftlichkeit oder Kundenvorgaben lassen sich auch beide Lösungen in einer Linie abbilden, um so die Spreizung der Fertigungszeiten so weit wie möglich zu reduzieren.
Auslastungssicherung der Fertigungslinie trotz Stückzahlschwankungen
Bisweilen entwickeln sich die Verkäufe für ein bestimmtes Fahrzeugmodell anders, als es die Prognosen vorhergesehen hatten – die Produktion muss angepasst werden. Je nach Konstellation der Stückzahlentwicklung kann sich hier die gemeinsame Fertigung mehrerer Fahrzeugtypen auf einer Linie günstig auswirken: Wenn sich ein neues Modell besser am Markt entwickelt als geplant, dann ist die Volumenflexibilität ein immenser Vorteil bei der Skalierung.
Denn auch wenn das eine Herausforderung für Mensch und Maschine bedeutet, besteht hier grundsätzlich die Möglichkeit, das Produktionsprogramm flexibel und kurzfristig anzupassen und damit Volumenschwankungen der einzelnen Modelle auszugleichen. Treffen die Stückzahlschwankungen jedoch die gesamte Branche, potenzieren sich diese Schwankungen bei mehreren Produkten auf einer Linie – im positiven und auch negativen Sinn.
Ein großer Vorteil der Multi-OEM Fertigung bei Magna ist aber, dass es hier möglich ist, kurzfristig und mit reduziertem Invest zusätzliche Produkte in normalen Produktionsstillständen wie dem Werksurlaub in die Linie integrieren zu können – und somit zusätzliches Volumen und eine bessere Auslastung zu erreichen.
Qualifizierte Mitarbeiter als Voraussetzung für flexible Multi-OEM-Fertigung
Die Multi-OEM-Fertigung unterschiedlicher Fahrzeuge auf einer Linie bedingt, dass vielfältigere und komplexere Arbeitsschritte pro Auto ausgeführt werden: Unterschiedliche Fahrzeuge benötigen unterschiedliche Materialen und Prozesse und somit unterschiedliche Handgriffe. Zusätzlich sind verschiedene Vorgaben und Qualitätsansprüche zu berücksichtigen.
Daher ist die Qualifikation der Mitarbeitenden ein wesentlicher Schlüssel speziell für eine erfolgreiche Multi-OEM Fertigung. Hier legt Magna großen Wert auf Schulungen und Trainings.
Der Einstieg wird den Mitarbeitenden erleichtert, indem sie zuerst in den Grundarbeitstechniken geschult werden, bevor sie an der Linie eingesetzt werden. Das Ziel dabei ist, sie langsam an die Produkte heranzuführen und ihnen nach und nach weitere Aufgaben anzuvertrauen.
Das digitale Fahrzeug: Flashen und EOL-Testing unterschiedlicher E/E-Plattformen
Die rein mechanische Montage unterschiedlicher Fahrzeugtypen oder zumindest unterschiedlicher Fahrzeugvarianten auf einer Linie ist heute eine gelöste Herausforderung. Sie ist inzwischen auch in den eigenen Produktionsanlagen der Hersteller zunehmend üblich, auch wenn Magna als Vorreiter hier durch die jahrzehntelange Erfahrung noch immer besondere Kompetenz aufweist.
Mit der weiter zunehmenden Integration neuer digitaler, softwarebasierter Fahrzeugfunktionen gewinnt aber das Flashen der Datenspeicher im Fahrzeug – also das Aufspielen aktueller Softwarestände – mehr und mehr Bedeutung. Das Programmieren der Steuergeräte beginnt bereits früh im Montageprozess und zieht sich bis in den EOL-Bereich durch.
Hier arbeitet Magna Hand in Hand mit dem Hersteller und dessen Vorgaben im Prozess. Durch die flexible und erweiterbare Gestaltung unserer Prüftechnik lassen sich hier mehrere Kundensysteme auf einer Linie realisieren; es können aber auch für neue Kunden ohne Vorgabe – die sogenannten New Entrants – perfekte Lösungen für den Gesamtumfang entwickelt und angeboten werden.
Mit diesen Schlüsselkompetenzen hat Magna als Auftragsfertiger faktisch eine Alleinstellung: ob kürzere Modellzyklen, größere Variantenzahl, kleineren Stückzahlen sowie die ansteigende Bedeutung des softwaredefinierten Fahrzeugs – in Graz sieht man den künftigen Herausforderungen jedenfalls mit freudiger Erwartung entgegen.
RESILIENZ UND NACHHALTIGKEIT: DIE LOGISTIK EINES MULTI-OEM-AUFTRAGSFERTIGERS
Nicht nur in der Fertigung selbst, auch in der Logistik hat ein Auftragsfertiger, der für unterschiedliche Hersteller produziert, besondere Herausforderungen zu bewältigen. Er arbeitet mit einer größeren Anzahl von Lieferanten zusammen und muss eine höhere Anzahl unterschiedlicher Bauteile bereitstellen.
Die Teile- und Produktionslogistik ist bei einer komplexen Fertigung wie in der Automobilindustrie immer eine herausfordernde Aufgabe. Im besonderen Maße gilt das für einen Auftragsfertiger, der für mehrere Fahrzeughersteller arbeitet. Im Vergleich zu einem Automobilhersteller, der im eigenen Werk produziert, birgt die Zusammenarbeit mit einer weitaus größeren Anzahl an Zulieferern besondere Herausforderungen.
Multi-OEM-Logistik: Unterschiedliche äußere Strukturen
In einer Multi-OEM-Fertigung sind die Rahmenbedingungen andere als in einer typischen Herstellerfabrik: Man hat unterschiedliche Produkte, die eine unterschiedliche Struktur haben. Für die unterschiedlichen Produkte haben die Hersteller unterschiedliche Sourcing-Strategien vereinbart. Verschiedene Lieferanten verwenden häufig unterschiedliche Teilenummernsysteme, Verpackungen und Ladungsträger.
Das erzeugt eine komplexere Situation als bei einer geringeren Anzahl von Lieferanten, die nach einheitlichen Systemen und mit einheitlichen Prozessen arbeiten. Die besondere Herausforderung für die Logistik eines Multi-OEM-Fertigers besteht unter anderem darin, sie trotz der unterschiedlichen Kundenanforderungen mit möglichst standardisierten Prozessen optimal zu gestalten.
Dazu kommt, dass auch die Intralogistik komplexer ist – etwa, wenn konzeptbedingt bei unterschiedlichen Fahrzeugen unterschiedliche Verbaustationen für die gleichen Module oder Komponenten erforderlich sind. Das erhöht beispielsweise die Anforderungen an die Sequenzierung intern, damit die Komponenten zeitgerecht für das jeweilige Fahrzeug an die Linie gebracht werden können. Dafür ist eine besonders präzise Steuerung der Lieferketten der vielen Lieferanten erforderlich; für die Produktion bei Magna in Graz kommen Zulieferteile und -module derzeit von etwa 1700 unterschiedlichen externen Abholorten, die im Logistik-Netzwerk verwaltet und gemanagt werden müssen.
Unterschiedliches Sourcing je nach Projekt
Wer die Zulieferer bestimmt, ist vom jeweiligen Projekt abhängig – je nachdem, wie das Sourcing vereinbart ist. Es gibt dabei eine große Bandbreite von Möglichkeiten: angefangen davon, dass der Hersteller für das Sourcing verantwortlich ist und die zu verwendenden Teile oder kompletten Module beauftragt. Am anderen Ende des Spektrums steht die komplette Übergabe des Sourcings an den Auftragsfertiger. Dieser Weg kann speziell für New Entrants attraktiv sein, die sich mit derlei Aktivitäten nicht befassen können oder möchten – und deshalb gerne alles an einen zuverlässigen Partner auslagern.
In jedem Fall muss der Auftragsfertiger aber die gesamte Logistik übernehmen: von der Inbound-Logistik (der Materialanlieferung) über die Intra-Logistik (die Prozesse im Werk) bis hin zur Outbound-Logistik, der Ablieferung der fertigen Fahrzeuge. Der Hersteller-Auftraggeber kann sich jedoch für die für ihn optimal passende Lösung entscheiden.
Transparente Lieferketten für höhere Resilienz
Nicht erst die globalen Probleme der zurückliegenden Jahre – die Covid-Pandemie, die Suezkanal-Blockade und diverse Konflikte – haben mit unerwarteten Unterbrechungen der Lieferketten gezeigt, wie vulnerabel das weltweit übliche System der Warenlieferungen ist. Ganze Branchen standen längere Zeit faktisch still, weil Material fehlte. Natürlich hat ein Auftragsfertiger in der Automobilindustrie kaum Einflussmöglichkeiten, die Ursachen für den ins Stocken geratenen Warenfluss kausal zu beseitigen. Dennoch wurden Instrumente entwickelt, um eine höhere Resilienz bei solchen Störungen zu erreichen.
Eine wichtige Strategie, die Folgen zumindest zu minimieren, ist die Etablierung einer transparenten Lieferkette. Bei Magna wird daher schon seit über 20 Jahren konsequent daran gearbeitet, auch die Transportlogistik transparent zu machen, um besser vor Störungen gewappnet zu sein. Auch vor der Pandemie gab es wiederholt weltweite Krisen, auf die hin die Störanfälligkeit der Lieferketten schmerzlich spürbar geworden ist, etwa die Weltfinanzkrise 2007 oder die Fukushima-Katastrophe 2011.
Bei Magna wurde schon 2003 ein übergreifendes Transportmanagementsystem eingeführt und seither weiterentwickelt, um Transparenz in die Lieferketten zu bringen. Faktisch wurde punktgenau einen Tag, bevor der Covid-Shut-Down in Kraft trat, das letzte Update in diesem System ausgerollt, sodass die Lieferketten von einem auf den anderen Moment wie mit einem Schalter abgeschaltet werden konnten.
Natürlich beseitigt das nicht das Problem der ausbleibenden Materiallieferungen. Aber je frühzeitiger mögliche Störungen erkannt werden, desto mehr Zeit bleibt dem Fertigungsbetrieb, zu reagieren und gegenzusteuern, um die Auswirkungen zu mindern.
Digitalisierung der Lieferkette als Voraussetzung für deren Transparenz
Der Weg, den Materialfluss vom Lieferanten über die gesamte Transport- und Logistikkette bis zur Verbaustation an der Linie sichtbar zu machen, führt unausweichlich über die Digitalisierung der Logistik. Die Digitalisierung ist hier nicht nur ein Schlagwort und Selbstzweck. Sie schafft die Möglichkeit, jederzeit für jede Materiallieferung nachvollziehen zu können, wo sie sich gerade befindet. So kann festgestellt werden, ob Störungen auf dem Weg ins Werk und an der Montagelinie auftreten und wie lange diese voraussichtlich dauern.
Bei Bedarf können geeignete Maßnahmen ergriffen werden, um einen Stillstand der Produktion zu vermeiden. Das Ziel ist dabei, dem Materialdisponenten frühzeitig den Status und die voraussichtliche Ankunft der Teile auf Teilenummernebene zur Verfügung zu stellen.
Die erste Voraussetzung dafür sind integrierte IT-Systeme. Ein gut funktionierendes ERP-System leistet die Materialbedarfskalkulation im Werk inklusive der Abrufe bei den Lieferanten. Darauf setzt das Transportmanagementsystem auf, das auf kollaborativer Ebene auch die Lieferanten und Dienstleister mit in die Prozesse einbindet. So lässt sich eine Real Time Transport Visibility erzielen – wie sie bei Magna schon seit einigen Jahren zur Verfügung steht.
Gegenmaßnahmen im Fall von unterbrochenen Lieferketten
Für hochkritische Transporte wird das Real Time Tracking bei Magna schon seit 2016 eingesetzt. Dadurch wird automatisiert gemeldet, wenn ein Transport nicht planmäßig eintreffen wird. Dies ist besonders wichtig, da mögliche Gegen- oder Ausweichmaßnahmen umso einfacher und letztendlich auch kostengünstiger umgesetzt werden können, je früher man von ihrer Notwendigkeit erfährt.
Vorteilhaft kann es für einen Multi-OEM-Fertiger wie Magna sein, wenn mehrere unterschiedliche Fahrzeuge auf einer Linie gefertigt werden – und spezifische Materiallieferungen für eines der Produkte ausfallen. Laufen etwa zwei oder drei unterschiedliche Baureihen auf einer Linie, besteht zumindest grundsätzlich die Möglichkeit, Betrieb und Auslastung der Linie temporär aufrecht zu erhalten, indem dort verstärkt die anderen Fahrzeugtypen produziert werden.
Natürlich wird das nur rentabel sein, wenn es sich um eine voraussehbar längere Störung handelt. Denn die Änderung der Produktionspläne erfordert auch wieder aufwendige Umschichtungen der Logistik, die eine gewisse Vorlaufzeit benötigen. Und es wird nur funktionieren, wenn die Auftragslage eine solche Umschichtung der Stückzahlen erlaubt.
Digitale Supply-Chain-Optimierung
Ein grundlegend neuer Ansatz ist die digitale Optimierung der Lieferkette. Bei Magna wird diese Durchleuchtung der Materiallogistik unter dem Namen DiSCO geführt – eine Abkürzung für „Digitale Supply-Chain-Optimierung“. Hinter diesem System, das vom österreichischen Bundesverband Materialwirtschaft, Einkauf und Logistik mit einem Preis ausgezeichnet wurde, steckt das Konzept der ganzheitlichen Erfassung aller relevanten Beschaffungsprozesse und -bereiche, um die Kosteneffizienz zu steigern.
Ziel ist, die Logistik-Kosten – und damit die Herstellkosten – gesamtheitlich zu minimieren, anstatt nur isoliert einzelne Kostenfaktoren zu betrachten. Denn deren Einzeloptimierungen können teilweise im Widerspruch zueinander stehen. Beispielsweise senkt zwar die Minimierung der Materialbestände die Lagerkosten, erfordert aber häufigere Transporte. Oder die isolierte Wahl des günstigsten Transportweges kann die Bestellaufwendungen erhöhen oder einen erhöhten Kommissionieraufwand erforderlich machen. Bei DiSCO wurde in Zusammenarbeit mit einem externen Partner ein mathematisches Modell und eine Methode entwickelt, um ein Gesamtoptimum zu finden.
Dabei werden die Supply-Chain-Kosten hinsichtlich der Gesamtkosten optimiert – angefangen von den Bestellkosten über den Transport, die Ladungsträgerkosten, die Manipulation im Werk, den innerbetrieblichen Transport, die Lagerhaltung und die Sequenzierung bis hin zu den Kosten des in der Ware gebundenen Kapitals im Werk wie auch auf der Transportstrecke. Durch Analyse der vorhandenen Daten wird mittels eines intelligenten Algorithmus für jedes Bauteil die optimale Lieferfrequenz ermittelt, wobei sich auch ergeben hat, dass beispielsweise ein etwas höherer Lagerbestand wirtschaftlich sein kann, wenn dadurch Transporte eingespart werden können und so die Gesamtkosten günstiger sind.
Real Time Tracking als Voraussetzung für Long Distance JIS
Bei relativ großformatigen Teilen, bei denen es zudem eine große Varianz gibt (etwa den Autositzen), ist eine Sequenzierung schon beim Lieferanten und eine JIS-Zuführung (Just In Sequence) direkt an der Linie der optimale und inzwischen branchenübliche Weg. Früher funktionierte das aber nur bei Lieferanten, die in der Nähe des Werks ansässig waren. Inzwischen funktioniert die JIS-Teilezuführung auch über größere Distanzen und längere Zeiträume.
Die Idee hinter Long-Distance-JIS ist, eine längerfristige Perlenkette aufzubauen. Über sieben oder mehr Tage hinweg wird die Reihenfolge der Fahrzeugaufträge fix gehalten. So lässt sich auch bei Zulieferungen über längere Distanzen sehr genau vorherbestimmen, wann beispielsweise welcher Sitz zum Einbau kommen muss. Dieses Programm wird auch dem Lieferanten zur Verfügung gestellt, wodurch dieser eine längere Vorlaufzeit für (wie im Beispiel) den jeweiligen definierten Sitz hat. So kann auch er seine eigene Fertigung flexibler auslasten und ist nicht mehr so eng standortgebunden.
Eine der Voraussetzungen, um das Long-Distance-JIS störsicher umsetzen zu können, war bei Magna die Einführung des Real Time Tracking bis hinunter auf die Ebene des einzelnen Lkw-Aufliegers. Deshalb wurde das MIATT genannte System – die Abkürzung steht für Magna Intelligent Arrival Trailer Tracking – bei den Long-Distance-JIS-Lieferungen zuerst eingesetzt. Damit die JIS-Teilezuführung funktioniert, müssen auch die Lkw-Auflieger ihre Sequenz beibehalten und deshalb einzeln im System erfasst und identifiziert werden können.
Papierloser Warenfluss erspart Relabeling
Ein wichtiger Schritt zur Optimierung der internen Logistik, der gleichzeitig Kosten und Aufwand spart und den Ressourcenverbrauch reduziert, war die Einführung des papierlosen Wareneingangs. Die Entladelisten werden am Tablet aufgerufen und den Mitarbeitenden standardisiert zur Verfügung gestellt. Zudem wird die angelieferte Ware durch ein standardisiertes Label, das schon vom Lieferanten aufgebracht wird, erfasst. So entfallen aufwendiges Umetikettieren und das Anbringen zusätzlicher interner Information an den angelieferten Teilen.
Intelligente Logistik dient der Nachhaltigkeit
Die gesamtheitliche Betrachtung der Logistik dient nicht nur der Kostenoptimierung – die wiederum den Kunden, also den Herstellern zugutekommt – auch der Verbesserung der Nachhaltigkeit. Denn ein Transport, der vermieden werden kann, verbraucht keine Energie und verursacht damit auch keine Emissionen.
Den gleichen Zweck verfolgt auch die digitale Lieferkettenoptimierung. Transporte können vermieden, die vorhandenen im Interesse der Effizienz besser ausgelastet werden. Deswegen ist DiSCO ein wichtiger Baustein der Bemühungen, Magna insgesamt CO2-neutral zu machen und die Produktion den Anforderungen des Umwelt- und Klimaschutzes anzupassen.
Weitere Maßnahmen auf diesem Weg, die Logistik betreffen, sind
- die Verlagerung von Transporten auf Schienen,
- die Durchführung unvermeidlicher Shuttleverkehre mit alternativen Antrieben und
- die Vermeidung von Verpackungen, indem Mehrweg-Ladungsträger und -verpackungen verwendet oder zumindest
- alle Altstoffe recycelt werden.
Viele größere und kleinere Schritte ergänzen sich hier mit Maßnahmen in anderen Bereichen der Fertigung zu einem gangbaren Weg in Richtung einer emissionsfreien Produktion der Automobilindustrie.
FAZIT: FLEXIBLE AUFTRAGSFERTIGUNG GIBT SICHERHEIT IM MOBILITÄTSWANDEL
Die Mobilitätswende ist langfristig nicht mehr aufzuhalten. Dennoch birgt sie kurz- und mittelfristig Risiken für die Automobilindustrie. Ein vollständiger Ausstieg aus der Verbrennerfertigung kann den Erfolg der gesamten Branche gefährden, da konventionelle Fahrzeuge weiterhin rentabel sein können und ihre Berechtigung haben – insbesondere in Märkten, in denen eine vollständige Umstellung auf Elektrofahrzeuge langsamer voranschreitet.
In solchen Situationen kann ein erfahrener Produktionspartner helfen. Er kann im Auftrag des OEM neue Elektrofahrzeuge fertigen oder alternativ auch die Fertigung bzw. Auslauffertigung von vorhandenen Verbrennerfahrzeugen übernehmen.
Der Trend zu kleineren Stückzahlen je Segment und einer steigenden Anzahl von Fahrzeugvarianten macht die Zusammenarbeit für Hersteller mit einem flexiblen Auftragsfertiger auch zukünftig attraktiv.
Stay connected with Inside Automotive!
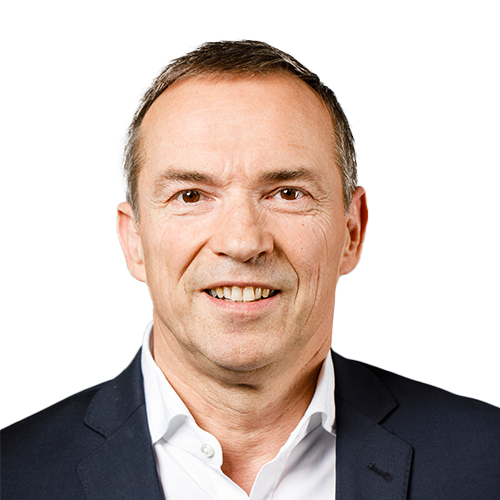
Erwin Fandl
Erwin Fandl ist seit 2019 Vice President Manufacturing bei Magna Steyr. Nach seinem Eintritt bei Magna im Jahr 1992 war er in verschiedenen leitenden Positionen in der Gesamtfahrzeugfertigung und im Qualitätsmanagement tätig. Er hat einen Abschluss als Diplom-Ingenieur an der Universität Graz.
We want to hear from you
Send us your questions, thoughts and inquiries or engage in the conversation on social media.
Verwandte Stories
Verbunden bleiben
Bleiben Sie informiert und erhalten Sie News & Stories in Echtzeit in Ihren Posteingang geliefert.