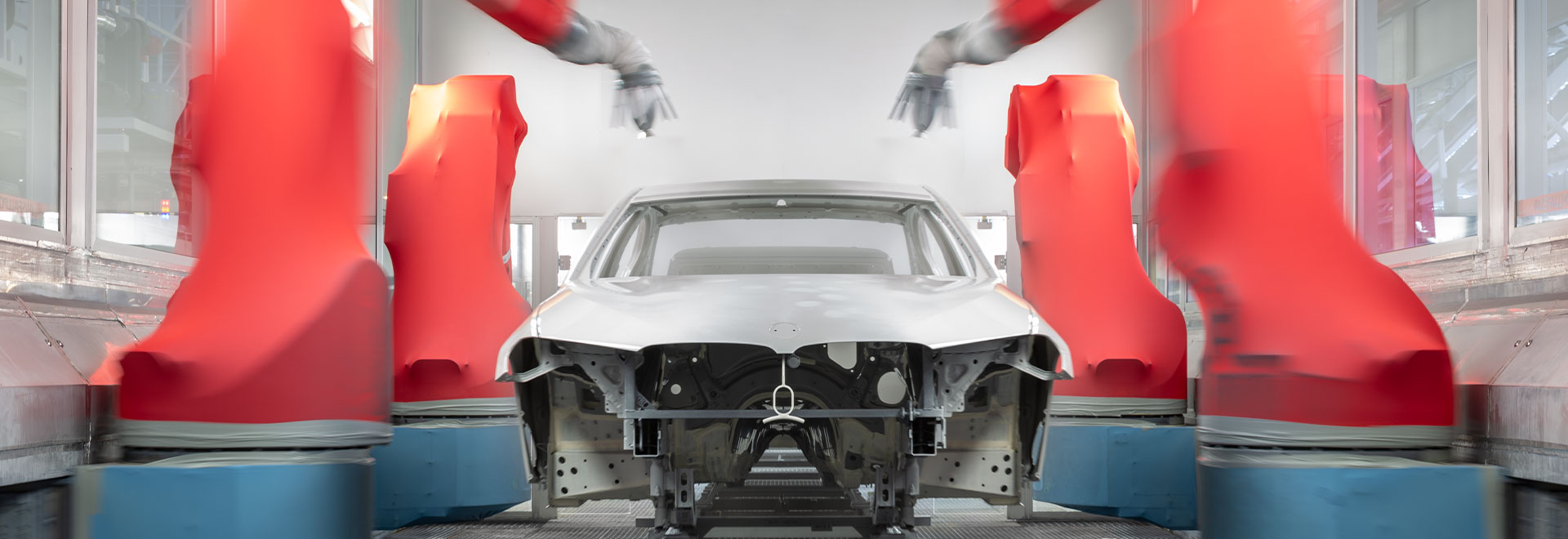
Zusammen und Getrennt – Herausforderungen in der
Lackieranlage einer Multi-OEM-Fertigung
- Klaus Pirker
- Mai 06, 2024
- 4-min read
Die Fahrzeuglackierung spielt eine Schlüsselrolle für die Fertigungsqualität eines Autos – und so ist die Lackieranlage auch eine der zentralen Stationen in der Produktion. Der Lackierprozess birgt jedoch für einen Multi-OEM-Fertiger in all seinen Schritten, von der Vorbehandlung bis zum abschließenden Decklack, besondere Herausforderungen.
Denn wenn zahlreiche unterschiedliche Baureihen auf einer Lackierlinie laufen sollen, spielen Vielseitigkeit, Flexibilität und Skalierbarkeit eine große Rolle; und dennoch darf die Effizienz ebenso wenig aus dem Blick geraten wie die Qualitätskontrolle.
FLEXIBLE GRUNDKONZEPTION DER ANLAGE
Damit die Lackieranlage für eine möglichst große Anzahl an Produktlinien geeignet ist, muss sie zunächst über ausreichend große Boxmaß verfügen.
Dafür bietet die Lackierstraße bei Magna in Graz gute Voraussetzungen.
Dort sind die Stationen so konzipiert, dass sie auch für Fahrzeuge mit überdurchschnittlicher Aufbauhöhe und Länge geeignet sind. Dadurch können nicht nur SUVs und Minivans, sondern auch Offroad-Fahrzeuge effizient lackiert werden.
Um völlig unterschiedliche Karosserien bearbeiten und bewegen zu können, werden in Graz sogenannte Skids eingesetzt: Transportschlitten, die mit unterschiedlichen Aufnahmen versehen werden. Vormontierte Aufnahmelaschen werden mit aufgesteckten oder aufgeschraubten Adaptern bestückt, die fahrzeugspezifisch sind und sich jeweils nach den Aufnahmepunkten richten. Dabei gleichen diese Adapter auch unterschiedliche Aufbaumaße aus, um Dachoberkante oder Brüstungshöhe der Karosserien auf ein einheitliches Niveau zu bringen – nicht nur aus arbeitsergonomischen Gründen.
UNTERSCHIEDLICHE ARBEITSUMFÄNGE FÜR UNTERSCHIEDLICHE PRODUKTE
Die unterschiedlichen Vorgaben der unterschiedlichen Hersteller, für die Magna produziert, können unterschiedliche Workflows erfordern – insbesondere, wenn je nach Fahrzeugprojekt zusätzliche Arbeitsgänge auszuführen sind. Deshalb muss die Lackieranlage so flexibel gestaltet sein, dass einzelne Arbeitsstationen hinzugefügt oder entfernt werden können, um den jeweils spezifischen Anforderungen der verarbeiteten Produktlinien zu entsprechen.
Dabei ist für eine Multi-OEM-Anlage ein modularer Aufbau der Arbeitsstationen vorteilhaft, denn dieser erleichtert es, bestimmte Abschnitte der Anlage speziell für die Anforderungen einzelner Hersteller anzupassen. Auf diese Weise können zusätzliche Arbeitsgänge oder spezifische Prozesse für bestimmte Produktlinien implementiert werden, ohne den gesamten Betrieb zu beeinträchtigen.
SORGFÄLTIGE PLANUNG ALS SCHLÜSSEL ZU EFFIZIENZ UND QUALITÄT
Um dabei teure und ineffiziente Rüstzeiten zu vermeiden, ist eine effizienzorientierte Planung und Koordination der Produktionsabläufe entscheidend. Die einzelnen Arbeitsgänge in der Lackieranlage müssen in der richtigen Reihenfolge und im richtigen Timing ausgeführt werden, damit die Produktion flüssig läuft – auch wenn sich die Umfänge unterscheiden. Dazu ist eine sorgfältige Abstimmung der Produktionspläne, des Materialflusses und der Ressourcen erforderlich. Das stellt sicher, dass die unterschiedlichen Anforderungen der Hersteller erfüllt werden, ohne die Qualität im Endergebnis zu beeinträchtigen.
MAXIMALE QUALITÄT DURCH STRENGE KONTROLLVERFAHREN
Eine Multi-OEM-Anlage muss hohe Qualitätsstandards erfüllen, weil sie für viele unterschiedliche Automobilhersteller arbeitet. Denn dabei sind unterschiedliche Lackierungsrichtlinien und -spezifikationen zu erfüllen. Strenge Qualitätskontrollen sind ein integraler und unverzichtbarer Bestandteil des Lackierprozesses: Um zu gewährleisten, dass die spezifizierten Qualitätsstandards durchgängig eingehalten werden, sind regelmäßige Inspektionen und laufende Tests ebenso in den Produktionsprozess eingebunden wie die Rückverfolgbarkeit eventueller Abweichungen.
EIGENES ZERTIFIZIERTES LABOR FÜR ENTWICKLUNG UND PRÜFUNG DER MATERIALIEN
Bereits die Qualität und Zusammensetzung der verarbeiteten Materialien muss den jeweiligen Anforderungen der unterschiedlichen Hersteller entsprechen. Magna kann auch diesen wichtigen Baustein eines optimalen Endergebnisses gewährleisten.
Im eigenen, zertifizierten Labor können in Zusammenarbeit mit den jeweiligen Lieferanten maßgeschneiderte Materialien entwickelt werden, die den individuellen Kundenanforderungen entsprechen. Zudem erfolgen dort alle wesentlichen Prüfungen. Dabei geht es nicht nur um das Lackmaterial selbst; Magna kann beispielsweise auch die verwendeten Klebstoffe für die Karosseriemontage im Labor prüfen: Eine Möglichkeit, die unter anderem für viele New Entrants attraktiv ist, weil diese möglicherweise noch keine eigenen Labore haben und diese Dienstleistung extern einkaufen müssen.
UNTERSCHIEDLICHE PROZESSE FÜR UNTERSCHIEDLICHE KAROSSERIEN
In der Lackieranlage bei Magna werden neben 100%-Stahlblechkarosserien und 100%-Aluminiumkarosserien auch solche in Mischbauweise beschichtet. Zukünftige Herausforderungen liegen in der BEV-Architektur, wo speziell der Schwellerbereich besonders steif ausgelegt wird und verstärkt Gussteile integriert werden, um sowohl die Insassen als auch die unterflur eingebauten Batterien bei einem Crash optimal zu schützen. Die Mischbauweise aus unterschiedlichen Materialien wird somit noch komplexer. Das bedeutet, dass die Anforderungen sowohl für Vorbehandlung und KTL-Grundierung (Kathodische Tauchlackierung) als auch für den Trockner steigen und sich verändern; denn die Aufheiz- und Abkühlrampen müssen genau abgestimmt und kontrolliert werden, weil die Wärmedehnung der unterschiedlichen Metalle – Alu und Stahl – sowie die Karosseriebauverbindungen und Klebstoffe zu berücksichtigen sind.
LOSGRÖSSEN VON von 1 BIS 280000
Die Multi-OEM-Lackieranlage bei Magna ist nicht nur in der Lage, Großserienprodukte effizient und hochqualitativ zu beschichten. Die Flexibilität der Prozesse stellt auch eine gute Skalierbarkeit für den Fall stark schwankender Produktionsvolumina sicher. Die Fähigkeit, kleine Stückzahlen und Sonderserien abzuwickeln – bis herunter zur Losgröße 1, etwa die Lackierung von Prototypen – unterscheidet die Grazer Lackieranlage von rein auf die Serienproduktion ausgerichteten Anlagen beim Hersteller selbst. Für diese Aufgaben gibt es in der flexiblen Lackieranlage zahlreiche Bypass-Linien und Sonderarbeitsplätze, an denen spezifische Tätigkeiten ausgeführt werden können, ohne dass die Serienproduktion beeinflusst wird.
FLEX-DECKLACK-KONZEPT FÜR SONDER- UND KLEINSERIEN
In der Decklack-Station sorgt die Möglichkeit einer Sonderfarbzuführung dafür, dass auch kleine Losgrößen und Einzelstücke in Großserienqualität lackiert werden können. Außer den 25 Ringleitungen, in denen die Decklacke in den Standardfarben aus den üblichen 300-Liter-Containern bereitgehalten werden, gibt es die Zuführung von Sonderfarben in 25-Liter-Gebinden, den sogenannte Hobbocks. Damit lassen sich bis zu acht unterschiedliche Sonderfarben pro Stunde lackieren, ohne den Serienprozess zu stören. Dabei helfen bewegliche Reinigungskolben in den Leitungen – ein sogenanntes Molch-System –, den Lackverbrauch zu minimieren und Spülverluste gering zu halten.
Eine vorgelagerte Maskier-Station ermöglicht zusätzlich eine hohe Flexibilität bei Teilflächen- und Kontrastlackierungen, die individuelle Vorbereitung erfordern. Und auch bei der Finalisierung gibt es Variationsmöglichkeiten: Es können drei unterschiedliche Klarlacke appliziert werden – neben dem Standard-Klarlack eine kratzfestere Beschichtung und ein Matt-Klarlack, wie er immer häufiger nachgefragt wird.
BESTE FARBTREUE AUCH FÜR ANBAUTEILE BEI SONDEREDITIONEN
Für Sondereditionen können nicht nur Karosserien und Blechteile, sondern auch Kunststoffanbauteile in der gleichen Lackieranlage lackiert werden. Karosserie und Anbauteile werden dabei direkt hintereinander mit dem gleichen Farbsystem aus dem gleichen Hobbock beschichtet; so ist sichergestellt, dass Qualität und Farbabstimmung der Anbauteile optimal zur Karosserie passen. Die Kunststoffteile werden danach in einen 80-Grad-Trockenofen gefahren, um das Material nicht zu überlasten. Diese Methode führt gerade in Klein- und Sonderserien zu einer sehr guten Farbgleichheit und Color-Harmony. Bei Anbauteilen, die in einem separaten Lackierprozess behandelt werden, ist dies schwierig zu erreichen und für Klein- und Sonderserien praktisch nicht umsetzbar.
MAGNA ALS ONE-STOP-SHOP – ALLES AUS EINER HAND
Weil in der Business Unit Lack bei Magna eine sehr breite Wissensbasis zur Verfügung steht, können neue Produktlinien sehr schnell und für den Kunden bequem und kostengünstig integriert werden. Das Team der Lackiererei kann auf Experten und Fokus-Gruppen für Simultanes-Engineering, Anlagen- und Prozessplanung, Fahrzeugsteuerung, Betriebsmittelkonstruktion und -fertigung, Applikationsexperten und natürlich eine sehr erfahrene Produktionsmannschaft zurückgreifen, was den Integrationsprozess vereinfacht und verkürzt. Die breit gefächerte und umfassende Eigenkompetenz deckt den gesamten Produktentstehungsprozess ab – von der Konzeptentwicklung über die Serienentwicklung bis hin zu Anlauf und Serienproduktion.
MIT DEM MAGNA NET ZERO PROGRAMM GERÜSTET FÜR DIE ZUKUNFT
Bei der Herstellung eines Gesamtfahrzeugs fallen für den Bereich Lackierung rund 70% der Energiekosten an. Insofern ist es eine große Herausforderung, auch diesen Produktionsbereich mit dem Magna NET ZERO Programm zu verbinden. Darin bekennt sich Magna zum Ziel, den gesamten Fertigungsprozess bis 2050 zu 100% nachhaltig zu gestalten. Zur Erreichung dieses Ziels im Bereich Painted Body wurde bereits jetzt ein Transformationsprozess namens Paint Strategy 2.0 begonnen. Es wird Energietransparenz geschaffen, Energieeffizienz in den Anlagen gefördert und auf erneuerbare Energien schrittweise umgestellt. So wird die seit 30 Jahren betriebene Lackieranlage fit für die Zukunft – mit der Vision, gleichermaßen Flexibilität, Wettbewerbsfähigkeit und Nachhaltigkeit zu erreichen.
Stay connected with Inside Automotive!
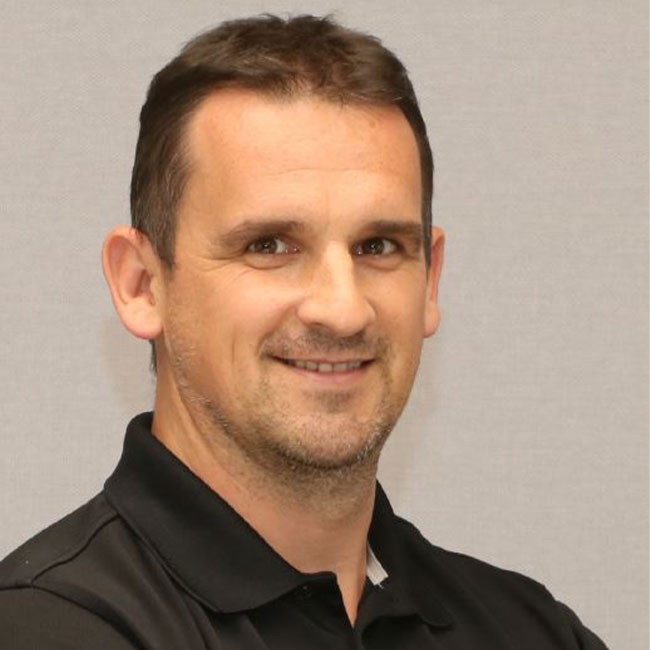
Klaus Pirker
Klaus Pirker arbeitet seit dem Jahr 2000 bei Magna Steyr in Graz. Zunächst war er als Prozessplaner in der Lackiererei tätig. In den folgenden Jahren hat er verschiedene Positionen in der Planung und als Technologie Projektleiter bei Fahrzeug Projekten innegehabt. Ab 2013 war er Gruppenleiter für den Bereich Lackiererei sowohl in Graz als auch global. Ab 2015 hat er zusätzlich den Bereich Karosseriebau geleitet. Seit Mitte 2021 ist er nun Abteilungsleiter für den Bereich CoC Paint Body.
We want to hear from you
Send us your questions, thoughts and inquiries or engage in the conversation on social media.
Verwandte Stories
Verbunden bleiben
Bleiben Sie informiert und erhalten Sie News & Stories in Echtzeit in Ihren Posteingang geliefert.