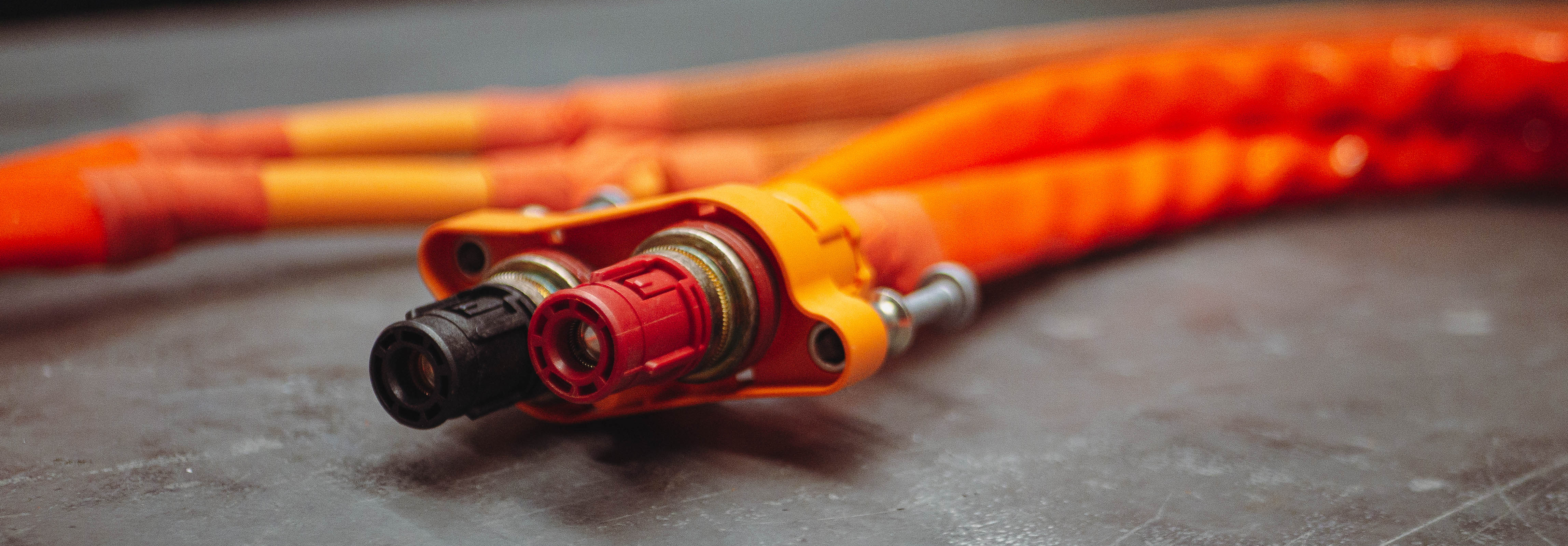
BATTERY TESTING BRINGS NEW CHALLENGES FOR PASSIVE SAFETY
Battery testing poses a challenge not only for new entrants to the automotive market, particularly the BEV market, but also for established car manufacturers. The specialized tests required to demonstrate battery safety cannot be easily conducted at their own crash test facilities. Magna's Vehicle Safety & Testing site in Sailauf, Germany has experience as a development partner in the field of "Passive Safety." Early on, they encountered the requirements for battery systems through crash tests on high-voltage vehicles. Expanding competencies into battery component testing is a logical extension of their portfolio. Collaboration with a development specialist is advantageous for vehicle manufacturers because it allows them to share the necessary high investments and risks. Additionally, it enables the car manufacturer to focus on their core competencies.
IT ALL STARTS WITH STANDARDS: DEVELOPING TEST PROCEDURES AND TEST BENCHES FROM LEGAL REGULATIONS
At the beginning of E-mobility, regulations and laws had to be developed to supplement the requirements for conventional, internal combustion engine (ICE) vehicles. Initially, there were neither test procedures nor the appropriate hardware and infrastructure to conduct the necessary tests. Over time, processes have been established, and standards for battery testing have solidified. This process is comparable to the development of overall vehicle safety: Initially, there were only rough requirements to be met; with the precise definition of requirements and the establishment of corresponding standards, test processes and facilities have evolved.
In recent years, a lot of pioneering work has been done to ensure battery tests are future-proof and professional. Most of the battery testing facilities at Magna are proprietary developments, with few existing models to follow.
ENERGY DENSITY VS. SAFETY - CONFLICTING GOALS IN BATTERY DESIGN
Vehicle manufacturers naturally aim to achieve maximum energy storage in the drive battery with minimal space and weight, as this is a tangible advantage for the end customer, ultimately determining the vehicle's market success. However, increasing energy density also means that the consequences of an unintended event or accident become more severe.
Manufacturers must ensure that suitable protective mechanisms prevent a "thermal runaway" or "thermal propagation" in the event of a battery defect. There must be sufficient time for occupants to safely exit the vehicle. This proof must be provided through testing.
THE TESTS: FOCUS ON SAFETY
One of the fundamental regulations for battery testing is the UN-R 100, which outlines the requirements for the approval of electric vehicles. Central to this are aspects of electrical safety and the battery's resistance to external impacts, both during vehicle operation and in the event of an accident.
Not only complete batteries are tested; there are also tests at the cell or module level. In these cases, the battery manufacturer usually commissions the test rather than the vehicle manufacturer. At the other end of the spectrum, the entire vehicle may be tested, which is relevant because the battery housing is increasingly integrated as a structural element in the vehicle architecture, and the battery and its components are tested dynamically in near-realistic accident scenarios.
An experienced provider of vehicle safety and battery tests can ensure compliance with relevant regulations comprehensively. While specific tests may be outsourced depending on the case, most are conducted in-house. Magna's new battery laboratory in Sailauf, Lower Franconia, which has been continuously developed since 2019, can conduct many relevant tests.
WHAT IS TESTED? – TORTURE FOR BATTERIES
The tests are divided into different areas. Temperature and humidity tests demonstrate that the battery operates correctly under extreme environmental conditions without entering a critical operating state. Vibration and shock tests check whether the battery withstands specific stresses that can occur in a vehicle, unlike stationary batteries. Electrical tests include performance testing of the battery, such as conducting charge and discharge cycles under various climatic conditions.
Extensive and important are the so-called abuse tests. These start with electrical "abuse," such as reactions to overcharging or undercharging, external or internal short circuits, or interruptions in connection or internal wiring. Mechanical resistance to deformation is also tested. Intrusion tests ensure that the battery housing withstands impacts from below, as might occur in accidents. Batteries are dropped from defined heights, subjected to sudden pressure from different directions, and rotated to simulate a rollover accident.
THE ULTIMATE TEST: SAFETY AGAINST THERMAL PROPAGATION
The worst-case scenario for a high-voltage battery is thermal propagation, where a temperature increase in one cell triggers a chain reaction throughout the battery. Propagation is usually initiated by overheating a module or intruding a test nail. This scenario must be tested, as there are specific regulations on how long the battery must withstand.
Such incidents are induced under controlled conditions. Magna has a specially secured and enclosed test room in a hall where the battery is driven into propagation. A sophisticated safety concept ensures the fire remains controlled, and the resulting smoke gases are safely extracted and treated.
SPECIAL CHALLENGES IN HV
BATTERY TESTING
Most abuse and safety tests are destructive, meaning the test cannot be repeated. The test pieces are extremely expensive and often limited per development stage. Therefore, extraordinary care in planning and conducting tests is necessary; nothing must go wrong, and tests must be meticulously prepared and executed in a specific sequence.
As in all areas of automotive development, there are multiple development stages for batteries. Any change to the battery or its peripherals, such as the battery management system or charging system, that affects behavior requires retesting. Changes to the rest of the vehicle during development can also alter battery safety behavior and necessitate further tests.
CHANGES IN HV BATTERY TESTING
With the advancement of battery technology, test procedures must continually evolve. Higher battery capacities require different test and measurement equipment. Tests themselves are becoming more sophisticated, precise, refined, and standardized—overall more professional.
A prime example is propagation testing: Previously, tests were conducted outdoors in remote areas. Depending on the country, many test service providers still do this. At Magna, propagation is conducted indoors, avoiding environmental hazards and health risks for employees while significantly improving test reproducibility under standardized conditions.
THE FUTURE OF HV BATTERIES AND HV BATTERY TESTING
Battery development is rapidly progressing, with constant research into new battery concepts. Energy density has markedly increased over the past decades, driven by new battery designs. Some new battery types present additional challenges, while others may simplify testing. For example, solid-state batteries, which are promising and operate without liquid electrolytes, likely pose fewer issues with thermal propagation than the currently predominant lithium-ion batteries. Other battery developments may introduce different problems. Propagation test requirements will change, and tests must adapt accordingly. Different temperatures and cell reactions in penetration cases will evolve alongside battery development.
It is certain that HV battery testing will become even more significant in the future. The shift towards E-mobility is inevitable, and new systems and developments require new tests—not only to advance performance but also for safety, which remains a key concern for end customers hesitant to adopt BEVs. Professional battery testing also contributes to sustainability: Enhanced battery safety reduces the likelihood of environmentally hazardous substances being released in accidents.
Stay connected with Inside Automotive!
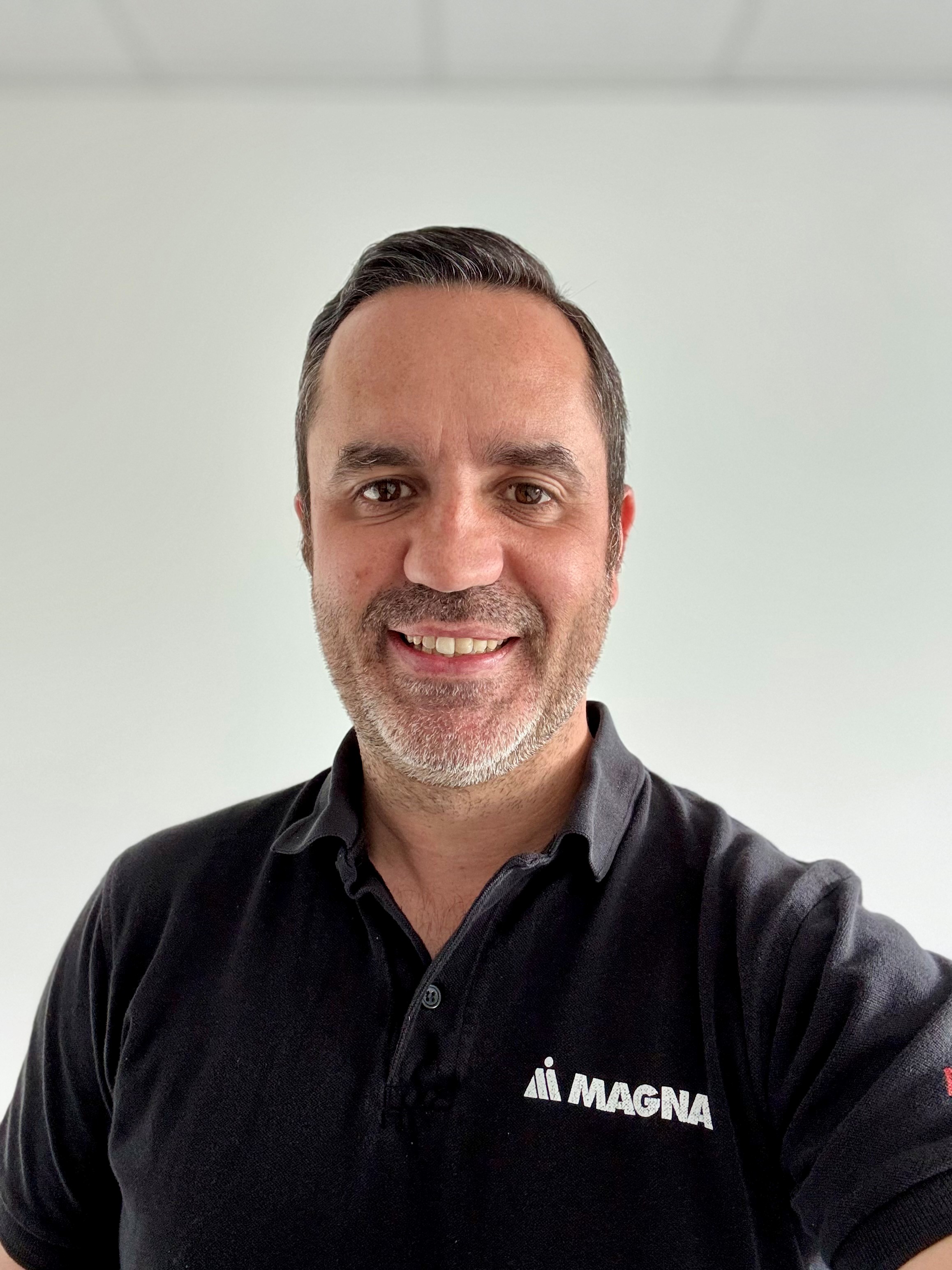
We want to hear from you
Send us your questions, thoughts and inquiries or engage in the conversation on social media.
Related Stories
Stay connected
You can stay connected with Magna News and Stories through email alerts sent to your inbox in real time.