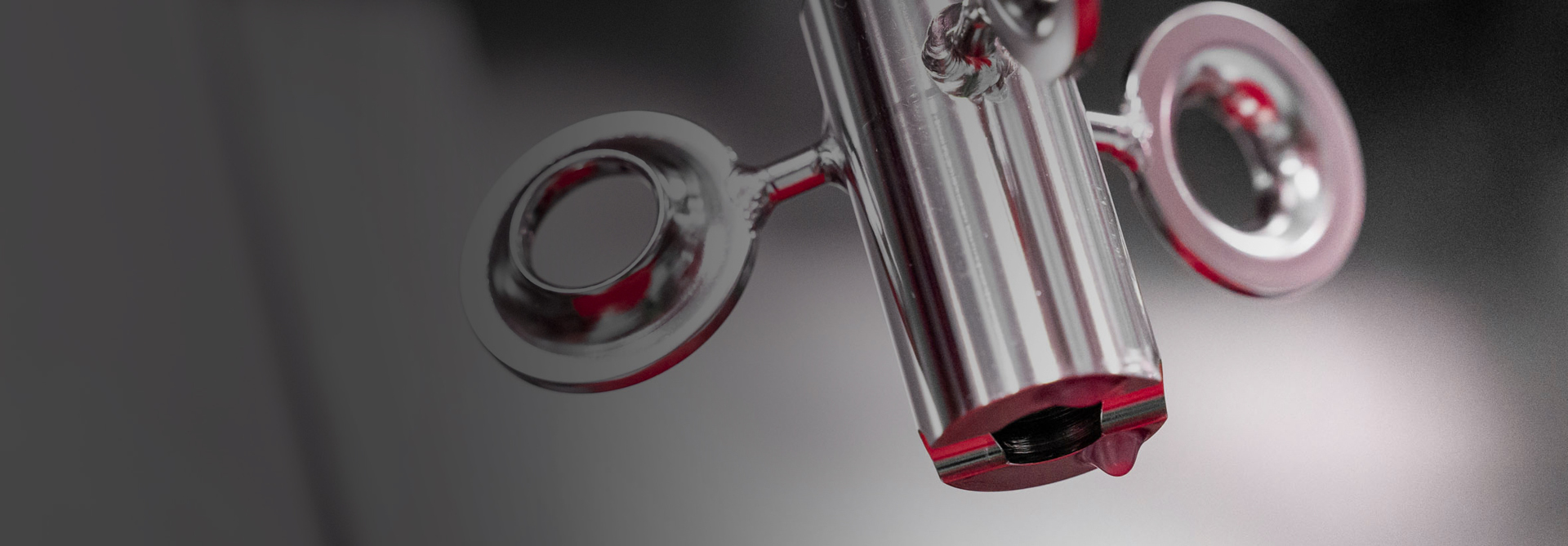
AM ANFANG WAR DIE SONDERSERIE
Als flexibler Auftragsfertiger der Automobilindustrie hatte und hat Magna in Graz seit jeher mit Klein- und Sonderserien zu tun. Deshalb lautete eine wichtige Anforderung für die Lackiererei, auch mit kleinen Stückzahlen und Sonderfarben umgehen zu können. Im normalen Lackierprozess, wie er in der Serienproduktion angewendet wird, ist das aber ein Problem. Denn Kunststoffanbauteile wie etwa Stoßfänger oder Radkastenblenden können den normalen Prozess nicht durchlaufen. Sie würden das Einbrennen der Lackierung bei den üblichen 140°C nicht schadlos überstehen.
Deswegen müssen sie üblicherweise getrennt von der Blechkarosserie lackiert und getrocknet werden. In der Großserienproduktion werden die Kunststoffteile daher meist bereits endlackiert angeliefert. Dies ist aber für Klein- und Kleinstserien nicht praktikabel, denn die Lieferanten sind auf große Stückzahlen ausgerichtet.
Als Ausweg aus diesem Dilemma wurde ein Niedrigtemperatur-Lackierprozess entwickelt, der es ähnlich wie auch bei der Karosserieinstandsetzung ermöglicht, Kunststoffanbauteile unversehrt mit durch den Lackierprozess laufen zu lassen. Dazu senkt man die Einbrenntemperatur von 140°C auf rund 80°C ab.
ANDERE MATERIALIEN UND ANDERE PROZESSE FÜR DAS NIEDRIGTEMPERATURLACKIEREN
Dabei ist es aber nicht damit getan, einfach die Temperatur im Trockenofen herunterzufahren. Zwar lässt sich der Niedrigtemperatur-Lackierprozess grundsätzlich in einer bestehenden Lackieranlage implementieren. In jedem Fall müssen aber andere Materialien verwendet werden. Dabei sind Lacke, insbesondere Klarlacke, erforderlich, die schon bei Temperaturen weit unter den üblichen 140°C eingebrannt werden können und auch dabei schon ihre Endfestigkeit erreichen. Soweit es um Kunststoffteile geht, benötigt man besondere Haftvermittler, um eine gute Verbindung der Beschichtung mit dem Bauteil zu erreichen.
Je nach Einzelfall können die nötigen Veränderungen bis in den Karosserierohbau hineinreichen: Moderne Fügetechniken, bei denen Blechteile – etwa Aluminiumteile – verklebt statt punktgeschweißt werden, können darauf abgestimmt werden, dass die finale Festigkeit der Verklebung erst im Trockenofen erreicht wird. Auch hier ist anderes Material zu verwenden, das die hohen Temperaturen nicht benötigt.
GEÄNDERTE TECHNOLOGIEN UND PROZESSE
Auch im Prozess, an den Werkzeugen und den Vorrichtungen sind Änderungen erforderlich. Das fängt schon beim Lackauftrag an. Wenn Kunststoffteile, die von sich aus nichtleitend sind, lackiert werden sollen, funktioniert die elektrostatische Lackierung nicht wie gewohnt. Es sind andere Zerstäuber nötig, denn die üblichen ESTA-Finger, also die elektrostatischen Applikatoren, könnten ungeeignet sein.
Alternativ oder ergänzend muss man zusätzliche Maßnahmen ergreifen, um eine leitfähige Oberfläche auch an Kunststoffteilen herzustellen. Etwa, indem zuvor leitfähige Primer aufgetragen oder freiliegende Pins in leitfähigen „Jigs“ vorgesehen werden.
Als finaler Schritt muss man auch den Polierprozess ändern. Niedrigtemperaturlackierte Teile, namentlich Kunststoffteile, können nicht im üblichen Polierprozess behandelt werden, weil sie generell schlechter polierbar sind. In viele Fällen ist es sinnvoller, fehlerhafte Teile auszuschleusen und den Lackierprozess zu wiederholen.
IN EINEM RUTSCH: ANBAUTEILE ZUSAMMEN MIT DER ROHKAROSSERIE LACKIEREN
Für Sonderserien mit spezieller Lackierung werden Anbauteile, die mitlackiert werden sollen, auf entsprechende Gestelle montiert und getrennt von der Karosserie durch die Decklacklinie gefahren. Man brennt sie separat in einem zweiten, auf die niedrigere Temperatur eingestellten Trockenofen ein. Ziel ist aber, diese Teile zusammen mit der Karosserie zu lackieren, was den Gesamtaufwand reduziert. Denn das ist einer der größten Vorteile des Niedrigtemperatur-Lackierprozesses.
Allerdings werden die Anbauteile dabei nicht auf dieselbe Weise an die Karosserie montiert wie in der Endmontage. Es sind spezielle Hilfsgestelle und Aufnahmen zu konstruieren, die an der Karosserie angebracht und mit denen die Anbauteile in Einbaulage fixiert werden. Natürlich muss man die hierfür erforderlichen Arbeitsstationen in den Durchlaufprozess der Karosserie durch die Lackieranlage integrieren.
Letztlich verringert aber die Lackierung der Anbauteile zusammen mit der Karosserie im Vergleich mit der Getrenntbehandlung den Arbeitsaufwand. Und sie ermöglicht eine effiziente und qualitativ hochwertige Niedrigtemperaturlackierung, welche die hohen spezifischen Anforderungen in der Automobilindustrie erfüllt.
GEÄNDERTE, TEILS UMFANGREICHERE VORBEHANDLUNG ERFORDERLICH
Bei den Stahl- und Aluminiumteilen erfordert das Lackieren im Niedrigtemperaturverfahren im Wesentlichen keine andere Vorbereitung als im Hochtemperaturverfahren. Anders sieht es bei Kunststoffteilen aus: Je nach Anlieferzustand der Anbauteile – komplett roh und möglicherweise verschmutzt, oder bereits geprimert und grundiert – sind zusätzliche Arbeitsschritte notwendig.
Um eine gute Haftung zu erreichen, müssen die Teile möglicherweise geflämmt und/oder gewischt werden, bevor der Primer aufgebracht wird. Je nach Zustand ist zuerst auch eine Reinigung und Entfettung nötig. Wie bei der Karosserie ist die perfekte Vorbereitung wichtig, um ein gutes Lackierergebnis zu erzielen.
KONTROLLEN UND PRÜFUNGEN ZUM AUFRECHTERHALTEN DER QUALITÄT
Grundsätzlich ist bei jedem Lackierprozess eine sorgfältige Kontrolle der Qualität der Lackierung erforderlich. Hier unterscheidet sich der Niedrigtemperaturprozess nicht von der klassischen Hochtemperaturmethode. Denn das Ergebnis, die Oberflächenqualität, muss in jedem Fall den hohen Anforderungen der Fahrzeuglackierung entsprechen. Die genauen Verfahren können je nach Kundenanforderung variieren.
Üblich sind neben visuellen Inspektionen der fertigen Fahrzeuge Lackdickenmessungen, Haftungstests und auch Farbanpassungen. Bei letzterem Punkt ist der Niedrigtemperatur-Lackierprozess im Vorteil. Wenn man Karosserie und Anbauteile zusammen in einem Durchgang lackiert, wird der objektive Farbeindruck (auch Colormatch genannt) präziser zusammenpassen als bei der Getrenntlackierung. Die Lackdickenmessung auf Kunststoffteilen muss man allerdings mit anderen Verfahren durchführen als auf Blechteilen, weil die gängige Methode auf dem nichtleitenden Kunststoff nicht einsetzbar ist.
Grundsätzlich müssen die unterschiedlichen Kontrollschritte genauer dokumentiert werden, wenn Kunststoffanbauteile mit in den Lackierprozess integriert werden. Denn Kunststoffteile lassen sich kaum reparieren, wenn während der Beschichtung ein Fehler sichtbar wird, der möglicherweise schon vorher angelegt war oder im Prozess entstanden ist. Das Teil gilt dann als Ausschuss und muss durch ein neues ersetzt werden. Allerdings muss man bei diesem den gesamten Lackaufbau wieder neu durchführen. Deshalb ist eine rigorose Dokumentation der Prozessdaten nötig, um ein effektives Claim Management zu gewährleisten.
VORBEREITUNG UND SCHULUNG DER ARBEITSKRÄFTE IN DER LACKIEREREI
Eine hohe Ergebnisqualität und eine reibungslose Umstellung auf neue Prozesse kann immer nur dann erreicht werden, wenn auch die Mitarbeiter_innen in der Lackiererei zuvor gut vorbereitet werden. Im Fall der Niedrigtemperaturlackierung wird der Mehraufwand gering sein, was die Karosserie selbst angeht, weil die Prozesse grundsätzlich die gleichen bleiben. Allerdings müssen andere Anforderungen im Bereich des Klarlack-Finish-Prozesses bei Anbauteilen berücksichtigt werden, weil der Polierprozess sich verändert. Man darf beim Polieren von Kunststoffteilen nicht zu viel Wärme einbringen.
Im Bereich der Anbauteile wird je nach Prozessaufwand ein erhöhter Schulungsaufwand erforderlich – insbesondere, was die Reinigung, Beflämmung, Haftvermittlung und Lackiereffizienz angeht. Magna als Auftragsfertiger ist durch die langjährige Erfahrung mit Sonderserien, bei denen Anbauteile im Werk lackiert werden, im Vorteil, da bereits Know-how in der Behandlung von unterschiedlichsten Kunststoffteilen vorhanden ist. In den eigenen, primär auf Großserienproduktion ausgerichteten Werken der Automobilhersteller darf man dies nicht voraussetzen.
Ähnliches betrifft auch die Ausrüstung der Lackiererei: Weil der Niedrigtemperatur-Lackierprozess für diese besonderen Fälle schon länger umgesetzt wird, verfügt die Lackiererei in Graz über zwei Trockenöfen – einen für das konventionelle 140°C-Einbrennen, und einen für das Niedrigtemperaturhärten bei 80°C. Das ist bereits jetzt ein USP gegenüber den meisten anderen Lackieranlagen der Automobilindustrie.SCHNELLER ODER LANGSAMER? NIEDRIGTEMPERATUR-LACKIERPROZESS UND PRODUKTIVITÄT
Einerseits erhöht das Arbeiten im Niedrigtemperatur-Lackierprozess unter Einbeziehung der Anbauteile prinzipiell die Wertschöpfung beim Auftragsfertiger. Das kann sich für den OEM in Form eines günstigeren Fahrzeuggesamtherstellpreises auszahlen. Dabei steigert die Lackierung von mehr Fahrzeugteilen innerhalb der Taktzeiten (wenn Anbauteile gleichzeitig mit der Karosserie mitlackiert werden) grundsätzlich die Produktivität. Auch die schnellere Polierbarkeit kann den Durchsatz erhöhen und gleichzeitig den Energiebedarf für Kühlzonen verringern.
Andererseits kann die Prozessbestückung der Teileträger und Hilfsgestelle den Durchlauf verlangsamen und einschließlich entsprechender Teilepuffer zusätzlichen Flächenbedarf bedingen. Und je nach Prozesstiefe können eventuell längere Trocknungs- und Aushärtezeiten dazu führen, dass letztlich weniger Fahrzeuge pro Tag lackiert werden können.
DER EINFLUSS DES NIEDRIGTEMPERATUR-PROZESSES AUF DIE PRODUKTQUALITÄT
Ein Vorteil der gemeinsamen Lackierung von Karosserie und Anbauteilen ist die weitestgehende Eliminierung von Farbabweichungen. Das vereinfacht und verkürzt den Colormatch- bzw. Colorharmonieprozess und reduziert damit die Integrationszeit. Die niedrigere thermische Belastung reduziert außerdem die Spannungen, die beim Einsatz von Multimaterialien – etwa der Kombination von Stahl und Aluminium – durch die unterschiedlichen Wärmeausdehnungskoeffizienten entstehen. Und dies trägt zu einer gleichbleibend hohen Qualität der Lackschicht bei.
Obwohl ständig Fortschritte bei der Lackentwicklung gemacht werden, sind Klarlacke, die bei niedrigerer Temperatur eingebrannt werden, jenen bei 140°C eingebrannten in der chemischen und mechanischen Haltbarkeit nicht ebenbürtig. Insbesondere bei der Kratzfestigkeit erreichen sie aktuell noch nicht deren hohes Niveau. Zudem sind genauere Prozesskontrollen erforderlich, weil die Prozessfenster für Vernetzung und Aushärtung enger sind.
Allerdings kann man Nutzen und Notwendigkeit der extrem hohen Beständigkeit heutiger Hochtemperatur-Klarlacke auch anzweifeln. Denn eine niedrigere Kratzfestigkeit bei Anbauteilen ist heute ohnehin schon bei solchen Fahrzeugen zu beobachten, deren Karosserie im Hochtemperaturverfahren lackiert wurde, die Kunststoffteile aber notwendigerweise bei niedrigeren Temperaturen – in der Großserie meist schon beim Lieferanten.
Demnach „altern“ Stoßfänger, Schürzen und andere Kunststoffelemente schneller und somit entwickeln sich nach längerer Einsatzdauer die Oberflächen quasi auseinander. Wird alles zusammen im Niedrigtemperatur-Lackierprozess lackiert, „altern“ Anbauteile und Karosserie sozusagen gemeinsam.
Natürlich sind hier Prognosen schwierig. Aber es ist zu erwarten, dass die Anforderungen vieler Autohersteller und OEMs – insbesondere der deutschen Premium-Marken – mittelfristig auf ein realistischeres Maß zurückgehen, was die Widerstandsfähigkeit der Karosserieoberflächen angeht. Einige Hersteller haben bereits begonnen, auch Teile der Außenhaut im Niedrigtemperaturverfahren zu behandeln, wie etwa kontrastlackierte Fahrzeugdächer. Und im Nutzfahrzeugbereich sowie bei einigen Kleinserien-Sportwagen ist die Niedrigtemperaturmethode ohnehin bereits industrialisiert.
GEHÖRT DEM NIEDRIGTEMPERATUR-LACKIERPROZESS DIE ZUKUNFT?
Der zentrale Vorteil des Niedrigtemperatur-Lackierprozesses ist der insgesamt geringere Energiebedarf und damit der Fortschritt bei der Dekarbonisierung der Automobilproduktion. Dieser Aspekt gewinnt immer mehr an Bedeutung. Damit einher geht naturgemäß auch eine Verringerung der Energiekosten. Deshalb beschäftigen sich faktisch alle Autohersteller und OEMs damit, die Temperaturen im gesamten Beschichtungs- und Lackierprozess zu senken, um den Energieaufwand zu reduzieren und somit den CO2-Fußabdruck der Produktion zu verkleinern.
Einerseits geschieht dies aus Kostendruck; andererseits aber auch, um gesetzliche Auflagen und Vorgaben für eine nachhaltige Produktion zu erfüllen. Denn weil die Lackiererei der energieintensivste Teil der gesamten Autoproduktion ist, stellt die Niedrigtemperaturlackierung – verglichen mit anderen Bemühungen, die CO2-Emissionen in der Autoproduktion zu reduzieren – eine „Low Hanging Fruit“ dar. Denn durch sie kann man sehr große Verbesserungen erreichen.
Das betrifft nicht allein den Decklack, sondern umfasst auch vorangegangene Schritte, etwa schon die KTL-Tauchlackierung. Beim Decklack können künftige Entwicklungen den Niedrigtemperatur-Lackierprozess weiter fördern: Um etwa weitere Sensoren für das automatisierte Fahren der Levels 3 und 4 unterzubringen, ist es vorteilhaft, größere Teile der Karosserieaußenhaut aus Kunststoff zu fertigen. Hier schafft die Niedrigtemperaturlackierung größeren Spielraum und mehr Freiheiten im Produktdesign durch den Einsatz von Verbundwerkstoffen. Und auch im Leichtbau ist damit eine größere Materialvielfalt darstellbar.
Der generelle Trend zu kürzeren Modellzyklen und somit geringeren Gesamtstückzahlen, verbunden mit einer insbesondere im Hochpreissegment steigenden Nachfrage nach Individualisierung und Sonderfarben, kann die Bedeutung der Niedrigtemperatur-Lackierprozesses weiter erhöhen. Denn damit lassen sich Klein- und Sonderserien leichter darstellen. So deutet vieles darauf hin, dass die Niedrigtemperaturlackierung in Zukunft eine bedeutende Rolle in der Automobilindustrie spielen wird, da sie ökologische mit ökonomischen Vorteilen verbindet.
Stay connected with Inside Automotive!
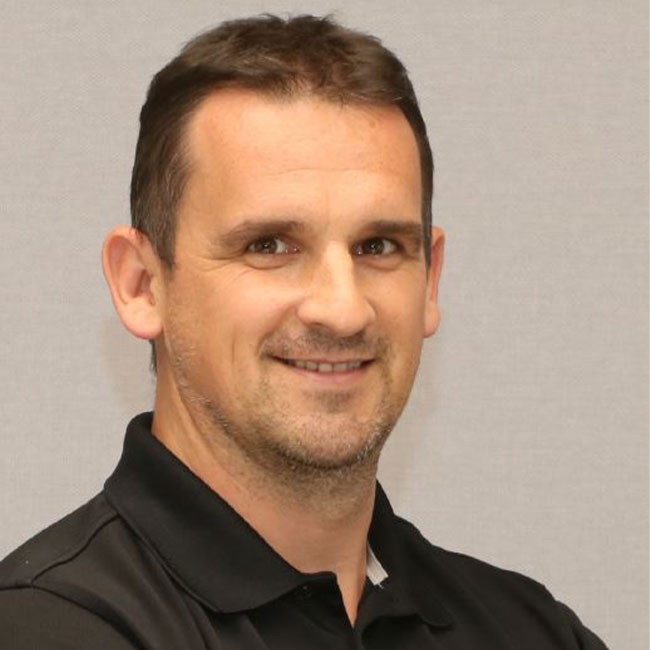
We want to hear from you
Send us your questions, thoughts and inquiries or engage in the conversation on social media.
Verwandte Stories
Verbunden bleiben
Bleiben Sie informiert und erhalten Sie News & Stories in Echtzeit in Ihren Posteingang geliefert.