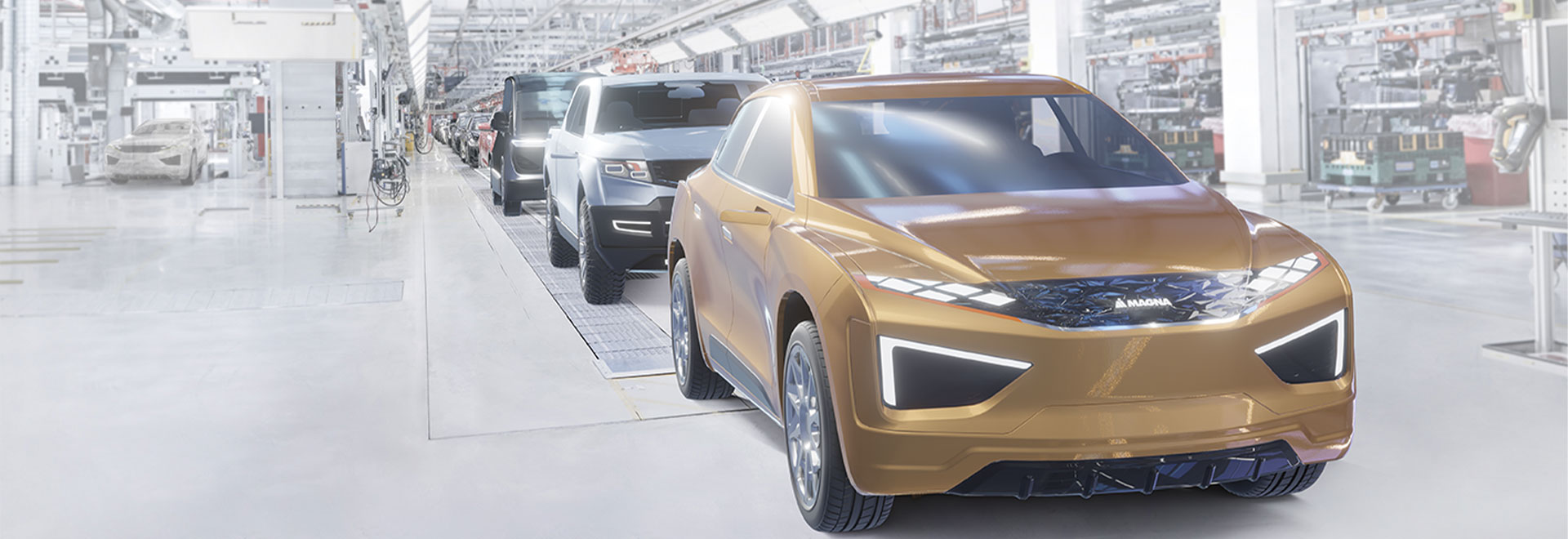
Flexible Produktion in der Automobilindustrie durch Multi-OEM-Auftragsfertigung
- Erwin Fandl
- Januar 08, 2024
- 5-min read
Die Mobilität ist im Wandel – und das auf verschiedene Weisen. Nicht nur die Produkte selbst ändern sich, wie steigende Marktanteile bei Fahrzeugen mit alternativen Antriebssystemen zeigen, sondern auch die Einstellung in der Gesellschaft zur Mobilität, etwa durch das allgemein höhere Umweltbewusstsein. Das alles führt zu sich wandelnden Anforderungen und Erwartungen bei Autokäufern, bei denen die neuesten Fahrassistenz- und Infotainment-Features klassischen Fahrzeugattributen wie Leistung und Fahrverhalten inzwischen starke Konkurrenz machen. Die Automobilindustrie muss also ihr Produktangebot so ändern, dass es zu den Herausforderungen der Zukunft passt und auch in der Produktion entsprechend neue Wege gehen. Als Lösung dafür bietet sich flexible Produktion bei einem erfahrenen Herstellungspartner an.
NÖTIGE VERÄNDERUNGEN IN DER AUTOMOBILINDUSTRIE
Derzeit drängen nicht nur viele neue Anbieter (New Entrants) insbesondere aus dem asiatischen Raum mit elektrischen Autos in den europäischen Markt; auch die etablierten OEMs arbeiten mit Hochdruck an der Transformation ihrer Modellpalette. Manche von ihnen haben vielleicht auch die Geschwindigkeit des Wandels unterschätzt. Diese hat durch die Verwerfungen der letzten Jahre von Covid-19 bis zu den jüngsten geopolitischen Ereignissen und die dadurch bedingten Lieferengpässe noch einmal zugelegt.
DER TREND ZU KLEINEREN STÜCKZAHLEN
Insgesamt geht die Tendenz zu geringeren Stückzahlen je Fahrzeugsegment, die zudem schwieriger vorhersagbar sind. Angesichts der vielen Marktneuzugänge bleiben die Absatzzahlen nach der Einführung eines neuen Fahrzeugs weniger lang stabil, weil ein neues Modell technologisch schneller veraltet ist: Die Volumina flachen schneller ab, der gewohnte Sieben-Jahres-Modellzyklus ist nicht mehr selbstverständlich. Außerdem spaltet sich der Markt immer weiter auf. Einerseits werden immer mehr unterschiedliche Karosserievarianten auf einer Plattform entwickelt, um den Wunsch der Kund_innen nach Individualität zu erfüllen. Andererseits werden auch mehr Nischenmodelle und Sonderserien entwickelt und aufgelegt, etwa um das schon nach wenigen Jahren nachlassende Kaufinteresse wieder zu wecken.
All diese Zusatzversionen können mit ihren zumeist eher geringen Stückzahlen den Ablauf der Produktion in den auf Großserien ausgerichteten Werken der OEMs stören: Nischenmodelle sind schwierig in eine bestehende Linie zu integrieren, die grundsätzlich auf hohe Stückzahlen eines Modells ausgelegt ist. Zudem ist oft schwer abzuschätzen, ob das neue Fahrzeug bei den Kund_innen gut ankommt – oder ob unkontrollierbare äußere Einflüsse insgesamt zu einer Abschwächung des Marktes führen. Die Produktion muss also skalierbar sein, was in den Stammwerken der OEMs nicht immer ohne weiteres möglich ist.
Auch viele New Entrants der Automobilindustrie starten zunächst mit relativ kleinen Stückzahlen am Markt. Für sie ist eine skalierbare, flexible Produktion besonders wichtig, um nicht unnötig hohe Kapazitäten aufbauen zu müssen. Sie müssen jedoch weiterhin in der Lage sein, einer unerwartet höheren Nachfrage schnell nachkommen zu können.
MEGATREND ELEKTRIFIZIERUNG - UND DIE BESTE REAKTION DARAUF
Einer der wichtigsten globalen Megatrends in der Automobilindustrie ist das derzeitige Bemühen um Nachhaltigkeit und CO2-Reduktion. Daraus resultierend ändern sich zusehendes die Marktanforderungen vom traditionellen Verbrennungsmotor hin zu alternativen Antrieben und batterieelektrischen Fahrzeugen.
Die etablierten OEMs wählen dabei unterschiedliche Wege, um diese Herausforderung zu bewältigen. Die Entwicklung neuer, elektrisch angetriebener Fahrzeuge ist nur der erste Schritt, den die meisten traditionellen Hersteller schon gegangen sind. Die Herausforderung ist nun, die neuen Elektrofahrzeuge in ihre bestehenden Produktionsabläufe zu integrieren. Dabei bauen manche OEMs komplett neue Fertigungsanlagen für diese Modelle, während die Verbrenner auf den vorhandenen Fertigungsanlagen weiterlaufen, um das traditionelle Marktsegment weiter zu bedienen. So verdienen die Hersteller mit den konventionell angetriebenen Fahrzeugen weiterhin Geld und sind somit in der Lage, die Investitionen in Entwicklung und Produktion von batterieelektrischen Fahrzeugen zu finanzieren.
Andere OEMs rüsten bestehende Werke so um, dass dort nur noch E-Autos gebaut werden können und die Produktion von Verbrennern an diesen Standorten eingestellt wird. Dieses Vorgehen ist nicht ohne Risiko, denn das bisherigen Kaufverhalten zeigt, dass die Zulassungszahlen von E-Autos volatiler zu sein scheinen und dass der Verbrenner nach wie vor nachgefragt wird. Je nach Marktsegment und Markt ist der Verbrenner weiterhin die präferierte Antriebsart für viele Kund_innen. Deshalb geht der Trend zur Entwicklung von Universalplattformen, bei denen die Fahrzeugarchitektur sowohl einen konventionellen als auch einen alternativen Antrieb abbilden kann. Dieser Ansatz erfordert allerdings Kompromisse, da die unterschiedlichen Antriebsarten mit ihren spezifischen Anforderungen ein unterschiedliches Packaging erfordern. Außerdem sind tiefgreifende Veränderungen und Anpassungen in den Prozessen, Produktionsanlagen und Lieferketten notwendig, um eine Integration in die vorhandene Fertigung und damit flexible Produktion sicherstellen zu können.
AUFTRAGSFERTIGER ALS PROBLEMLÖSER
Den Ausweg kann dem OEM hier ein externer Produktionspartner bieten. Auftragsfertiger sind durch ihre hohe Flexibilität in der Lage, auch kleinere Stückzahl effizient und in hoher Qualität zu produzieren. So hat Magna jahrzehntelange Erfahrung darin, unterschiedliche Fahrzeuge auf einer Linie zu produzieren. Damit können verschiedene Programme mit kleineren Stückzahlen eine Linie auslasten und damit wirtschaftlicher hergestellt werden. Bis zu einem gewissen Grad ist es dabei auch möglich, die Produktionskapazität zwischen den unterschiedlichen Produkten auszubalancieren, um die Produktionslinie auch im Falle einer nicht erfüllten Stückzahlerwartung bestmöglich auszulasten.
Für einen Multi-OEM-Fertiger wie Magna ist die Fähigkeit dieses ständigen Ausbalancierens Teil des Geschäftserfolgs. Sinkende und schwankende Volumina können bei einem OEM schnell zu Kapazitätsunterauslastungen führen und die Fertigung von Modellen ineffizient und kostenintensiv machen. Auch die Strategie einiger OEMs, Modelle mit einem geringen Deckungsbeitrag aus dem Programm zu nehmen, führt zu geringerer Auslastung der Werke. Deshalb kann es für einen OEM auch sinnvoll sein, beispielsweise die Auslauffertigung eines nach wie vor profitablen Modells nach außen zu geben. Ebenso interessant kann die Auslagerung der Fertigung sein, wenn der OEM etwa die Akzeptanz für Fahrzeugkonzepte oder -segmente testen will, ohne dafür eigene Kapazitäten bereitstellen zu müssen.
FLEXIBLE PRODUKTION ALS IDEALE VORAUSSETZUNGEN FÜR NEW ENTRANTS
Für Neueinsteiger in der Branche ist die Produktion bei einem externen Partner besonders interessant. Mit einem Auftragsfertiger erhält das Unternehmen Zugang zu einer bereits eingerichteten Produktionsstätte, inklusive der Belegschaft, mit eingespielten Prozessen und bestehender Supply Chain. Für ein größeres Projekt übernimmt ein in der flexiblen Automobilproduktion erfahrener Fertigungspartner auch die komplette Industrialisierung: Planung und Aufbau der Fabrik, die Etablierung der Prozesse, den Aufbau der Infrastruktur und die Festlegung passender Qualitätsstandards. Dadurch hat der Neueinsteiger nicht nur weniger Risiko in Bereichen, in denen er selbst noch wenig Erfahrung hat; sondern er kann auch schneller auf dem Markt sein. Und er kann sich auf Kernaufgaben wie Markenbildung, Werbung, den Aufbau von Vertrieb und Servicenetz und nicht zuletzt die Akquisition von Investoren fokussieren. Somit fallen einige Risikofaktoren weg, die immer wieder zum Scheitern von Startups im Automotive-Bereich führen.
MAGNAS „FLEXIBLE MANUFACTURING SOLUTIONS“-INITIATIVE
Um die Fertigung im Magna-Werk in Graz noch flexibler und zukunftsfähiger zu gestalten, wurde eine Transformation unter dem Namen "Flexible Manufacturing Solutions" eingeleitet. Ziel ist es, bis zu vier Plattformen und acht Derivate unabhängig von Antriebsart und Stückzahlschwankungen auf einer Linie zu produzieren. Dabei strebt Magna an, der schnellste und effizienteste Partner für Programme mit mittleren (15.000 - 50.000 Fahrzeuge pro Jahr) und niedrigen Stückzahlen (< 15.000 Fahrzeuge pro Jahr) in Europa zu sein.
MEHR PLATTFORMVARIANTEN PRO LINIE IM KAROSSERIEBAU MÖGLICH
Mit einer Reihe von Maßnahmen wird die Flexibilität im Karosseriebau noch weiter erhöht. Durch die Integration flexibler Fügestationen können mehrere Modelle auf einer gemeinsamen Linie gefertigt werden, ohne für jedes Modell einen eigenen Karosseriebau aufbauen zu müssen. Ein erster Schritt in der Flexibilisierung des Karosseriebaus war die Einführung des "Modular Flex Framing". Das System ermöglicht es künftig, bis zu sechs verschiedene Karosserievarianten in einer einzigen Station zu rahmen.
Herzstück ist ein flexibler Framer, der in rotierenden Speichern bis zu drei modellspezifische Adapter hält und diese passend für das jeweils nächste Fahrzeug in der Linie in Position bringt. Fährt zum Beispiel ein Sedan in die Linie, werden automatisch die entsprechenden Adapter eingesetzt, um den Sedan zu fertigen. Folgt darauf etwa ein SUV, werden die Adapter wieder automatisch getauscht und das SUV gefertigt.
Zusätzlich wird in Zukunft ein geometriebildender „Modular Flex Geoskid“ zum Einsatz kommen, der einen vollautomatisierten Austausch der geometriebildenden Vorrichtungen ermöglicht. Anstelle modellspezifischer Transportschlitten werden flexible Systeme eingesetzt. Ein universeller Rahmen wird automatisiert mit spezifischen Adaptern bestückt und ermöglicht so einen schnellen Wechsel zwischen verschiedenen Modellen. Zusammen erhöhen diese Maßnahme die Anzahl von Karosserievarianten pro Linie von zwei auf bis fünf – bei Erweiterung sogar zu sechs
INNOVATIONALS SCHLÜSSEL
Innovative Lösungen stellen dabei konstante Produktqualität sicher. Ein Beispiel hierfür ist die „Automated Body-in-White Fixture Control“. Die geometriebildenden Transportschlitten sind eines der wichtigsten Elemente beim Aufbau der Geometrie der gesamten Rohkarosserie. Geometrische Abweichungen führen dazu, dass auch die produzierten Rohkarosserien von den Maßen abweichen, was sogar den weiteren Montageprozess des Gesamtfahrzeugs behindern kann. Um dies zu verhindern, müssen die Transportschlitten periodisch überprüft werden – allerdings sind diese während des laufenden Betriebs nicht zugänglich und müssen somit außerhalb der Linie überprüft werden.
Anstatt dieser sehr aufwendigen periodischen Überprüfung vermisst Magna nun jede Fahrzeugkarosserie in einer eigenen Messstation. Mit einem smarten Algorithmus wird aus den Messdaten extrapoliert, ob die Transportschlitten innerhalb der Toleranzen sind. Diese deutlich engmaschigere Prüfung sorgt dafür, dass Abweichungen vorrausschauend erkannt und abgestellt werden. Nacharbeit an Karosserien, die diese Toleranzen nicht einhalten, wird somit stark reduziert.
FLEXIBLE PRODUKTIONSMÖGLICHKEITEN IN DER LACKIEREREI
Schon seit Jahren lackiert Magna alle Fahrzeuge, die am Standort Graz vom Band laufen, in einer gemeinsamen Anlage, unabhängig vom Hersteller oder der genauen Plattform. Dabei ist ein hoher Grad an Individualisierung möglich – von maßgeschneiderten Lackdesigns über besondere Lackeffekte (z.B. Perleffekt, Klarlack, Mattlack), kontrastierende Farben für Dächer und Türen bis hin zu Sonderfarben. Auch Niedertemperaturlackierung, z.B. für besondere Effektlackierungen oder das Lackieren von Anbauteilen, etwa für Sonderserien, ist möglich. An Stückzahlen deckt die Lackiererei alles von Einzelstücken (auch als Losgröße 1 bezeichnet) bis zur Großserie alles ab, und das unter Einhaltung sämtlicher Qualitätsstandards der jeweiligen Automobilhersteller.
OPTIMIERUNG DER LOGISTIK DURCH NÄHE ZUR MONTAGELINIE
Die Logistik rückt im Grazer Magna-Werk näher an die Montagelinie, um die steigende Modell- und Teilevielfalt optimal handzuhaben. Heutige Industriestandard-Lösungen sind oft nicht effizient genug und benötigen zu viel Platz. Das neu konzipierte automatisierte Lager- und Bereitstellungssystem bei Magna in Graz zur Sequenzierung stellt den Mitarbeiter_innen die Teile in der richtigen Reihenfolge und mit den richtigen Ausstattungsvarianten nahe am Band zur Verfügung. Es reduziert einerseits Gehwege für die Logistiker_innen und andererseits den Platzbedarf für die Sequenzierung. Diese Maßnahmen ermöglicht es, dass bisher externe Sequenzierumfänge nun bandnah auf dem Werksgelände sequenziert werden, wodurch sowohl die Transportbedarfe reduziert als auch die Kosten pro Fahrzeug gesenkt werden.
Die reduzierten internen Transporte unterstützen auch die Nachhaltigkeit am Standort Graz. Das Werk ist bereits seit 2022 CO2-neutral, die verbesserte Logistik trägt zu einer weiteren Verringerung der Emissionen bei.
PRODUKTFLEXIBILITÄT AUF MONTAGELINIE WIRD ERHÖHT
In der Montage ermöglichen flexible Fördertechnik, eine flexible Hochzeitsstation und erweiterte Testkapazitäten die Fertigung von bis zu vier statt bisher zwei Plattformen auf einer Montagelinie. Durch den Einsatz von austauschbaren, produktspezifischen Adaptern werden Unterschiede in den Antriebsarten, Plattformabmessungen und Aufbauformen berücksichtigt. Die erhöhte Tragkraft der Transportgehänge ermöglicht künftig auch die Fertigung von größeren und schwereren Fahrzeugen und trägt dem steigenden Anteil an Elektrofahrzeugen Rechnung. Die zusätzlichen Prüfstände am Ende der Linie stellen sicher, dass die erweiterten Fahrzeugfunktionen auf ihre Zuverlässigkeit abgesichert werden können.
Durch die Erhöhung der Flexibilisierung in den verschiedenen Bereichen der Produktion ist Magna in Graz weiterhin der ideale Partner für traditionelle und neue Automobilhersteller. Kund_innen profitieren dabei von langjähriger Erfahrung und verkürzten Integrationszeiten.
Stay connected with Inside Automotive!
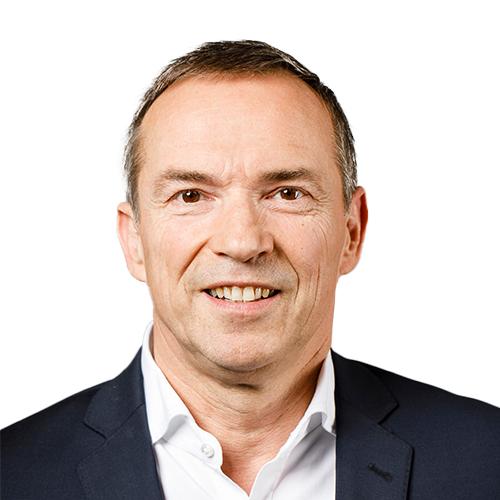
Erwin Fandl
Erwin Fandl ist seit 2019 Vice President Manufacturing bei Magna Steyr. Nach seinem Eintritt bei Magna im Jahr 1992 war er in verschiedenen leitenden Positionen in der Gesamtfahrzeugfertigung und im Qualitätsmanagement tätig. Er hat einen Abschluss als Diplom-Ingenieur an der Universität Graz.
We want to hear from you
Send us your questions, thoughts and inquiries or engage in the conversation on social media.
Verwandte Stories
Verbunden bleiben
Bleiben Sie informiert und erhalten Sie News & Stories in Echtzeit in Ihren Posteingang geliefert.