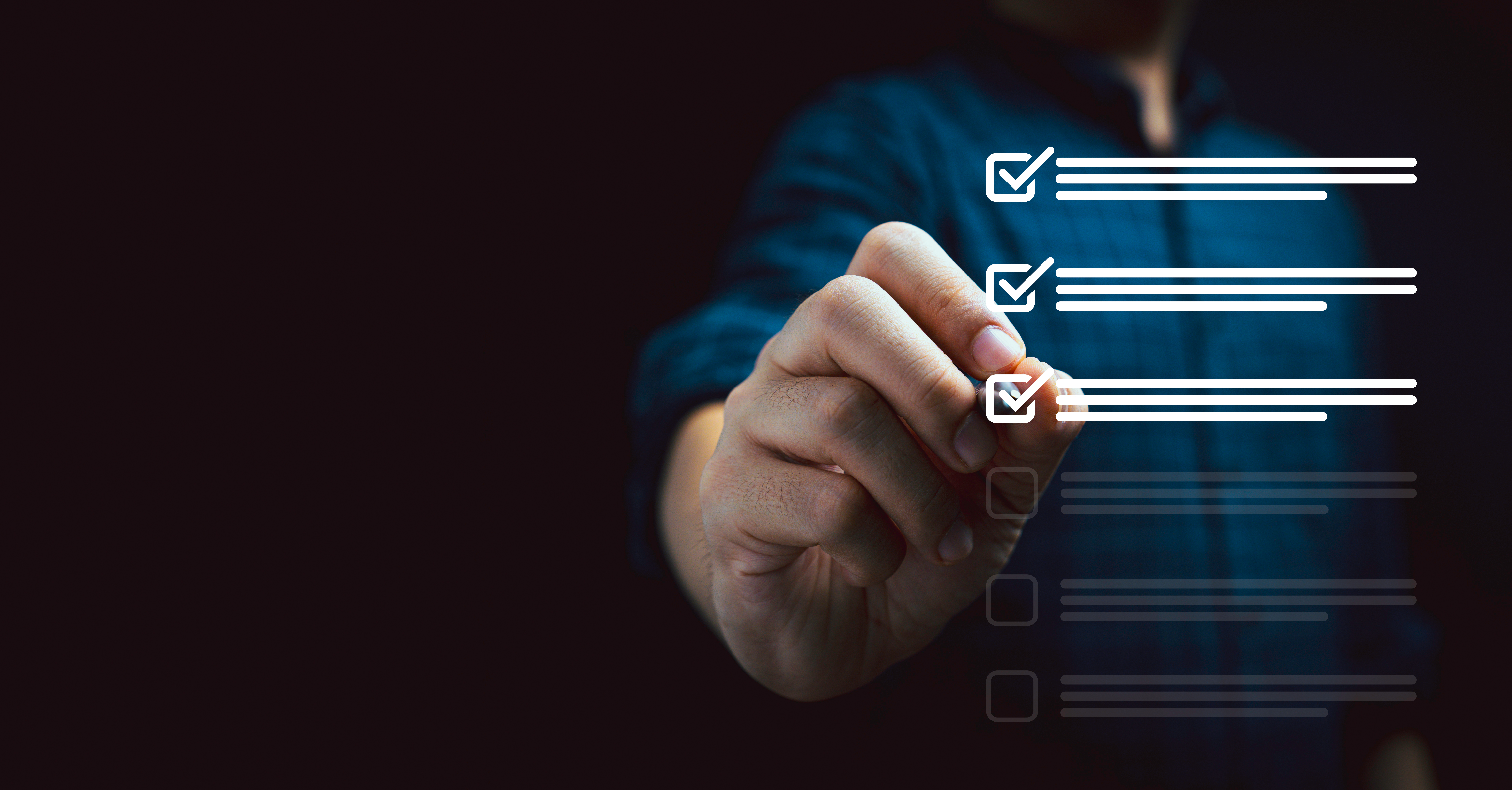
NO CERTIFICATION WITHOUT QUALITY MANAGEMENT, NO ORDER WITHOUT CERTIFICATION
A certified quality management system is a prerequisite for a service provider or supplier to operate in the automotive industry. For this purpose, the IATF (International Automotive Task Force) has developed uniform requirements for quality management systems, which all relevant companies are obliged to comply with.
The IATF is an international working group consisting of representatives from leading automotive manufacturers in Europe, North America and China. A respective company is only certified in accordance with IATF 16949 when it can demonstrate a comprehensive quality management system that covers all business processes. Without a comprehensive quality management system and without IATF 16949 certification, a company is virtually ineligible as a supplier for vehicle manufacturers.
For quality assurance in general, the primary goal is to always ensure customer satisfaction. For the contract manufacturer, this means not only complying with the quality criteria specified by the client in the actual production process but also building a product that satisfies the end customer in terms of quality. Therefore, the contract manufacturer must meet the same requirements as the vehicle manufacturer itself, and quality assurance begins as early as the concept phase of a production order.
QUALITY MANAGEMENT AFFECTS ALL AREAS WITHIN THE COMPANY
All corporate areas are mapped in the quality management system because all of them play an important role when it comes to a product as complex as a complete vehicle. Precise process descriptions are crucial in the project phase to be successful right from the start.
Customer requirements are determined using data such as market analyses to develop product-dependent processes. A standardization of these processes is pursued, which has the advantage of being able to refer to existing experience. Hence, an experienced contract manufacturer offers a competitive benefit because they can assess in advance which potential difficulties could arise. The aim is to identify potential risks at an early stage and prevent them from occurring to achieve and ensure maximum customer satisfaction.
This process begins during development and continues throughout setup and ongoing serial production. It is constantly evaluated and further developed. Quality management also has tasks to perform in the aftersales area even after production has been discontinued, for example in the field of spare parts supply. As a result, more than just customer satisfaction is ensured. It also generates valuable feedback information, and the experience gained is then used in future programs.
ESTABLISHING APPLICABLE QUALITY STANDARDS IN CLOSE COOPERATION WITH CUSTOMERS
At the start of any program, the relevant quality assurance standards and criteria are defined in close cooperation with the vehicle manufacturer. A multi-OEM manufacturer like Magna benefits greatly from working with not just one, but many different vehicle manufacturers. This allows the best of all worlds to be brought together and transferred to the company's own internal standards. Their application is then arranged with the customer wherever possible so they can be implemented for the respective project in a very short time.
Of course, if the vehicle manufacturer insists that the project is only carried out exactly according to its own specifications, this can be realized. That is why it is necessary to involve quality management at a very early stage because these agreements have an impact on the corresponding processes, the required effort and the respective offer to the vehicle manufacturer or the model of collaboration.
By the time serial production starts, all alignments have been completed in detail. Nevertheless, customers can always request modifications which can then lead to process updates as part of change management.
CONTINUOUS QUALITY PERFORMANCE MEASUREMENTS AS PREREQUISITE FOR CONSISTENTLY HIGH QUALITY
The internal key performance indicator system enables monitoring where the respective key performance indicators (KPIs) currently lie for each area at any time. If one of these indicators reaches a critical level, meaning that there is a risk of limit violations, countermeasures will be taken immediately. The quality assurance methods are then based on the respective production process.
For example, the dimensional accuracy of the vehicle body is partly monitored 100 percent inline in automated measuring stations during the production process. In addition, comprehensive random sample inspections are carried out on individual vehicle bodies, which are taken from ongoing production and transferred to the measuring facility. This allows the key figures for individual features as well as for the dimensional accuracy of the entire vehicle body to be condensed into a comprehensive overview.
It is crucial not to intervene only when a key figure becomes “out of control,” but to recognize trends and initiate countermeasures before the product is negatively affected.
PREVENTION IS BETTER THAN CORRECTION: WHY FMEA IS A MUST
Prevention is a central element of quality management in more than just the automotive industry. It begins as early as the product and process development stage with an appropriate risk assessment. The aim is to minimize the likelihood of deviations from specification and, where possible, to rule them out, for example through robust processes, appropriate design and suitable equipment.
The FMEA (Failure Mode and Effects Analysis) and, in production, the process FMEA are used for this purpose. A structured risk assessment is conducted to determine and evaluate the potential for process faults and to take appropriate measures to minimize the risk. This ensures that errors do not occur in the first place.
As a complete vehicle solutions provider combining development and manufacturing under one roof, Magna has the advantage of short distances and therefore, fast feedback loops. For example, the aspects of easy manufacturability are already incorporated into the product development, which leads to risk-optimized manufacturing processes. The keywords here are design for manufacturing and design for assembly.
PRODUCING QUALITY, NOT TESTING IT: THE IMPORTANCE OF EDUCATION AND TRAINING
Well-educated and trained employees are not only more motivated, but they are also able to achieve better quality. At Magna, there are two sides to this: First, the ratio of skilled workers in production is high. Second, training each individual employee in their work steps is a major concern.
The so-called specification documents are based on the work instructions and training documents specific to the current workplace. Training employees not only keeps the job interesting for them, but also develops an understanding of what is being assembled and what function their own work fulfills.
Well-trained employees are of great importance to minimize the risk of errors right from the beginning of the project. This also includes the immediate reporting of any faults that are observed during assembly. This allows investigations to be carried out quickly at the relevant inspection stations or at least initiated. For example, if a faulty supplier part is detected, the next logical step is to immediately check all similar parts on the line before they are installed into the vehicle. For this, standardized processes that can be activated immediately must be in place.
AUTOMOTIVE INDUSTRY: CHANGING QUALITY EXPECTATIONS OF END CUSTOMERS
There is no doubt that the quality assessment of end customers is shifting. It is particularly noticeable that the success of some manufacturers' products appears to be unaffected if classic criteria such as a part’s accuracy of fit or narrow and precise gap dimensions are given slightly larger tolerances. However, some vehicle manufacturers and their end customers continue to demand “craftsmanship” and therefore no negligence on the part of the contract manufacturer is tolerated in this respect.
Also, the introduction of new systems, particularly in ADAS and connectivity, comes with additional qualitative requirements in terms of functionality, stability and safety.
THE IMPORTANCE OF PRODUCT QUALITY FOR MARKET SUCCESS
Even if end customer expectations are at least in part changing – product quality is still of central importance for the success of a vehicle. Even if the end customer cannot judge everything for themselves, the perceived quality is important for classifying the vehicle in the market.
For example, perceived quality is assessed and reported by journalists in corresponding test reports in specialized and general press and influences the assessment of other product features. There are also other assessment tools like breakdown statistics and studies by institutes such as JD Power, which assess the quality of the end product.
Naturally, it is also important for the contract manufacturer that the vehicle is well received in the automotive industry market. Although the contract manufacturer cannot influence every aspect of the vehicle's acceptance, it can at least ensure that it makes the best possible contribution to customer satisfaction. In this way, the production plant not only secures its position in relation to other contract manufacturers, but also in relation to the vehicle manufacturer's own plants.
DIGITALIZATION AND SOFTWARE-DEFINED VEHICLES: THE BIGGEST CHALLENGES FOR QUALITY MANAGEMENT
The increasing complexity of systems whose overall quality and error-free functioning cannot be comprehensively tested during the production process ultimately reduces the scope for quality management in production.
To ensure that only vehicles that are flawless in all respects (especially regarding the functionality of the software-controlled systems) pass through quality assurance and leave the factory, both the vehicle manufacturer and the contract manufacturer are dependent on reliable work during product development and flawless supplier components.
This is where analysis is particularly challenging: It is typical for software-related malfunctions to only occur randomly in certain constellations and special situations – and therefore very sporadically. As part of the final inspection, it is not possible to test all possible situations to ensure that everything is completely fault-free.
Great importance is placed on ensuring supplier quality to filter out potential error sources at an early stage. Here, very meticulous work is required to detect and avoid potential errors.
FUTURE TRENDS IN QUALITY ASSURANCE
Ultimately, the test procedures and methods must be adapted for each new vehicle type that goes into production. Even if the basic test steps are already known, applications must be developed specifically in each case, if necessary, together with the vehicle manufacturer and the suppliers of the parts or systems.
With new systems in vehicles, the amount of data that the contract manufacturer has to process is on the rise. It is becoming increasingly important to extract information from this data and to read and interpret it in such a way that it allows conclusions about the functionality of the vehicle. This particular aspect will continue to gain importance in the future. Support from external partners and research institutes helps not only to keep up with the times, but also to actively shape the future. However, traditional quality assurance in the automotive industry must and will always stay relevant.
Stay connected with Inside Automotive!
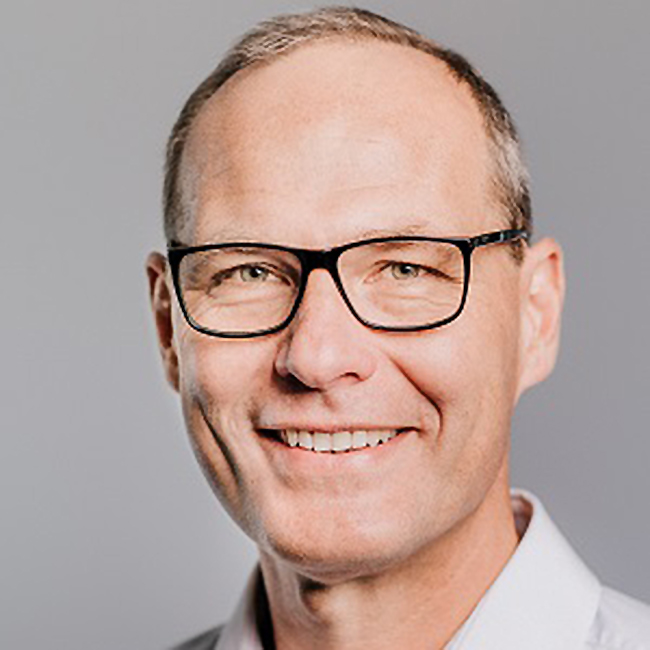
We want to hear from you
Send us your questions, thoughts and inquiries or engage in the conversation on social media.
Related Stories
Stay connected
You can stay connected with Magna News and Stories through email alerts sent to your inbox in real time.