Welding Technologies
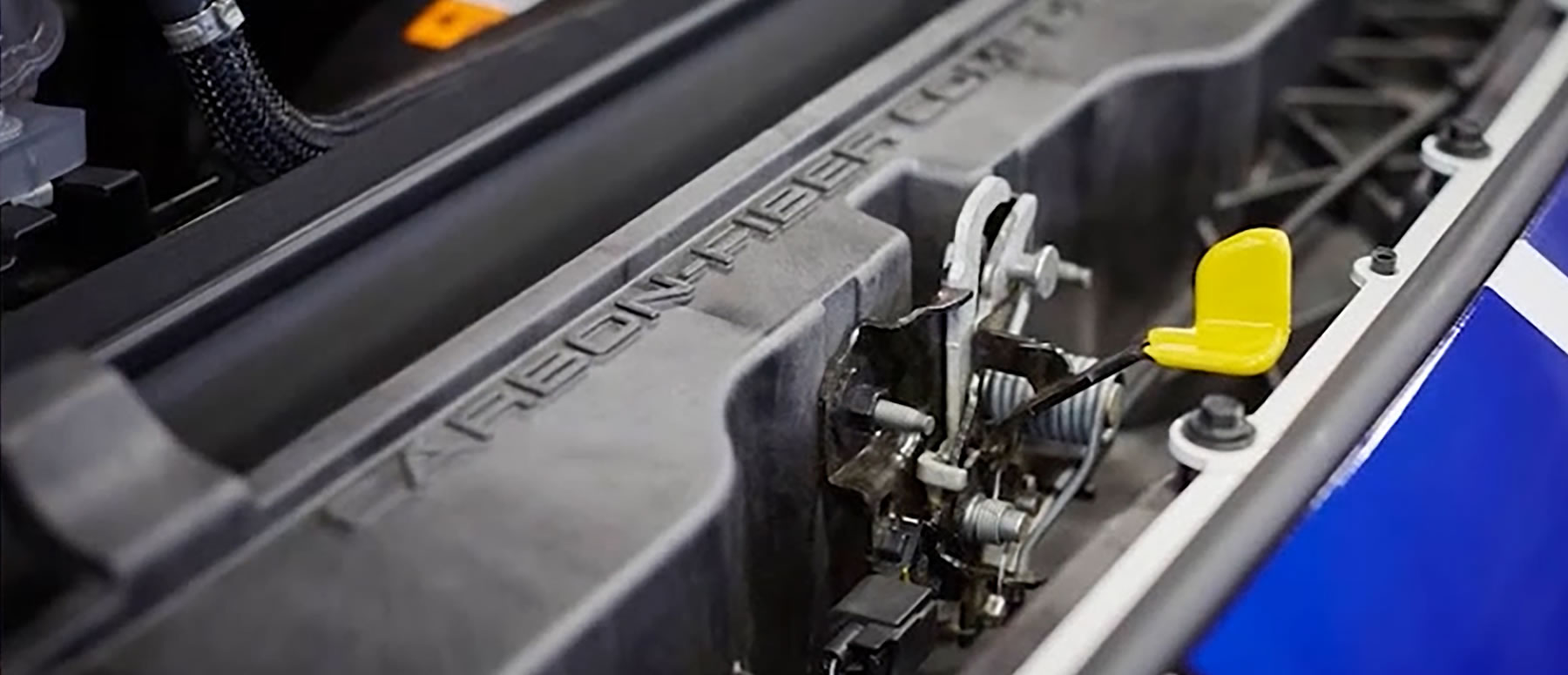
Process Innovation
At Magna, we use the latest in welding technologies to help our customers save costs, improve quality and light weight their vehicles.
Resistive Impact Welding
Cost Effective Welding Without Adhesives
The joining together of two or more plastic components to form a weld or joint is frequently required during the manufacture of automobile components. As the use of plastic material in automotive applications increases there exists a greater need for more ways of welding together such components. Resistive Implant Welding may be used to join materials using electrical current to create a box section construction. It is a cost effective and quick method of joining or welding low energy substrates without adhesives.
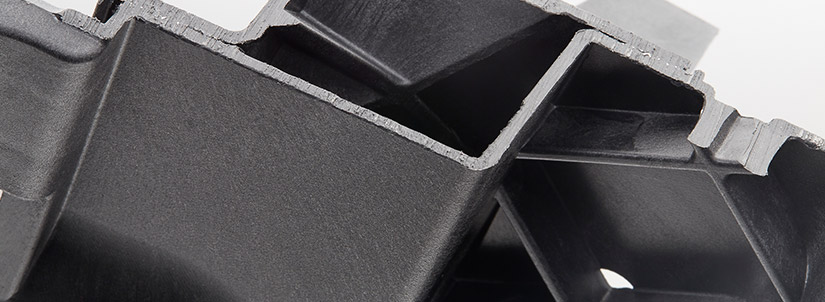
Process Efficiency
Resistive Implant Welding is a simple technique which can be applied to almost any thermoplastic. Weld times can be relatively short, typically under 60 seconds for most applications, resulting in greater process efficiency.
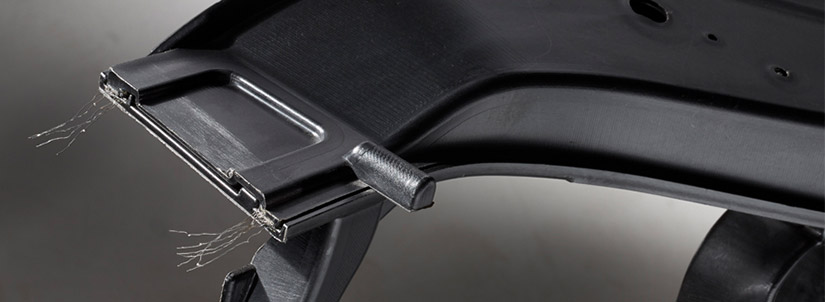
Cost Effective
The elimination of stamping, tooling and assembly equipment results in cost savings for the customer.
Torsional Ultrasonic Welding
Precision Joining for Automotive Fascia
Torsional Welding joins thermoplastic olefins (TPOs) in the manufacture of automotive fascia. A machine oscillates at a high frequency, creating friction that results in two TPO components, such as a fascia and a bracket, melting together precisely. Magna is the first to use torsional welding to join TPOs in the manufacture of automotive fascia.

Weight Reduction
The Torsional Welding process works well on thin-wall materials and no thickening is needed. With this process, Magna can achieve about 10 percent in mass reduction compared to a traditional wall stock. Because of this, Torsional Welding can help OEMs with lightweighting efforts, a priority as they work to meet increasingly stringent global emissions standards.
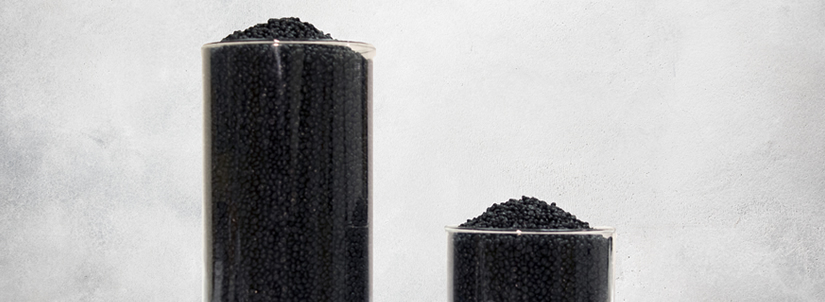
Material Reduction
Weight savings from the Torsional Welding process translate into cost savings thanks to reduced material costs.
Laser Cutting & Welding
Creating Value with Process Improvements
Magna’s Laser Cutting and Welding process provides greater flexibility when making lower-volume parts and enables weight savings by using a thinner-walled component. It also removes the need for traditional punch/weld machines, which saves on investment and floor space.
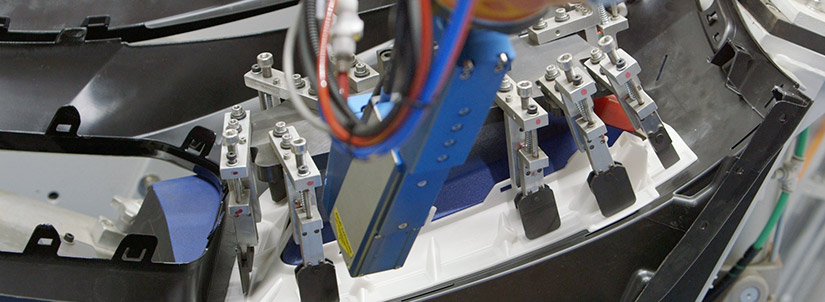
Flexible Manufacturing Capability
Laser Cutting and Welding can provide flexible manufacturing capability where secondary operations are required. Laser equipment can support several lower-volume programs, replacing multiple dedicated punch and weld cells.
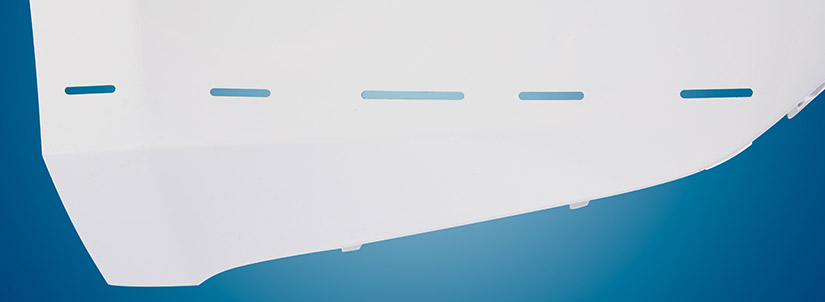
Laser Cutting
Through advanced laser cutting technology, flexibility increases through the cell by not limiting punch/die sizes. Laser cutting creates the ability to change hole sizes on the fly with simple programming changes rather than having a whole separate machine to do another size hole.
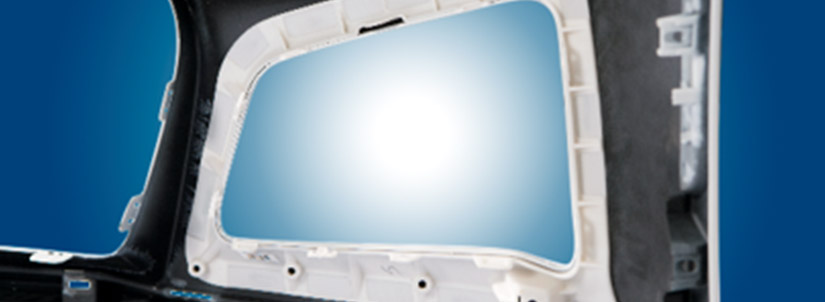
Laser Welding
Advanced laser welding technology is able to weld thinner wallstock without read through, which creates a mass saving on total assembly. It allows manufacturers to use less weld area and achieve higher pull off forces. This reduces bracket footprints causing a better packaging ability because smaller flanging is needed for laser welding.