"All vehicles can benefit from active aerodynamics"
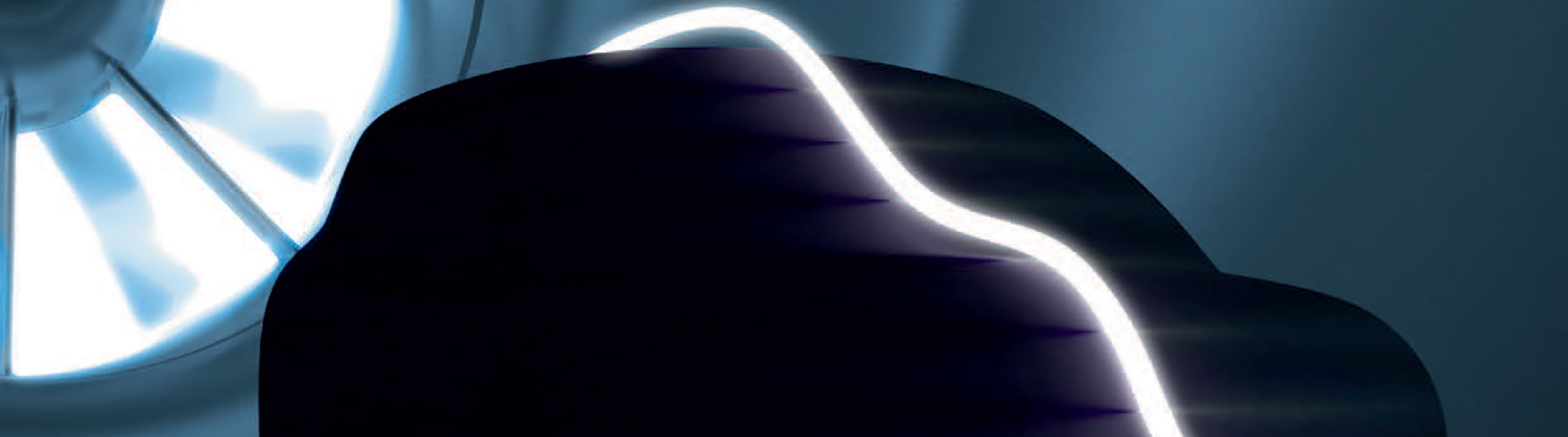
Interview with Braendon Lindberg
Featured in ATZ Automotive
Interviewed by: Frank Jung
To improve the aerodynamic profile, Magna has developed systems that are electronically linked to the vehicle and receive information about when and how they need to move. Braendon Lindberg, Technical Manager of the Global Active Aerodynamics Product Line at Magna Exteriors, explains how they work and their advantages.
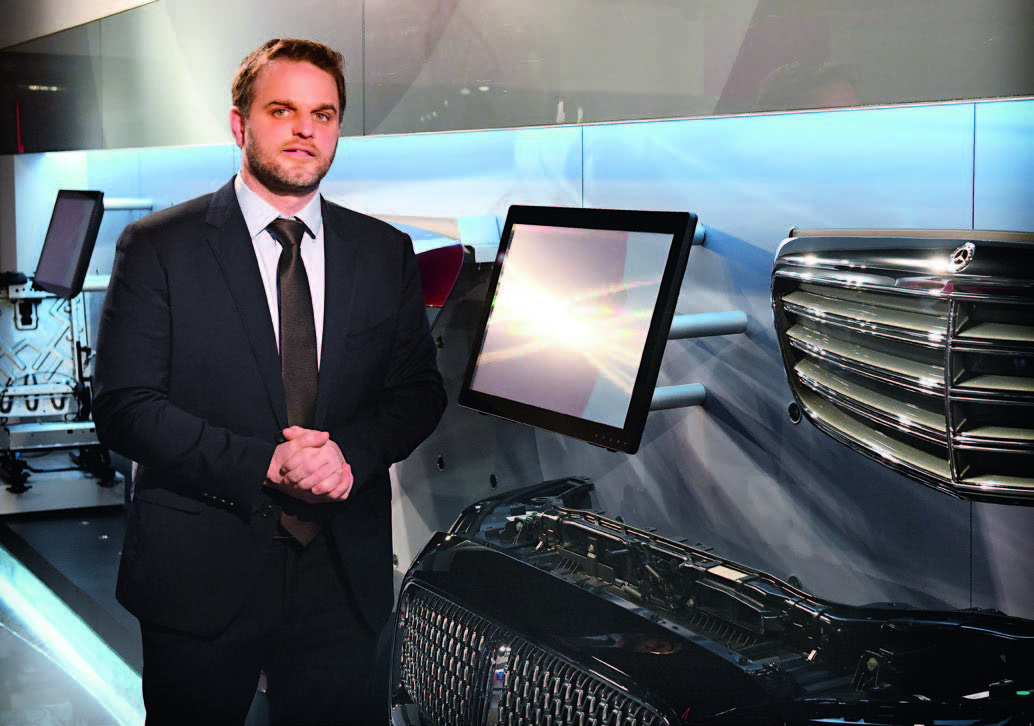
ATZ _ Braendon Lindberg, please take us on a short journey through time: Magna and aerodynamics – what key data, milestones and achievements have there been in the past?
LINDBERG _ Magna has been developing active aerodynamic systems since 2010. Our first Active Grille Shutter (AGS) system went into production in early 2012 on the Dodge Dart. We introduced our first Visible Active Grille Shutter (V-AGS) on the Mercedes-Benz E-Class in 2015. Since then, we have grown to all regions of the world and produce more than three million systems per year. In January of 2018, we launched a first-to-market, high-volume Active Air Deflector on the RAM 1500. Now, Magna has an entire suite of products that is currently in the pipeline for all vehicle types. To date, Magna products on the road have saved millions of metric t of CO2. We are committed to making an environ-mental impact, and active aerodynamics help our customers reduce their carbon footprint.
"Aerodynamics are complicated, and we use every tool at out disposal"
How does the aerodynamics of an electric car differ from that of a car with a combustion engine?
Fundamentally, aerodynamics are the same on any vehicle, regardless of pro-pulsion type. However, aerodynamics on electric vehicles demand increased focus. Drag on the vehicle moving down the road is one of the largest contributors to energy consumption. If we can save battery energy by making a vehicle travel down the road more efficiently, that energy can be used later to increase vehicle range. There is a slightly different approach to identifying products that work best for each vehicle type. For example, an electric vehicle with an inherently flat underbody might not need an Active Air Deflector, but a high-riding internal combustion vehicle would. On the other hand, an SUV with wide tires would see a substantial benefit from Active Front Wheel Deflectors. Each application can have an aero package that is optimized for that vehicle’s shape.
SUVs have been in vogue for years which stand in the way of streamline styling rather than being beneficial. Which auxiliary systems can be used to improve the drag coefficient? Does this also apply to panel/ box-type vans?
We like to ask, “Why compromise?” A major benefit of an active system is that the styling of the vehicle, and often the capability, can be decoupled from the aerodynamic profile if you are able to change the shape of the vehicle as it travels down the road. That is exactly what we do with our active aerodynamic systems. A vehicle can still have the styling cues when the car is stationary, like you mention, but shift to a more aerodynamic profile at certain driving conditions. All vehicles can benefit from active aerodynamics.
If you had to assess your work: How many percent improvement comes from the CFD analysis and how much from the real test in the wind tunnel?
Aerodynamics are complicated, and we use every tool at our disposal. Having said that, nothing compares to real-world testing. CFD is often simulated at the beginning of the product development process to indicate directional benefits. Because of our experience in developing active aerodynamic products, we lever-age this knowledge when planning our testing. Magna has a very effective approach to evaluating our systems in the wind tunnel, and we use that time to optimize our products.
This is valid today. What about in five and in 15 years from now?
As simulation programs become less resource-intensive and their accuracy increases, we will rely on them more heavily. However, we don’t see a large change in how we develop our products. We see the need for active systems increasing to meet future emissions requirements.
Wind around the body also creates noise. How important is NVH in your developments? How can it be determined?
Although wind noise is a very important topic, our focus is on reducing vehicle emissions, extending range, and saving fuel. Typically, during development, any type of NVH feature, like whistling, would be analyzed and addressed. We can then potentially reduce NVH by streamlining the airflow.
Without any doubt the keyword for your latest developments is “active.” What is the difference to previously installed systems?
The main difference is that we can change the exterior shape of the vehicle. We do this by making surfaces move to optimize the aerodynamic pro-file. This typically means there is a smart actuator connected to the sur-face. These actuators interface with the vehicle and receive information on when and how to move to optimize the aerodynamic profile. Since our products are active, we can occupy certain spaces at specified conditions. For example, our Active Air Deflector can deploy at higher speeds closer to the road, which is not possible for fixed devices due to curb height and ramp angle requirements.
"The need for active systems is increasing to meet future emission requirements"
Let’s start with the active closing system for the grille. How does it work and how can the necessary balancing act between thermal management and aerodynamics succeed?
An Active Grille Shutter works by opening and closing depending on the vehicle’s needs. When open, air-flow is directed through the grille opening to provide cooling. When the vehicle does not need cooling, the grille shutter will close and optimize the airflow around the vehicle. Having an active system allows for a balance of both thermal and aerodynamics requirements.
What about the Active Air Deflector and the underbody panel? Are these components a result of the increasing success of SUVs?
The Active Underbody Panel is geared towards lower-riding passenger cars because of how it directs the airflow. For SUVs and higher-riding vans, products like our Active Front Wheel Deflectors are popular for managing front air-flow, while Active Rear Diffusors and Active Spoilers help shape airflow on the rear of the vehicle.
Please explain to us how the Active Front Wheel Deflector and the rear diffuser work?
Both products work to achieve the same goal by providing the vehicle an aero-dynamic benefit. Where the two products differ is their location on the vehicle. The Active Front Wheel Deflectors help shape the airflow around the front tires. The Active Rear Diffusor takes the air-flow from under the vehicle and redirects it to optimize the flow directly behind the rear of the vehicle. As you can imagine, there is a lot of potential aerodynamic benefit in the SUV segment.
And the active rear spoiler? Will this be used exclusively in sports cars?
The Active Spoiler is best applied to sedans as a decklid spoiler and SUVs as a liftgate spoiler. Active Spoilers on sports cars are typically decklid spoilers that aim to improve handling performance, meaning they are focused on changing the downforce or lift of the vehicle. The Active Spoilers we develop focus on reducing the coefficient of drag, which results in improved fuel consumption and reduced emissions. For electric vehicles, the focus is to extend range.
What fuel and CO2 savings can be achieved by all of these components individually?
Individually, depending on the device and vehicle, fuel savings of 0.06 to 0.37 l/100 km can be achieved. If products are combined, the savings could be compounded.
Are they also worthwhile on the bottom line, so is the use of the components still in reasonable proportion to the additional material required and thus weight? Does the topic of sustainability by the spare of resource consumption play a role here too?
This is a question we get a lot and the answer is actually very surprising. In order to achieve the same fuel savings that many of our active systems can deliver, you would need to reduce the mass by up to 50 kg on certain vehicles, and by comparison, our systems don’t weigh nearly that much.
Braendon Lindberg, thank you for this interesting interview.
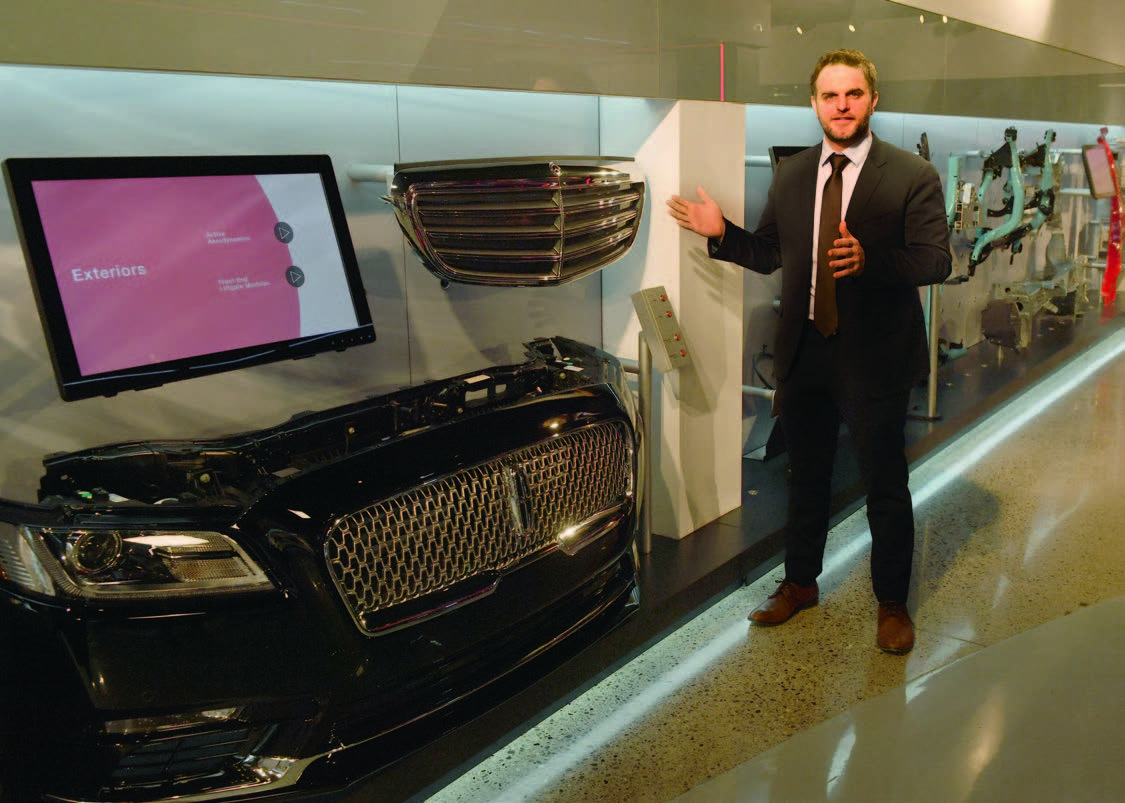
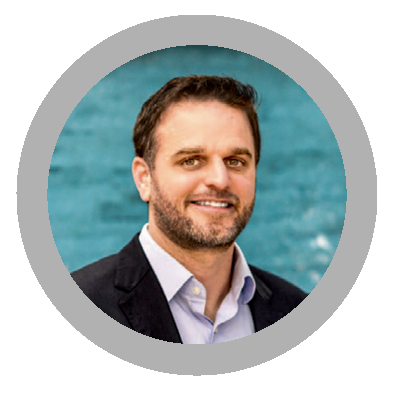
Braendon Lindberg
Braendon Lindberg (born in 1983) is Global Product Line Technical Manager of Active Aerodynamics at Magna Exteriors in Troy, Michigan (USA). He is responsible for the development of aerodynamic technology and innovations in support of Magna customers worldwide since January 2018. He graduated from Penn State University Behrend in Erie, Pennsylvania (USA) in 2011 with a degree in mechanical engineering. Lindberg has nine years of management and automotive experience in product development, process engineering, electro-mechanical actuation, plastic injection processing, as well as in powertrain and exterior development. He has lived and worked globally, having spent most of this time in the USA and Germany.