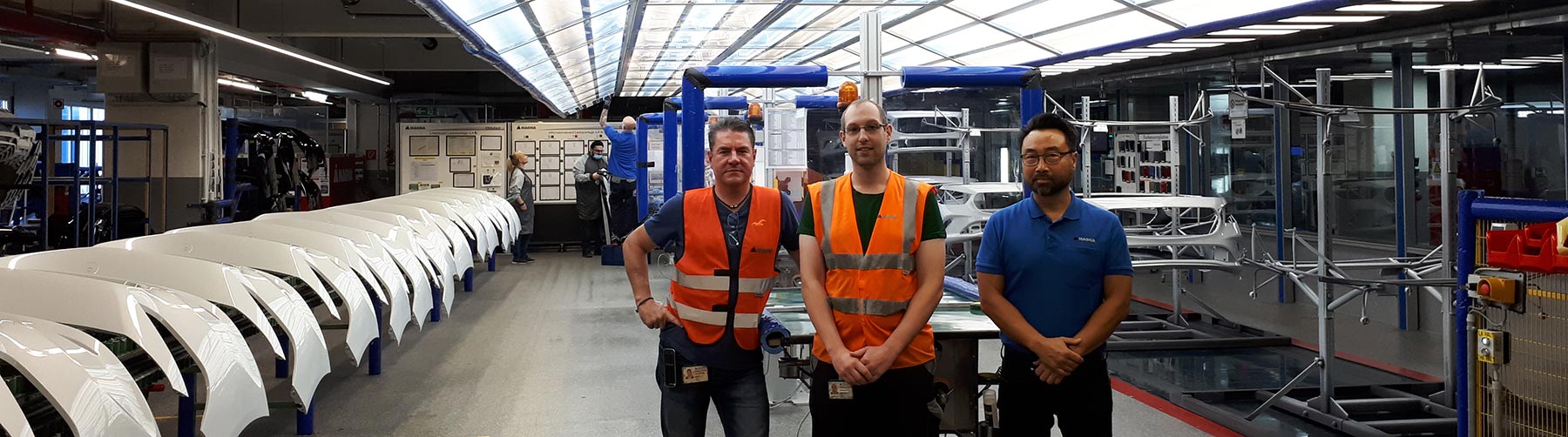
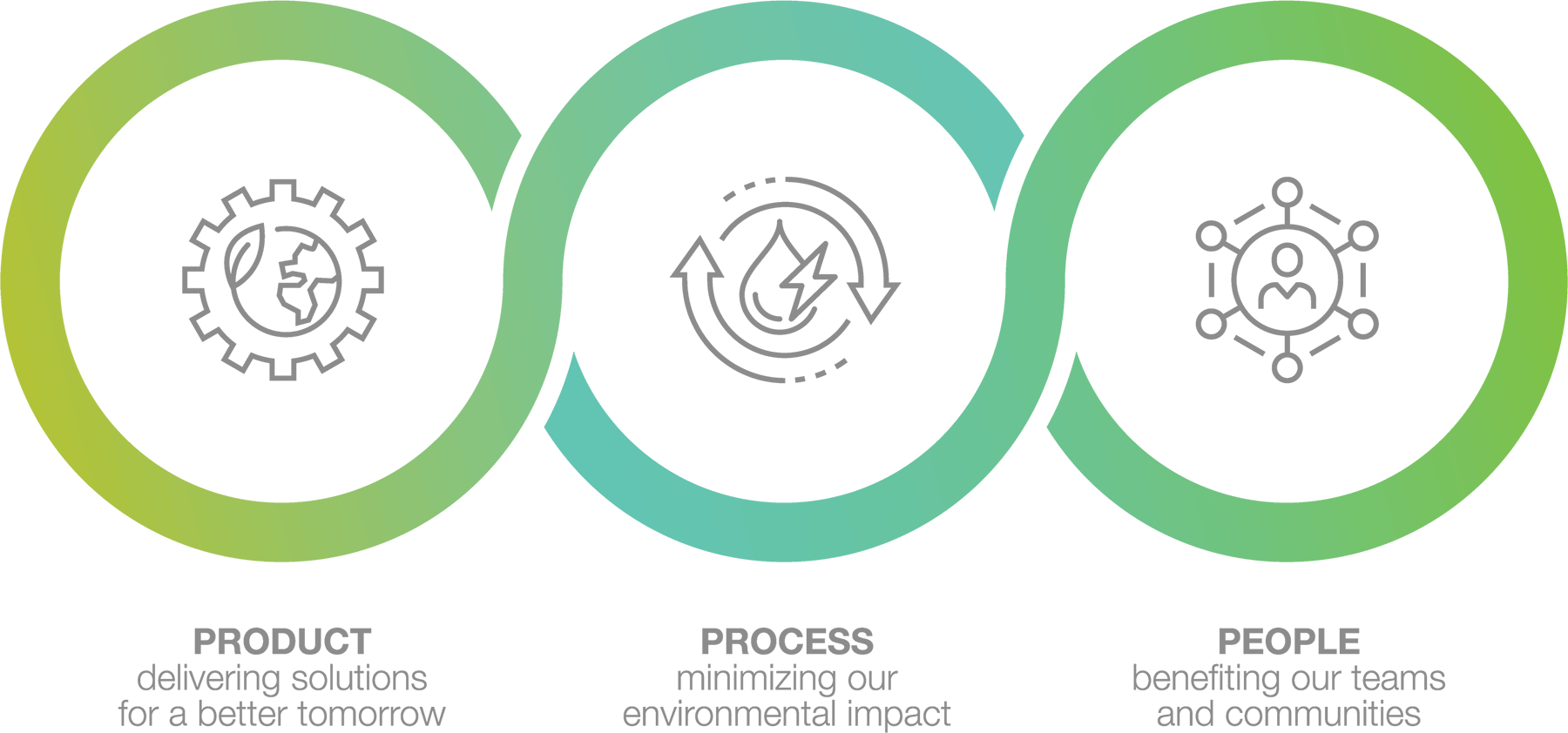
The technology was co-developed by Magna and Zumtobel, an Austrian company specializing in lighting, to replace an older, less-efficient system that used incandescent light bulbs.
Since the implementation of the lighting technology in 2019, Magna Obertshausen has reduced CO2 emissions in this part of the manufacturing process by 4.21 tons per year, with a resulting savings of 4,876 Euros per month. In addition, the LED tunnel has led to a 10-20 percent reduction in the reworking of parts and scrap at the plant.
The light-emitting diode (LED) is one of today’s most energy-efficient lighting technologies, compared to conventional incandescent lights. LEDs are being used in everything from traffic lights and TVs to vehicle brake lights. They last longer than traditional light bulbs, use energy more efficiently and dramatically cut energy usage.
Innovative LED Lighting is Just One Part of an Extensive Energy-Savings Program at Obertshausen
It includes:
- A special project to lower the “room air systems” during the COVID-19 lockdown and production-free period. This initiative reduced energy consumption by 300 megawatt hours in 2020, resulting in a reduction of approximately 120 tons of
CO2 emissions. One megawatt is equivalent to the energy produced by 10 automobile engines.
- The plant’s energy-monitoring program found and eliminated errors in the runtime of the plant’s injection-molding machine, cutting energy consumption from 22,350 kilowatt hours per week to 17,150 kWh per week. This step reduced CO2 emissions
by 2.08 tons per week.
- By lowering the automatic booth air during single-coat painting, when just a primer coat is used, the plant achieved an energy saving of approximately 283 megawatt hours per year and a reduction in CO2 emissions of 113.5 tons per year.
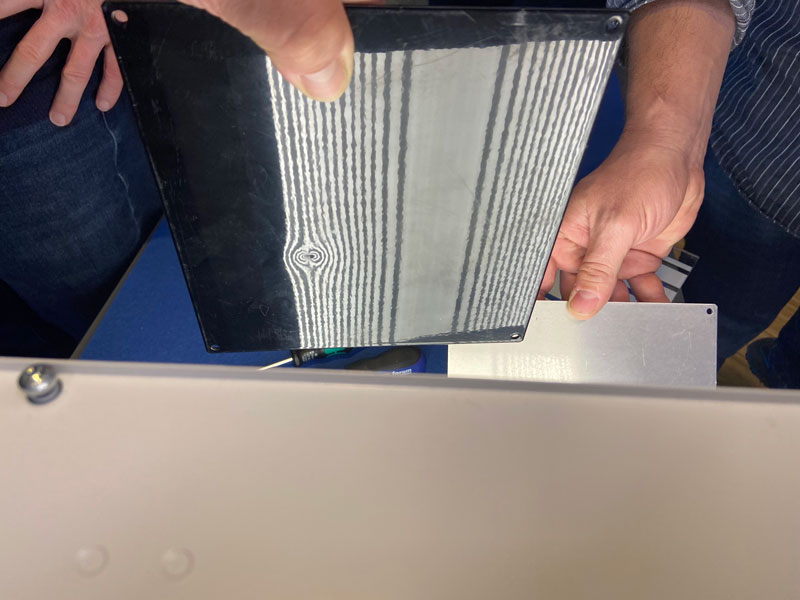
“The sustainability mindset is one of the cornerstones for our 1,150 employees,” said Andreas Spannenberger, the energy manager at Obertshausen.
The dedication to protecting the environment extends far beyond the walls of the plant for employees like Spannenberger and Grunewald.
“My grandson August is 18 months old,” Grunewald said. “I’m trying to make a better world for him. I’m not only working to save energy and reduce CO2 at work, I’m doing the same thing at home. I changed all of the light bulbs to LEDs and I put solar panels on my roof four years ago. I now have zero energy cost. What we are doing at work and at home is a great investment in the future for my grandchildren and generations to come.”
We want to hear from you
Send us your questions, thoughts and inquiries or engage in the conversation on social media.
Related Stories
Stay connected
You can stay connected with Magna News and Stories through email alerts sent to your inbox in real time.