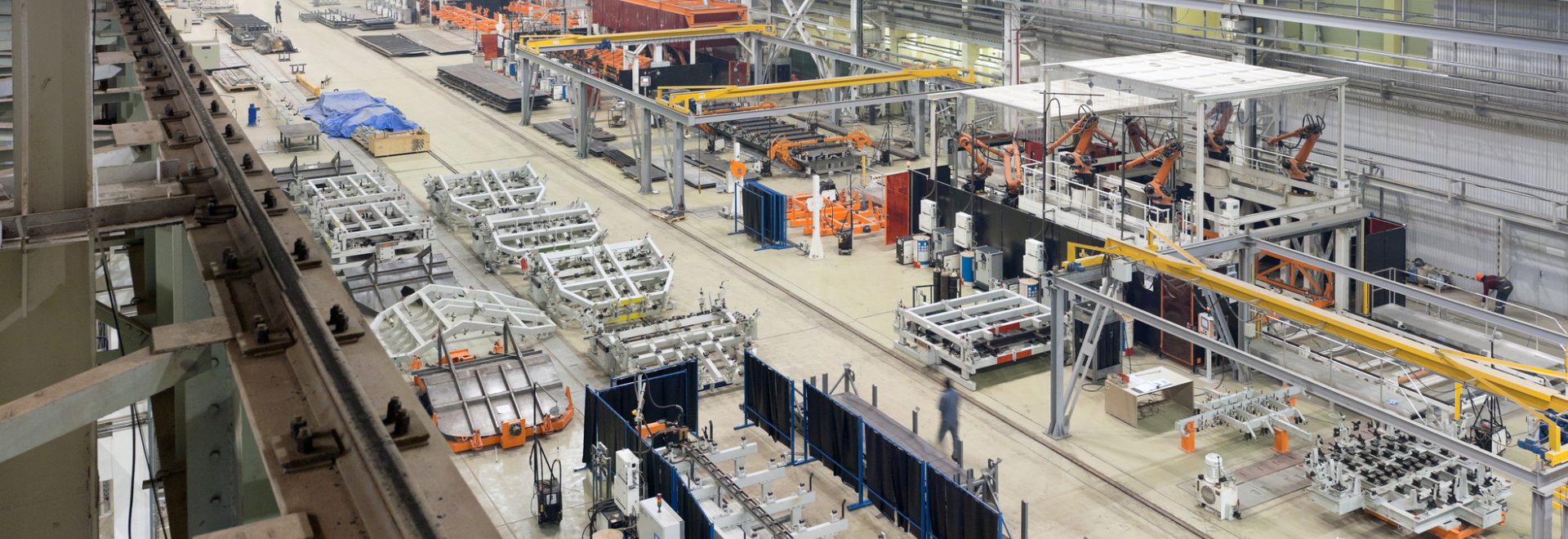
Amalia Ma - Director of Operational Improvement and Quality
Magna Asia
Shanghai, China
Driving World-Class Manufacturing
Big Picture: MAFACT is how we drive world-class manufacturing. It’s a management system and a set of standards that reflect the image of our company.
Passion: It’s a great joy to me that MAFACT helps us to eliminate waste and gives Magna financial benefits, but the most exciting thing is watching teams work together and grow. I love teaching others and helping them develop.
Best Practice at Work: Our Cosma Shenyang division is a benchmark for applying the 5S tools – sort, set things in order, shine, standardize and sustain. Clean, organized divisions with well-trained people in charge of their operations
are critical today and for the Factory of the Future. With robots and automation, you will still need humans to maintain, operate and analyze data.
Best Practice at Home: I taught the 5S rules to my 10-year-old son Hafiz. He uses them to keep his room clean, even though I need to remind him sometimes.
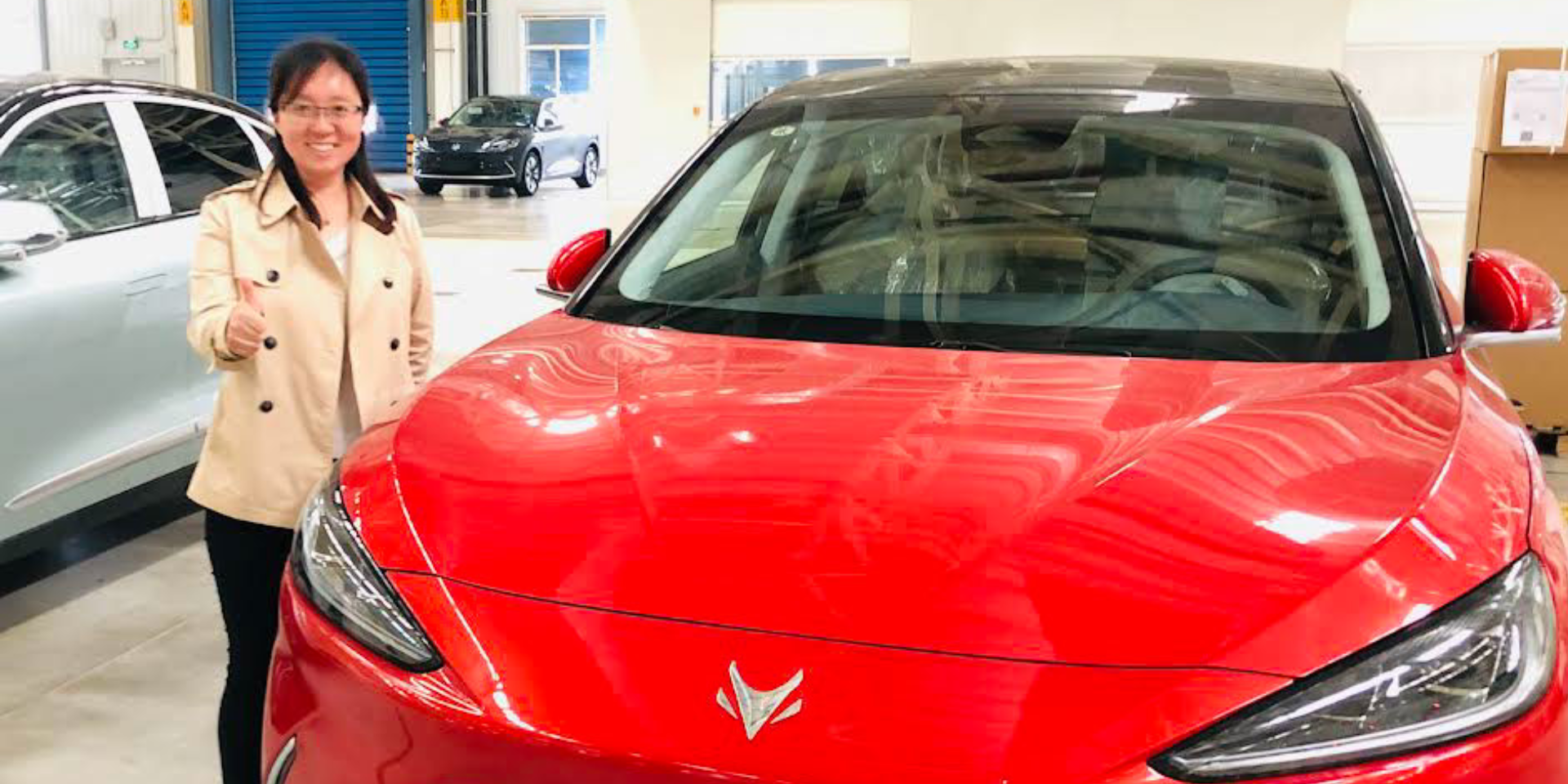
Darren Charbonneau - Director, Global Lean Manufacturing and Sustainability
Magna Mechatronics, Mirrors and Lighting
Newmarket, Ontario
Expecting Change, Driving Out Waste
Big Picture: MAFACT drives stability and continuous improvement by constant change. It isn’t a destination; it’s a journey. The whole point of MAFACT is waste elimination. If you continuously drive out waste, you’ll
have stability, better retention of people and a predictable process where people aren’t afraid to change. In fact, change is expected.
Passion: I’m passionate about the shop floor and the processes that adapt to the shop floor. The people on the shop floor make a product that we can sell. We are their support. This is how we drive quality.
Best Practice at Work: Our Monterrey, Mexico Electronics plant has low downtime, low customer concerns and great standard work. When you do MAFACT well, the outcome is a consistent and repeatable process. And it’s very visible the
moment you walk in the door.
Best Practice at Home: I always try to be efficient with household chores, with the least amount of steps. I use two hands to unload the dishwasher. If you can do this, you’ll increase your speed by 30%. I know this because we use
two hands on our assembly lines to meet cycle time.
Key Takeaway: Magna wants to be the supplier of choice because we have the best quality, lowest lead time and lowest cost. MAFACT helps to get us there.
Adrian Sumarjadi - Director, Global Operational Improvement and Lean Manufacturing
Magna Powertrain
Concord, Ontario
Every Cent of Improvement Counts
Big Picture: MAFACT is a mindset. We want to provide value to our customers with the lowest cost, highest quality and shortest delivery time.
Passion: I like to problem-solve and figure out how to optimize a process or condition. The MAFACT principles allow you to think deeply about the micro-level of cost. We look at the final product and how it’s being processed from every step. If you ship a million parts, every cent of improvement counts. My role is to coach employees to see waste reduction opportunities and spread that knowledge in their divisions.
Best Practice at Work: 80% of Magna’s 24 powertrain divisions have adopted the U-shaped assembly line concept. It’s similar to a U-shaped bar with the bartender and the bottles on the inside. It’s a more flexible and
efficient setup with significant savings.
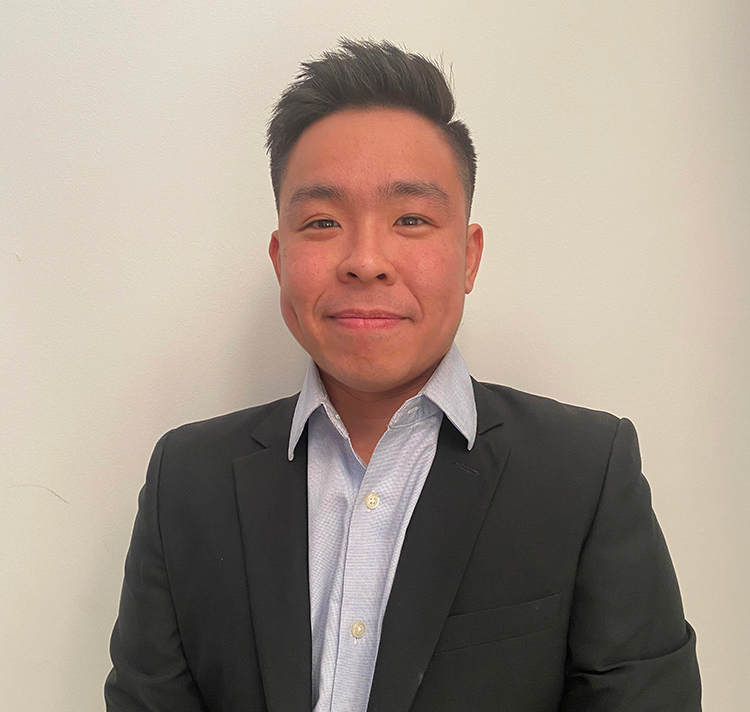
Best Practice at Home: Routine helps me to be productive, from waking up at the same time every day to walking the dog. I always challenge myself, even when I’m cooking noodles. How do I cook them in the shortest timeframe? What
can I do when the water is boiling?
Key Takeaway: MAFACT allows us to be a competitive, world-class manufacturing operation. It also speaks to the sustainability of Magna. By being competitive, it allows the company to last for generations.
Noah Robinson - Senior Manager Operational Excellence
Magna Exteriors
Troy, Michigan
Helping Divisions Grow and Succeed
Big Picture: MAFACT is a tool to help our employees be more successful and our divisions more profitable. By doing that, we attract new business and help make the business sustainable. It’s about job security, but it’s also about treating our resources properly and having a positive effect on the planet.
Passion: I started out as a quality engineer. I like helping people and solving problems. By teaching our employees to use the MAFACT tools, they can solve problems as well.
Best Practice at Work: We use MConnect, a database for idea sharing where everyone can access lessons learned and practices benchmarked at other plants. There’s a contest with a trophy called the MConnect Cup, where 34 divisions
compete every year based on number of ideas submitted and implemented, along with savings. It’s an incentive to use the system.
Best Practice at Home: Visual management is a big part of MAFACT training. Every time I drop my sons Jax and Beckett off at school, I notice the congested carpool lanes and think it would be so much better if I could redesign it. I have
not addressed this with the school administration yet, but I’ve been tempted to.
Key Takeaway: MAFACT is about helping our divisions grow and succeed. When you put the operational principles in place, it helps to prevent and solve issues.
Adriano Lima - Global Operational Excellence and Sustainability Manager
Magna Cosma
Perth, Ontario
Empowering People
Big Picture: MAFACT and sustainability go together. Both pursue a world-class approach for people, process and product. With this as our operational excellence guideline, it’s a way to envision our future and how we develop a business
that protects the planet, as we keep Magna as the right choice for investors, customers and employees.
Passion: I started on the shop floor and worked my way up to operations management and improvement. When I was a quality coordinator, I was invited to participate in a workshop where operators were allowed to speak about their ideas. That was the ‘aha’ moment that drove my career and education. The only place where we get consistent results is where things happen – at the shop floor. You must use the experience of everyone to continuously improve.
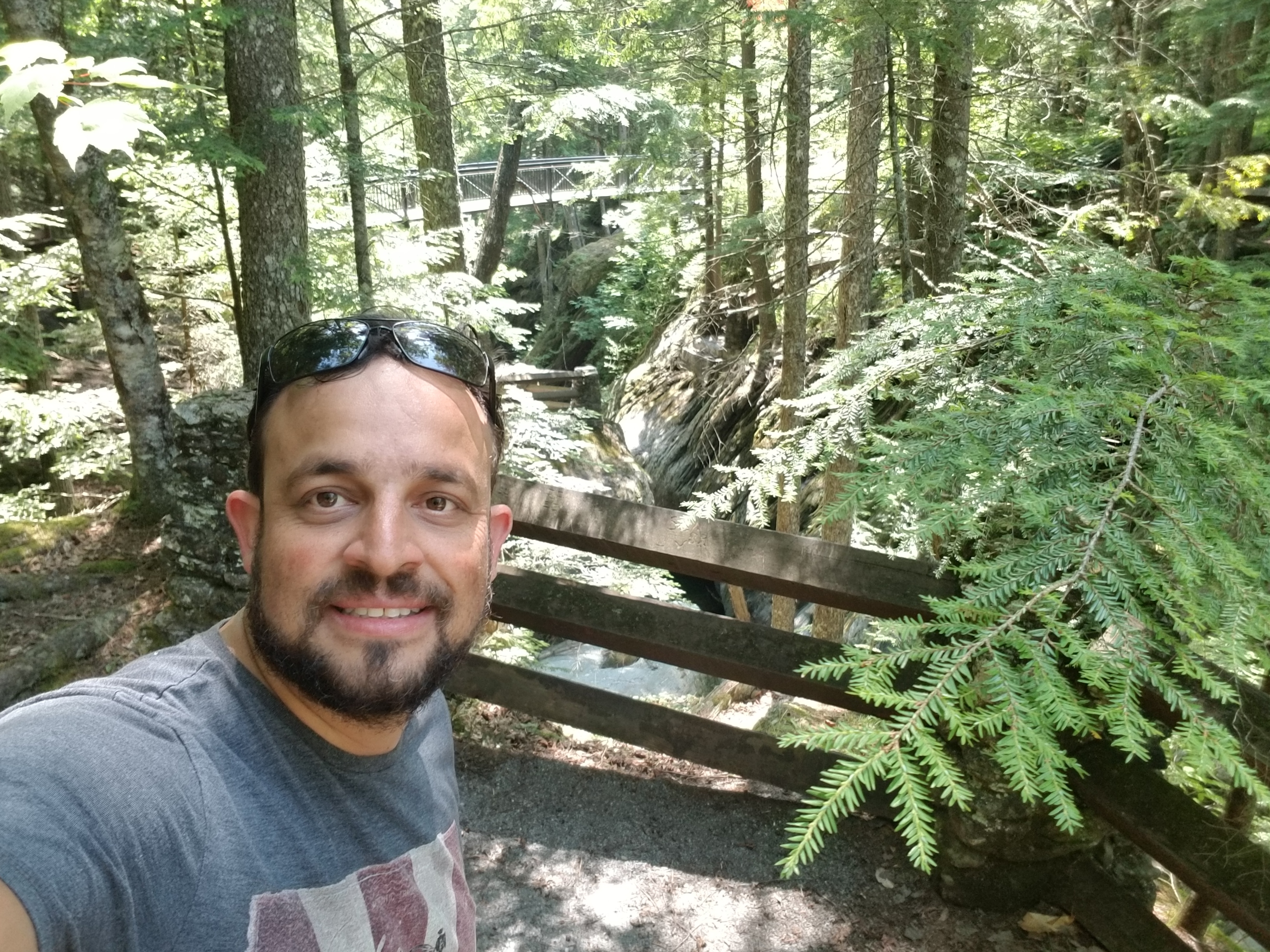
Best Practice at Work: Cosma Casting Poland used MAFACT to improve and turn around its business by involving people. For example, they invited me to train all of the division’s team leaders to create 100% of their standardized work. They understood what the production workers needed. Shop-floor involvement is critical.
Best Practice at Home: It’s not possible to split the mindset after doing this on a daily basis. I’ve become a data-driven person. I’m getting a new roof on my house and I know every single detail of the project and execution. I’m the same way with supermarket lists – really organized.
Key Takeaway: Our main goal is to have our people engaged, motivated and aligned. Doing the best for our business, investors, employees and customers. That’s what drives our operations. MAFACT empowers people to have great results.
Samir Khaled - Director of Continuous Improvement
Magna Seating
Novi, Michigan
Keeping It Simple
Big Picture: MAFACT is a system that puts procedures and policies in place, and affects everything you do. When you dissect it, it’s very simple: Use common sense, communicate and understand the true problems.
Passion: I enjoy coaching individuals and preparing them for future opportunities. I’ve had hourly associates who became team leaders. One just got promoted to assistant general manager. With MAFACT and a background in lean manufacturing, you don’t need high levels of education. You need an open mind and the will to do better.
Best Practice at Work: At Integram Windsor Seating, we used MAFACT and lean manufacturing principles, and got a slamdunk in all categories, including health, safety, quality and cost savings. We tore out traditional assembly lines and went from a manual system to one using automated guided vehicles for production lines. It’s opening new opportunities and helping overall business.
Best Practice at Home: My family of 6, including four kids, is moving to a new house. We used 5S quality tools that are part of MAFACT to clean a messy closet filled with jackets, shoes, toys and cat food. Now, the closet is immaculate.
Key Takeaway: MAFACT keeps us competitive in a competitive world with current and new customers. MAFACT is listening, understanding and keeping it simple. Work with your peers. Understand their problems and fix them.
Robert Strassberger - Head of World Class Manufacturing and Operational Improvement
Magna Steyr
Graz, Austria
Gearing Up for Excellence
Big Picture: I like to compare MAFACT to a gear set, where everything works together. MAFACT is a holistic approach to achieving excellence that includes manufacturing excellence, quality, environmental health and safety, logistics, human resources, engineering, management and cost.
Passion: Never settle is one of my principles at work and in my private life. It means never be satisfied with the current status. That’s why I work for a company like Magna that is driving innovation and improvement.
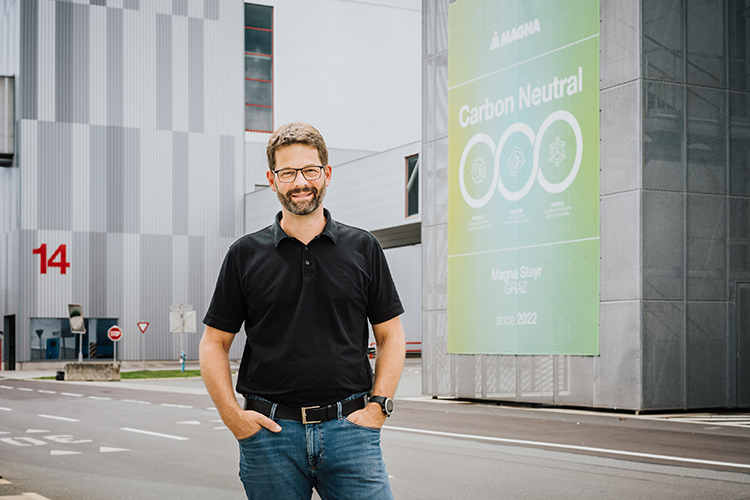
Best Practice at Work: MAFACT is always challenging us to make improvements in energy reduction and energy savings. Since the beginning of 2022, the Magna Steyr plant in Graz, Austria, is CO2 neutral, a sustainability achievement that was also driven by MAFACT. We are a big global company with so many ideas. It’s very easy to share best practices in all areas of expertise. If we are collaborative and work together, we will continue to improve our processes, technologies, procedures and methods, eliminate waste and use our resources effectively.
Best Practice at Home: I’m always trying to reduce energy consumption at home. I installed a heat pump and solar panels on the roof this spring, and I’m driving an electric vehicle. I consider these measures an investment in the future, especially for my eight-year-old daughter Helena.
Key Takeaway: There’s a connection between MAFACT, world-class manufacturing and moving forward for all. Everything is linked. It’s a great combination.
Everardo Villarreal - Global MAFACT Sustainability and Energy Leader
Magna Electronics
Guadalupe, Mexico
An Evolving Concept
Big Picture: I like to compare MAFACT to a gear set, where everything works together. MAFACT is a holistic approach to achieving excellence that includes manufacturing excellence, quality, environmental health and safety, logistics, human resources, engineering, management and cost.
Passion: I started out as a Magna engineer who likes continuous improvement. The people around me can feel that emotion. They are not excited by an org chart; they are excited by passion. It feels good when you shake hands with the team and say, ‘Great job!’
Best Practice at Work: Continuous improvement at the Magna Monterrey division in Mexico means using automated guided vehicles we call “Magnaritos” to help with material flow from the warehouse to the shop floor. It means going paperless for sustainability and using iPads for tracking and other tasks. It’s using checklists to chart projects, and the movements of people and materials. And it’s training other divisions about the benefits of total productive maintenance for quality and reliability.
Best Practice at Home: I teach my kids, Everardo, 8, and Leo, 5, to do simple steps with the laundry, to separate the colors and maximize water use. When I go to parent-teacher conferences, the teacher says they are very organized.
Key Takeaway: MAFACT an evolving concept that makes Magna sustainable, competitive and attractive. We have to move forward all the time. MAFACT helps us get there.
Christoph Bistricky - Director, Operational Improvement Europe
Graz, Austria
Listening to Fresh Perspectives
Big Picture: MAFACT is about creating a culture of continuous improvement. With clear goals and supportive management, every day should be a little better than the day before.
Passion: I have a passion for lean manufacturing to eliminate waste. After spending five years in a Magna division in Ramos Arizpe, Mexico, I knew I wanted to work exclusively in this area. Each and every decision we made at this powertrain plant was connected to lean manufacturing.
Best Practice at Work: The right coach and mentor can make a big difference. An impressive role model in this respect for me is a Magna executive who lives MAFACT and totally transformed a division in Spain. He had a detailed plan and a strict routine, which made everyone focused and effective, with everything running smoothly. This kind of structure and coaching is especially important for young employees who have so much potential.
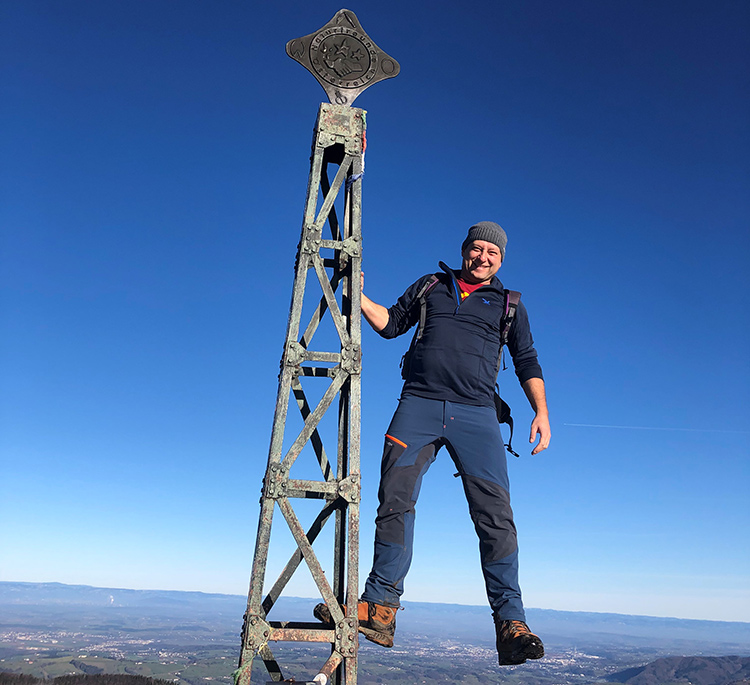
Best Practice at Home: I make detailed plans for everything, including “action trackers” for the weekend. My wife and I sit together on Friday evening and we write down everything we’ll do, including what we’ll cook, what we need to do around the house and in the garden. On Sunday evening, everything is done and we are happy.
Key Takeaway: You can drive continuous improvement if you are open-minded and listen to fresh perspectives.
Mark Cooper - Director, Operational Improvement and Lean Manufacturing,
The Americas
Aurora, Ontario
Leading the Market
Big Picture: If you walk into any of our plants, you will recognize that MAFACT is the way we run our business. You will see standardized displays, highly clean and organized operations, and people working on flexible lines. To paraphrase Henry Ford, “Standardization is the first step to continuous improvement.” MAFACT is all about solving problems and engaging all aspects of the organization to that end.
Passion: My personal passion is critical thinking: How to recognize problems, understand root causes and effectively eliminate them from ever occurring again.
Best Practice at Work: At the Magna Karmax division in Milton, Ontario, they were able to free up space by implementing MAFACT principles to reduce inventory, eliminate waste and make other improvements. In fact, they were able to free up enough space to launch a completely new program to build structural components for Honda without adding bricks and mortar. That is a great example of value-added assembly.
Best Practice at Home: I use A3 thinking for problem solving. It’s a collaborative process management and improvement tool developed by Toyota that fits onto an A3-size 11x17 sheet of paper. For anything that I want to achieve in life – getting the kids through school, career aspirations, family matters – I sit down and write an A3.
Key Takeaway: The goal of MAFACT is to be the lowest cost, highest quality and shortest lead-time manufacturer. That’s what makes Magna the market leader.
We want to hear from you
Send us your questions, thoughts and inquiries or engage in the conversation on social media.
Related Stories
Stay connected
You can stay connected with Magna News and Stories through email alerts sent to your inbox in real time.