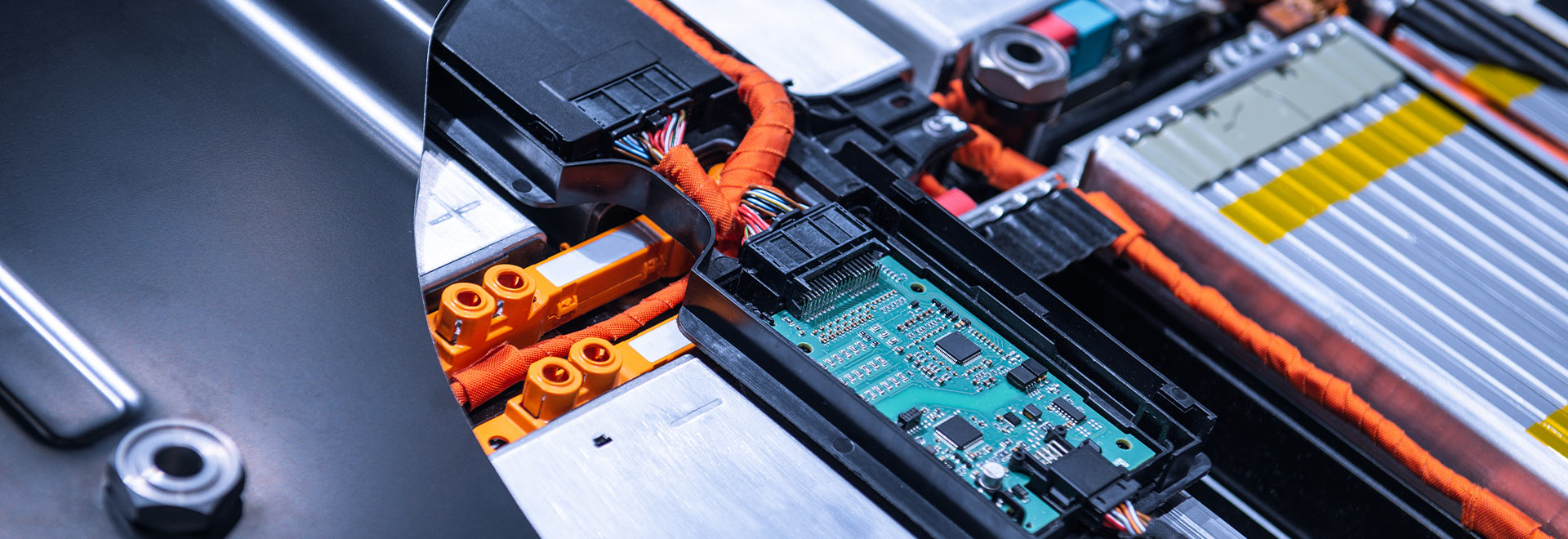
Battery Development for High
Voltage Battery Electric Vehicles – A Supercharged Subject
- Oliver Heidenbauer
- September 24, 2023
- 6-min read
High voltage batteries are not only the largest and most expensive module of any battery electric vehicle, but they also hold a key function for almost any expected feature in a BEV, from performance to security. The final battery is much more than just a case into which the cells are stacked to save as much space as possible, but an integral element of the vehicle’s architecture.
Integrating the high voltage battery development into the complete vehicle system of a BEV is one of the most important tasks of any vehicle project. And the development of new battery electric vehicles currently accounts for the vast majority of projects carried out by development specialists in close cooperation with OEMs.
TABLE OF CONTENTS:
> Target conflicts in high voltage batteries – Setting targets depending on the vehicle type
> A hot topic – Thermal security of high voltage batteries
> Dividing the load – High voltage battery as an integral component of the chassis
> In the beginning, there was the cell – Parallel development of battery and cell
> Regulations and rules – Slow and steady makes the law
> Conclusion: Extensive experience in all areas of development reaps the most benefits
TARGET CONFLICTS IN HIGH VOLTAGE BATTERIES - SETTING TARGETS DEPENDINGON THE VEHICLE TYPE
Considering the many requirements of a finished battery pack, it is impossible to isolate only one as the most important. That is why main requirements need to be defined in the earliest stages of any vehicle project and in cooperation between the development partner and OEM, depending on the use case of the vehicle through Vehicle Target Setting (VTS). These main requirements may vary since a limousine prioritizing driving range and energy efficiency has different key development aspects than a multifunctional SUV, a compact car for urban settings, or an all-terrain vehicle. Development specialist MAGNA works with a set of 40 main Key Performance Indexes (KPI) – a number which by itself indicates the variety of requirements within high voltage battery development.
Part of this process is solving target conflicts. Maximum energy density (as much stored energy in as little space as possible) can conflict with indispensable security requirements, a boost charge feature can weigh down on the battery’s life span, etc. A vehicle’s driving range is not solely influenced by battery capacity, but also by how efficiently the complete vehicle uses the provided energy. A rather large but heavy and expensive battery will not provide more driving range when used inefficiently than a smaller, but efficiently used battery. Additionally, boost charging will only make sense in combination with optimized battery, charging, and thermal management – or else the battery cells’ aging is accelerated.
Depending on the vehicle’s concept, optimizing driving range must also be balanced against protection against external impacts since electric all-terrain vehicles could be damaged from underneath when travelling off-road. This is not only achieved by strengthening the vehicle’s chassis, but also by providing enough free space to avoid damage by indentations to battery cells, conditioning, and sealing systems. However, these measures reduce possible packing density of cells and thus volumetric energy density.
A HOT TOPIC - THERMAL SECURITY OF HIGH VOLTAGE BATTERIES
The thermal security of high voltage batteries will always be an important issue – especially for the general acceptance of battery electric vehicles. Therefore, preventing incidents relevant to the battery pack’s security by implementing suitable measures is a central aspect of battery development.
On the cell level, thermal runaways are particularly important to watch out for. A thermal runaway occurs when electrochemical processes inside the battery get out of control due to overheating, thus creating more heat and further thermal runaways.
On the pack level, one thermal runaway can ‘infect’ other battery cells and start a chain reaction called thermal propagation.
Occasionally, news and videos of burning battery electric vehicles that cannot be extinguished will circulate traditional and social media. Stories like these regretfully nurture the myth that BEVs and their battery packs are easily ignitable. However, this statement cannot hold its ground on an empirical level. Studies show that the probability of a battery electric vehicle catching fire only corresponds to a fraction of the fire risk of an ordinary combustion engine vehicle (ICE).
According to a study from the Jülich Research Center of the Helmholtz-Institut in Muenster, only two fire incidents on average occurred per billion driven kilometers in battery electric vehicles. On the contrary, about 90 fire incidents on average occurred per billion driven kilometers in combustion engine vehicles. Of course, this data is based on relatively new technology, so the first vehicles produced on a larger scale have not yet exceeded a ten-year lifespan. Nonetheless, the numbers clearly show that the security of battery electric vehicles is on par with combustion engine vehicles when it comes to both ignition risk and fire load, i.e. the mass of combustible material.
Ignition risk in BEV and ICE
However, how a fire progresses is utterly different in these vehicle types. An ICE burns out quite quickly as soon as the carried fuel ignites. In contrast, a BEV burns out slowly, sometimes even over the course of several hours since thermal runaways slowly spread from cell to cell instead of the entire fuel supply combusting at once. This delayed reaction might seem more treacherous, but it is actually safer for the passengers. Even when the thermal runaway of a battery cell has already started, there is more than enough time for the passengers to safely evacuate the vehicle. That is why a UNECE legal standard dictates that at least five minutes must pass from the first detection of a thermal incident and the possible endangerment of passengers. Today, this standard has already been outperformed as recent designs strive to eliminate the possibility of a thermal propagation event altogether.
A variety of possible causes – thermal incidents in high voltage batteries
Surprisingly, the internal short circuit of cells is only seldom the cause for a thermal runaway, and in extreme scenarios, a thermal propagation. In most instances, the self-induced runaway of a battery pack usually happens because of quality deficits during the production process of the battery cells, especially through the contamination of the cell’s inner chemistry. However, production processes today are much more refined than in the past, and that is why internal runaways are not supposed to happen without outside influence anymore.
However, various other factors that might lead to a cell’s runaway can be prevented by appropriate countermeasures. For example, an infringement of operation strategy of either the cell or the cell’s chemistry due to temperature, charging or discharging performance. Under such subpar circumstances, dendrites can form – twig-like structures inside the cell that can permeate separators and cause internal short circuits afterwards.
Mechanical damage is another significant risk that needs to be prevented in the development and integration of high voltage batteries into the vehicle. This type of damage can occur through the short-term effect of extreme forces. For example, during a massive accident with extensive destruction, or through slow deformation from outside, like when a foreign object indents or perforates the chassis during off-road usage of the car. Fires caused by other vehicle components can also heat the battery from the outside, leading to a thermal incident. Examples are flashovers from low voltage electrical systems or the combustible cooling agent in the air condition. There is also the possibility of short circuits outside the battery pack that heat the high voltage paths, e.g. from the engines, the onboard-chargers, or DC/DC-converters. Finally, longer periods of strenuous use might also lead leaks in the battery enclosure, allowing moisture and dirt to intrude into the battery, which in turn might lead to electrical conduction and a short circuit inside the battery pack.
DIVIDING THE LOAD - HIGH VOLTAGE BATTERY AS AN INTEGRAL COMPONENT OF THE CASSIS
Although all these potential dangers are improbable, they still need to be seriously considered during the basic conceptual design of the vehicle and the battery development phase. For that reason, the robustness of the battery against outside influences is tested thoroughly. Development expert MAGNA usually tests extreme load cases via simulation, as well as during the entire design verification process (DVP). The high voltage battery must endure these tests without sustaining serious damage like deformations on the cellular level, leaks, or loss of functionality. Battery development and vehicle design must work closely together since the high voltage battery pack contributes heavily to the structural performance overall. That is because the body shell, underbody, and battery case divide the load transmission – in normal operation as well as in case of an accident.
IN THE BEGINNING, THERE WAS THE CELL - PARALLEL DEVELOPMENT OF BATTERY AND CELL
Development of the battery cells usually starts long before the actual development of the vehicle itself – even if the battery cell supplier has already been chosen at the beginning of the battery development. This is particularly common in projects with larger OEMs that already have a steady business relationship with cell manufacturers or have set foot into cell production themselves. If not, a suitable cell manufacturer needs to be chosen according to the specific requirements of the project. The overall battery development is neither accelerated nor slowed by this process since the development of battery and cells proceed parallel to each other.
To choose a suitable cell manufacturer, multiple basic concepts are developed by adaptation from the vehicle’s requirements first. Different cell and cell module manufacturers can then be easily compared and assessed from a technical perspective for the respective project. After evaluating other criteria like cost, quality, and production capacity, a recommendation for an eligible business partner can be provided. However, there is a stable trend across all cell suppliers towards continuously improving the cells’ chemistry regarding capacity, aging, security, and cost factor. Cell integration also takes further strides in development, and the general energy density of high voltage batteries is increasing by 10 to 15 percent each year.
The higher the integration degree, the higher the challenge
A few years ago, batteries were mostly created by using the module-to-pack method, i.e. by combining multiple cell modules into a battery pack. Nowadays, there has been a change towards the cell-to-pack method by integrating large arrays of combined cell formations into a battery pack. However, there is already a new approach on the horizon which integrates the cells directly into the chassis of the vehicle. This way, the cells’ packing density as well as their gravimetric and volumetric energy density can be further improved. But with the ever-increasing compactness of cell integration come technical difficulties regarding the prevention of thermal propagation. In the future of this development, new materials need to be introduced that can stop, or at least decelerate, the spread of heat from one battery cell to another.
The most important countermeasure against the overheating of a runaway cell is the dissipation of excess heat before it can infect another cell. In addition, increasing pressure created by the heating process needs to be safely released in a controlled fashion before the cells can burst open. That is why safety vents inside the casing are required. Additional pipes within the casing design can also help to divert hot gases over 500°C so that the heat cannot transfer to other battery cells. Moreover, a type of cell which can switch itself off if electrochemical processes reach critical temperatures is currently in development.
Creating a battery electric vehicle that is safe under even extreme circumstances is only possible if measures for the battery cell, the battery pack, and the complete vehicle work together. That is why having battery development and vehicle development under one roof can bring great benefits since they need to work hand in hand with each other to guarantee the best possible outcome.
REGULATIONS AND RULES - SLOW AND STEADY MAKES THE LAW
Of course, there are different legal regulations in place for high voltage batteries in BEVs depending on the location of the respective market, but they are always subject to steady change. However, it is almost impossible for battery developers to just consider regulations that are effective at the start of any given project since battery development is quite time-consuming. Depending on available resources – like how far the vehicle concept design has come, and in which state of maturity the battery cells are –battery development takes around three to four years. During this time frame, legal regulations usually change or are about to change.
Thus, vehicle developers need to be acutely informed about regulations that are currently in place, planned for the future, under development, or available as a draft at the moment. But years can pass until those early drafts become legally binding. On one hand, because there are always attempts to find and solidify global standards. On the other hand, committees for standardization work steadily, but slowly. Nonetheless, even trying to fulfill future regulations might be an insufficient effort to stay ahead of legal changes. That is why a competent battery developer will always strive to outperform current and even future requirements since an OEM’s vehicle project will stay in production for a long period of time and must keep conforming to regulations all the while.
CONCLUSION: EXTENSIVE EXPERIENCE IN ALL AREAS OF DEVELOPMENT REAPS THE MOST BENEFITS
There are quite a few inexperienced battery developers that pop up more spontaneously on the market and present concepts that seem attractive at first glance. However, a closer look usually reveals that these concepts cannot be applied to reality. Oftentimes, the battery is only developed in isolation and the requirements of the complete are not thoroughly considered. Working with an experienced development partner can prevent many problems down the line and reap a lot of benefits. MAGNA offers extensive competence in all areas of vehicle development and can provide the best solutions for high voltage battery development without time-consuming and costly errors.
Stay connected with Inside Automotive!
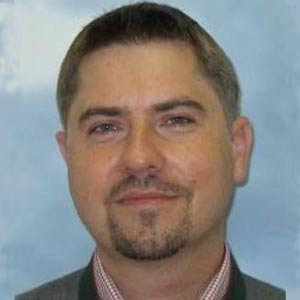
Oliver Heidenbauer
Oliver Heidenbauer is Group Leader of Electrical Storage Systems at Magna Steyr. With two decades of experience in the automotive industry, he has significant expertise in the development of HV components. His career in electronics/electrics started in 2003 as an SE team leader in physical wiring systems in complete vehicle engineering. He completed his apprenticeship as an automotive electrician and master car mechanic. He also graduated from the School of Electric & Electronic engineering, including SW development, and completed his business management qualification.
We want to hear from you
Send us your questions, thoughts and inquiries or engage in the conversation on social media.
Related Stories
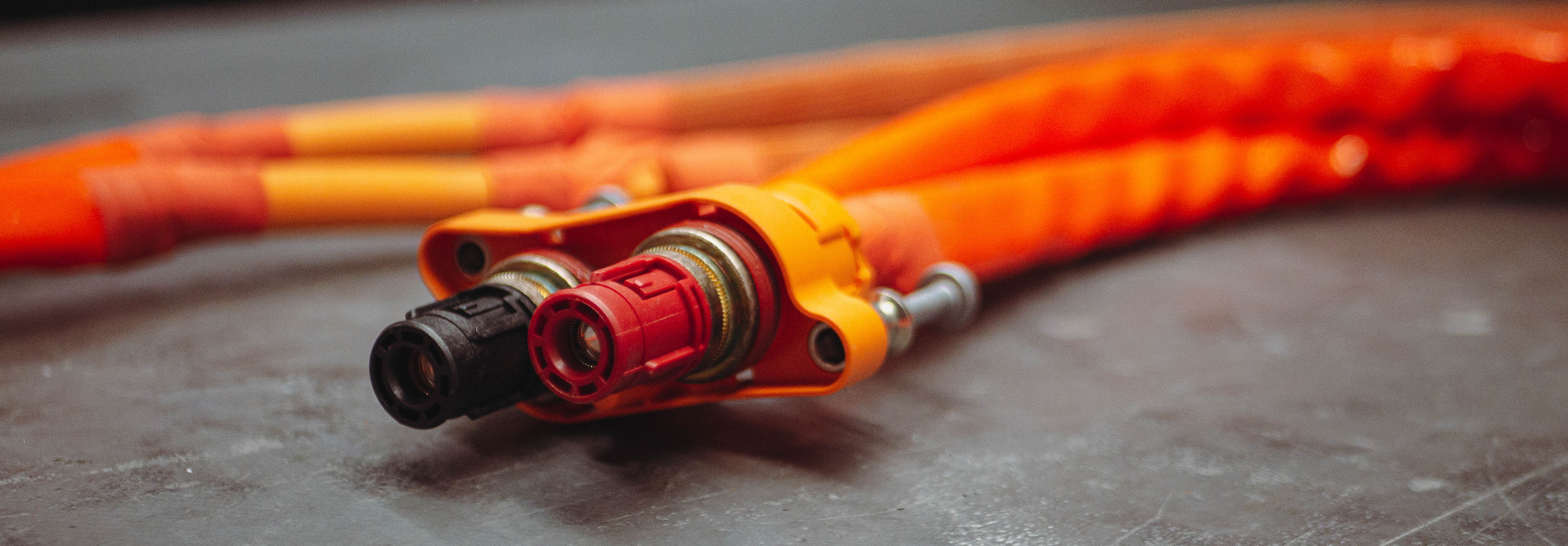
Test First, Then Enter the European Market: Professional Battery Testing Examines More Than Just the Charging Curve
Blog
Stay connected
You can stay connected with Magna News and Stories through email alerts sent to your inbox in real time.