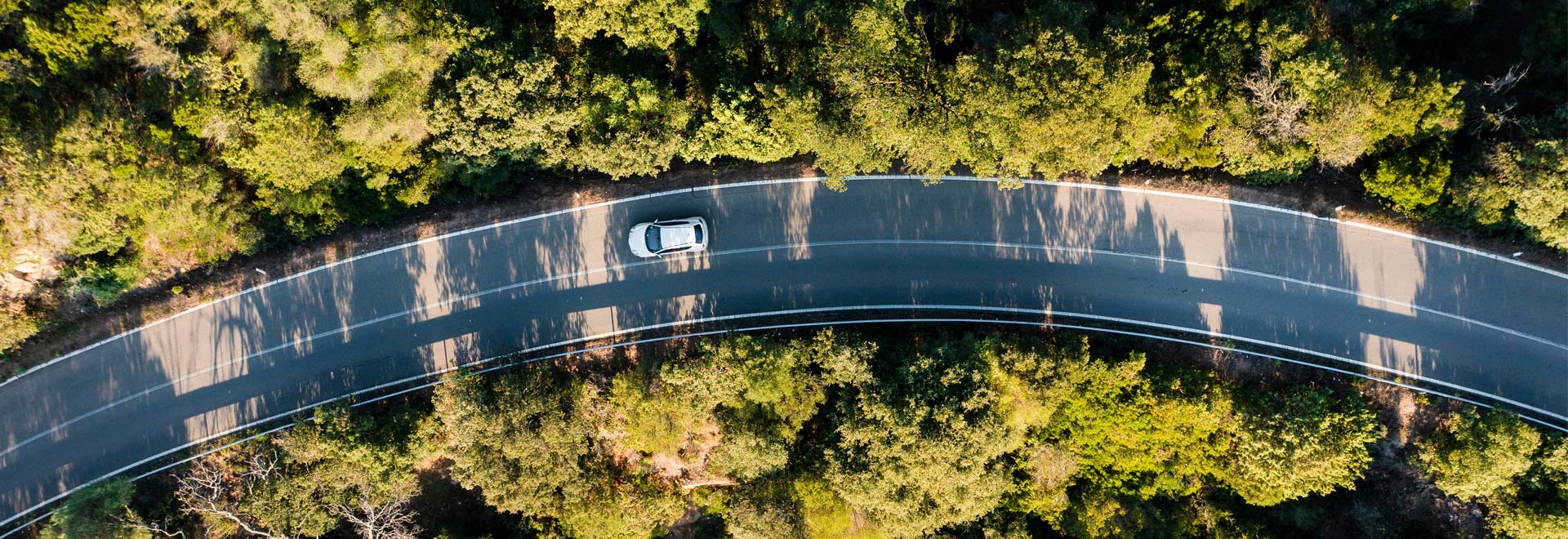
Many Roads Lead to Driving
Range – Energy Management in EVs
- Michael Martin
- August 22, 2023
- 6-min read
One of the primary goals of developing a battery electric vehicle (BEV) is maximizing the vehicle’s driving range via optimal energy management. It is mostly determined by a combination of efficiency and battery size. However, implementing a bigger battery with greater energy reserves does improve driving range, but it also increases the overall weight of the vehicle, and therefore actually decreases efficiency. However, efficiency is an important criterion for the end customer because it determines the cost of each kilometer driven in vehicle operation.
The development team’s aim is not only to maximize the nominal range under the normal and favorable conditions of WLTP testing, but also improving the real driving range and cost factors which are relevant for the customers. High customer satisfaction can only be ensured long-term if a vehicle shows good performance in these factors, within a close range of WLTP test scores. And that is, of course, of central interest to vehicle manufacturers.
Compared to internal combustion engine vehicles (ICE) with its multi-step transmission, electric vehicles come with significantly fewer adjusting screws within the powertrain itself to minimize real energy consumption and thus optimize driving range. Therefore, factors that influence the overall vehicle are of particular importance here. These factors include, among others, aerodynamics, reducing friction losses, and minimizing rolling resistance.TABLE OF CONTENTS:
> A holistic examination of the overall vehicle
> A drive formula, tailored to the destination – All-wheel drive can be efficient
> Converging nominal range and real driving range
> Are tires part of energy management?
> Thermal management as an important part of any energy strategy
> Driver Coaching as a chance to improve real efficiency
A HOLISTIC EXAMINATION OF THE OVERALL VEHICLE
Even if the same type of battery and power train are used, there is a significant difference in energy consumption and driving range depending on the vehicle’s basic concept and design. For example, SUVs are designed for greater spatial proportions, better aptitude for rough terrain, and powerful tractive output for pulling trailers. Of course, these use cases do not allow much leeway for energy efficiency. Hence, an SUV will never range the same efficiency levels as an aerodynamically advantageous, minimal weight vehicle optimized for high driving range.
Nonetheless, even the energy management of a vehicle with high consumption can be improved by optimizing elements of all divisions. One such approach to improve driving range is the efficient construction of the engine. In the next step, frictional resistance is minimized in the remaining power train. Then, tractive resistance (which consists of aerodynamics, rolling resistance, and overall vehicle weight) is reduced as much as possible. Thermal management also plays an important role in increasing the efficiency and therefore, the driving range of a battery electric vehicle (BEV) because unlike with ICE vehicles, energy for heating must also be borrowed from the battery.
A DRIVE FORMULA, TAILORED TO THE DESTINATION – ALL-WHEEL DRIVE CAN BE EFFICIENT
A power train’s basic concept must be suited to the needs of the intended target customer group. Hence, it should be designed in a way that solves target conflicts regarding the different customer’s expectations of the vehicle. One customer group might prefer good driving performance while another group is focused more on energy efficiency. A modular power train building block system offers a great solution for this problem. With this modular system, it is easily possible to build a version of a vehicle with one powered axle and another version of the same vehicle with two powered axles. While the vehicle with one powered axle can be offered as an entry level model build for driving range, the all-wheel drive vehicle acts as an alternative with higher overall performance. Moreover, the all-wheel drive feature provides an attractive additional selling point for any battery electric vehicle. The active torque distribution between the two drive axles presents another possibility to positively influence driving dynamics.
Optimizing power train design
On the surface, an electrified all-wheel drive has certain disadvantages conditioned by principle, like how two powered axles can increase overall weight and decrease available space within the vehicle’s design. However, higher performance potentials also enable better output levels in BEVs, since they perform better in partial load scenarios than internal combustion engine vehicles. This is already in use today with serialized vehicles. Also, even vehicles with one powered axle are usually outfitted with an overdesigned engine since the real use of BEVs incurs fewer high loads. This is especially important for constant driving as this use case is the most common type of normal driving operation.
There are more advantages to harness from all-wheel drives by decoupling one axle, for example the secondary axle, during phases of constant driving. This proves especially effective in combination with complementary rating of the primary and secondary drives.
Here, the rating of the drives occurs in a way that the efficiency sweet spots lie in different velocity ranges, which makes them complementary to each other. This way, two drives can create a far broader efficiency sweet spot through the complementary usage than only one drive ever could, resulting in a simultaneous increase of performance potential.
These advantages are of particular use to vehicle segments that need high performance anyway due to high driving range and consequently, heavier batteries. Usually, this also coincidently overlaps with vehicle use cases which are defined by higher customer expectations of traction and drive dynamics. Hence, it depends on the individual use case which solution makes more sense. However, contrary to ICE vehicles, an electric all-wheel drive can actually prove more economical.
CONVERGING NOMINAL RANGE AND REAL DRIVING RANGE
How much the WLTP nominal range and the real driving range of a BEV deviate from one another heavily depends upon usage profile: How similar is the expected vehicle usage to the standardized measurement methods according to the WLTP driven run? Generally, nominal range can be useful information for the end customer to objectively compare different vehicles. However, standardized measurements can never accurately reproduce the real vehicle usage of a specific end customer since nominal range is determined by a fixed run simulating urban traffic, rural traffic and highway traffic. That is why there can inevitably be higher values if the real usage varies from this particular route type allocation. For example, driving primarily on the highway will increase energy consumption and shorten the driving range. Thus, the aim of holistic energy management is to converge these two values in the development phase already.
The way this is achieved varies greatly depending on the vehicle’s concept and must be specified in the cooperation between OEM and development partner. On one hand, aerodynamics and the tires’ rolling resistance are much more important for vehicles meant for frequent long-distance travelling at higher velocity. On the other hand, a battery electric vehicle meant primarily for urban short-distance traffic with frequent deceleration, stagnancy, and subsequent run-ups must be optimized in terms of minimizing overall weight, maximizing the recuperation of braking energy, and optimizing energy demand for the vehicle’s A/C.ARE TIRES PART OF ENERGY MANAGEMENT?
Minimizing tractive resistance as a central element of energy management determines the choice and design of individual vehicle components. Tires play a key role in that matter. On one hand, wheels and tires are an important design element and must match the vehicle’s overall style. On the other hand, they also heavily influence tractive resistance. This not only applies to rolling resistance itself, but also to air resistance and weight. A tire that bears on a small surface area and barely churns minimizes not only rolling resistance, but also decreases air resistance due to its low width. However, a tire with relatively hard rollover reduces driving comfort and negatively influences driving dynamics. Therefore, a higher effort must be made while developing the chassis and modulating control systems for driving dynamics to ensure an acceptable comfort experience and safe driving behavior of the vehicle. Depending on the OEM’s requirements, tradeoffs in one area are necessary in order to optimize another area.
That is why OEMs can profit greatly from a development partner like MAGNA since they not only provide decades-long experience in all areas of vehicle development and adjusting components, but can also validate the systems’ performance and robustness in on-location test sites and test rigs.
THERMAL MANAGEMENT AS AN IMPORTANT ELEMENT OF ANY ENERGY STRATEGY
The design and adjustment of the thermal system plays a particularly important role in the energy management of battery electric vehicles. Since the WLTP measurements of the nominal range are run in 23°C environmental temperature and without climatization, there is no consideration for energy consumption due to the climatization of the vehicle and the electric batteries. However, this aspect can have a great impact on the real driving range since the thermal system influences both climatization and performance potential while charging and driving. On one hand, the higher energy demand due to heating the passenger cabin during cold environmental temperatures increases energy consumption and battery strain, and negatively impacts the energy balance. On the other hand, efficient battery cooling can greatly benefit fast-charging capabilities and the high-performance aptitude of the power train.
However, even in this area, compromises are necessary and must be made according to the requirements of the individual vehicle project which the OEM and development expert have defined together. Involving the development partner in an early stage of the project can not only shorten the overall development duration, but also decrease development costs since challenges and design problems can be avoided on time.
DRIVER COACHING AS A CHANCE TO IMPROVE REAL EFFICIENCY
Even when the vehicle’s systems provide all requirements for optimal energy management and maximum efficiency, the individual driver can experience a real driving range that undercuts the WLTP measured nominal range. This can happen when a battery electric vehicle is willfully or unknowingly operated by the driver in an energy-adverse fashion. This is where the so-called driver coaching via the vehicle’s infotainment systems can make a difference and exceed pure entertainment and information service in the near future. It can provide the drivers with guidance about operating the vehicle with utmost energy efficiency, by offering different driving modes like energy saving mode, normal mode or performance mode, for example.
The driver coaching will be adapted according to the chosen driving mode – for example, it can be assumed that the driver is knowingly forfeiting maximum driving range when choosing performance mode, so there will be no or less guidance from the system. On the contrary, guidance will be offered when drivers choose the energy saving mode, efficiency mode or economy mode to ensure actual optimal energy savings and maximum driving range. It can be assumed that the driver is not excepting a high-velocity driving experience while choosing these modes.
Route planning and driving habits as factors of energy management
Interconnectivity with the navigation system and observation of frequent driving habits offer further possibilities to increase real efficiency. For example, if the system detects a commuting habit of operating the vehicle for a short distance for the duration of ten minutes each morning, it may hint that the overall vehicle does not need to be fully heated up or cooled down to optimal operating temperatures, thus saving energy. In contrast, climatizing the passenger cabin and the batteries to optimal temperature makes sense if the goal of the route navigation is 300 kilometers away, since a battery in optimal operating conditions can provide more energy and improve fast-charging capabilities if necessary. Interconnectivity with route navigation and information can also improve efficiency in some cases. For example, it could determine if it is better to use the vehicle’s momentum or to increase recuperation strength for a purposeful deceleration.
In this aspect too, MAGNA as a development partner can act as an intersection between subsystem suppliers to ensure that the driver coaching can provide guidance for actual utmost efficiency. To provide another example, it can be more energy efficient to concentrate the passenger cabin climatization on only one seat if the vehicle is operated only by one person instead of opening the window or roof-light since this measure can decrease aerodynamics and negatively impact efficiency more than the usage of the A/C.Stay connected with Inside Automotive!
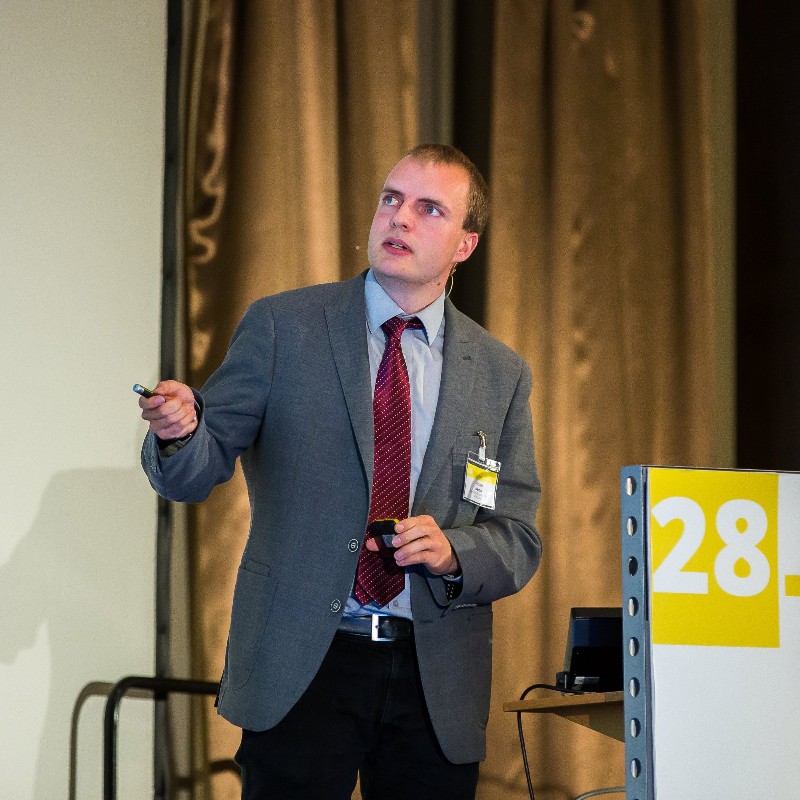
Michael Martin
Michael Martin is currently working as a Group Leader for Energy Management & Operating Strategy at Magna Steyr. He has experience as a Senior Engineer specializing in driving performance, energy efficiency, and driveability. He started his career at Magna as a Simulation Engineer in the field of energy management in 2011. He holds a doctoral degree in mechanical engineering from the Technical University of Graz, with a focus on automotive engineering.
We want to hear from you
Send us your questions, thoughts and inquiries or engage in the conversation on social media.
Related Stories
Stay connected
You can stay connected with Magna News and Stories through email alerts sent to your inbox in real time.