LONGER DISCHARGE TIME OF THE ELECTRIC CAR AT HIGHER VOLTAGE LEVELS
Due to the higher voltage levels, a lot more energy is stored in the EV’s intermediate systems, such as its cable network. The amount of energy increases as the square of the voltage. For example, in a system in which an amount of energy of 120 J remains at 400 V, 480 J remain at 800 V and even 750 J at 1000 V. This poses a challenge for the legally required rapid discharging ability of the vehicle system.
The legal requirements state that in the case of an emergency shutdown of the vehicle (e.g., after a crash), all parts of the vehicle must free of any electric potential (higher than 60 V, at least) after 5 seconds. In the case of the “conventional” 400 V, a single electric discharge unit suffices to remove any residual potential (e.g., an electric drive unit).
At higher voltage levels however, residual potential is higher – and more EDUs are needed to completely discharge all components within 5 seconds. Current trends indicate a shift towards self-discharging components, a technically feasible, albeit quite expensive solution to this problem. Additionally, costs are also increased by the more complex battery management system (BMS) which is needed at higher voltage levels due to more battery cells connected serially.
TECHNICAL CHALLENGES CAUSED BY HIGHER VOLTAGE LEVELS
Inverters, which are needed for an EV’s motor control, also face higher efforts at higher voltage levels. The electronic circuits (usually silicon IGBTs are used) within the inverter may reach their limits when voltage peaks occur; Switching to a different material such as silicon carbide (SiC) is required to ensure the required high switching power.
The switching losses depend linearly on the voltage, current, switching duration, and switching frequency. With constant power, higher voltage and lower current, the power loss can be mitigated by using fast-switching SiC-IGBTs. Another (expensive) solution could be simply switching the inverter architecture. Whether the higher efficiency are worth the higher costs should be coordinated with the OEM in both cases.
One problem that remains is electromagnetic interference (EMI) within the inverter occurs more frequently at higher voltage levels. EMIs may cause malfunctioning of the EV’s electronic assemblies, but they may also damage the insulations of the motor windings, which shortens the engine’s lifetime. They can be prevented from spreading along the cables and lines by installing improved filter units. Meanwhile, a shielded HV on-board power supply protects surrounding assemblies form EMI.
HIGHER VOLTAGE LEVELS DO NOT SOLVE ALL CHALLENGES WITH EVs
In conclusion: Switching to a voltage level higher than 400 V is by no means a perfect one-size-fits-all solution to increase efficiency, performance, and fast charging capacities of EVs. HV batteries definitely lead to large improvements in all regards, but only do so alongside a notable increase in costs. Whether switching 800 V or higher provides a competitive advantage or not must be gauged for each vehicle project individually.
Overall, higher voltages synergize best with high-performance BEVs sporting very large batteries. Here, the much higher charging power potential is much more relevant – and end customers can be expected to pay more for the improved technology. EVs of smaller sizes on the other hand benefit more from 400 V, as the lower voltage level is not only cheaper, but also provides several additional advantages.
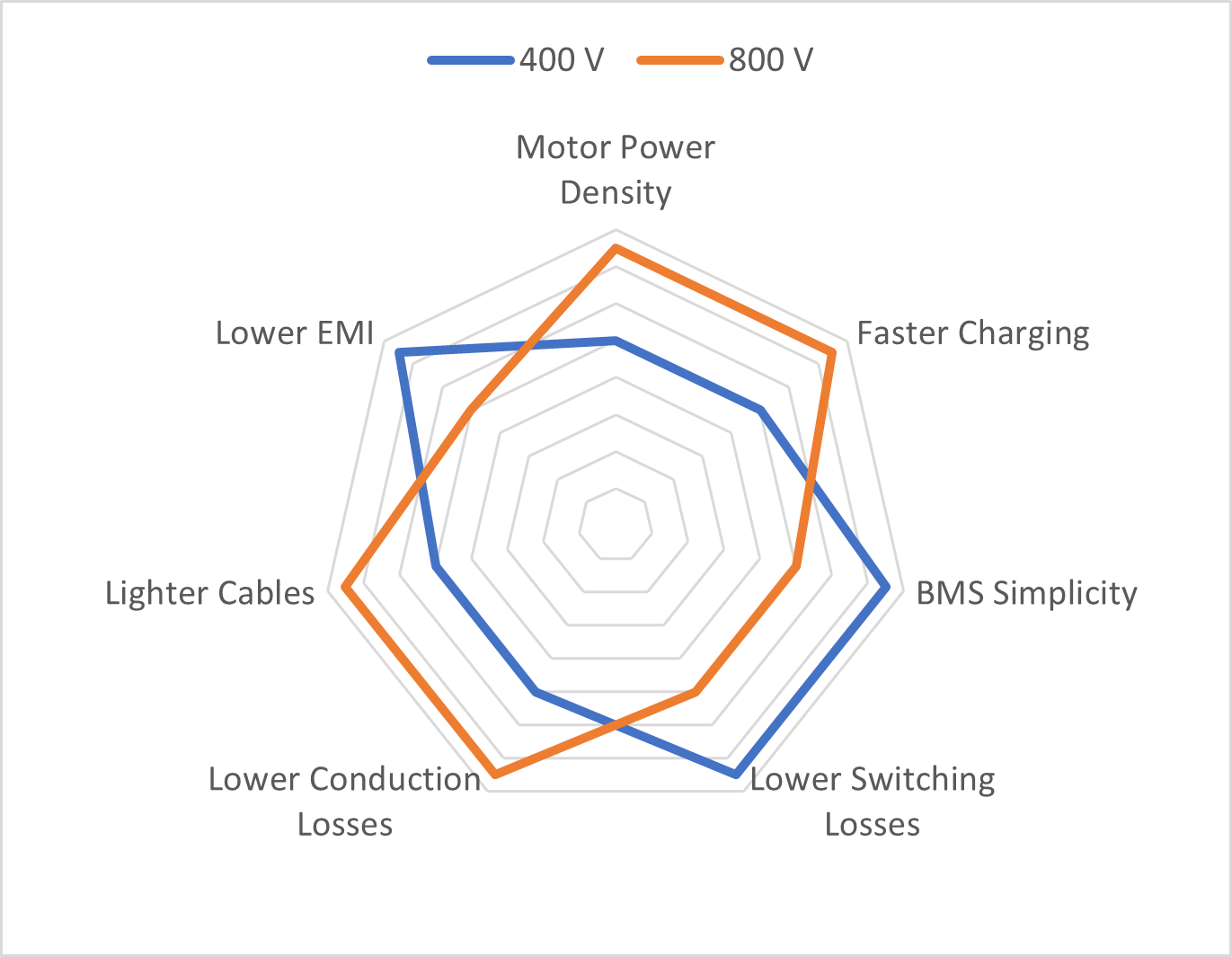
Advantages and disadvantages of 400 V and 800 V powertrain systems: HV disadvantages can be fixed with technical improvements, although higher costs should be expected.