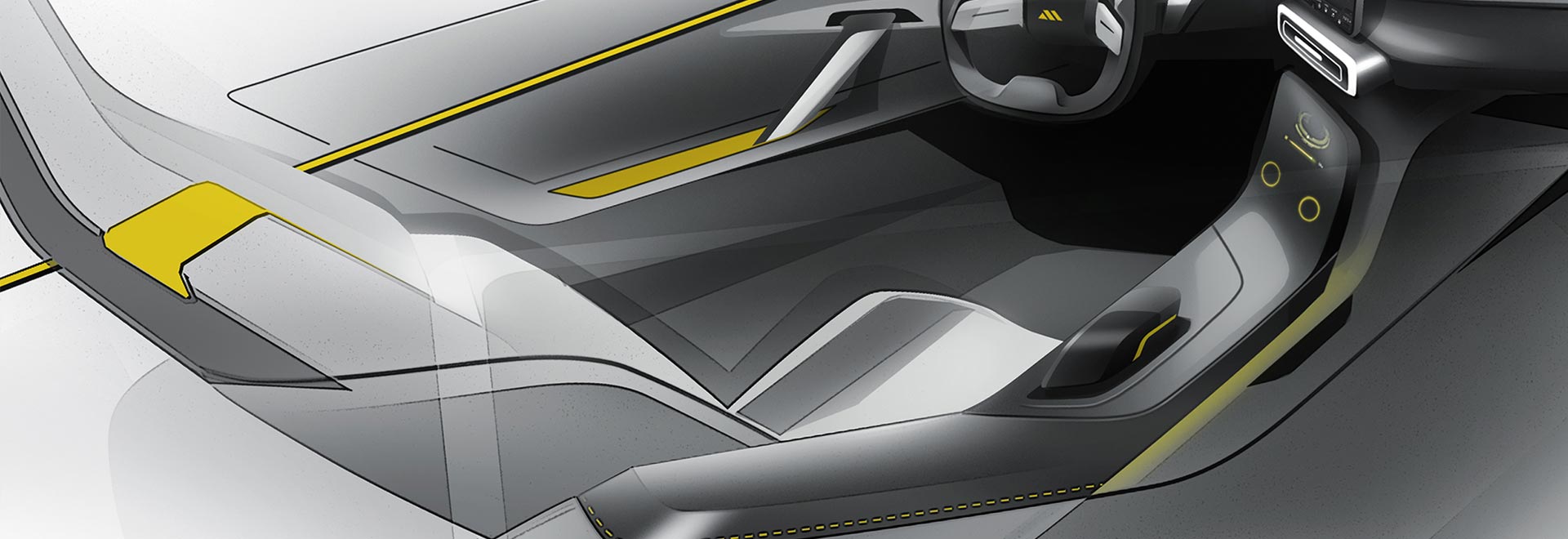
Future Vehicle Production With Advanced Manufacturing Engineering
- Gernot Trücher
- May 11, 2022
- 3-min read
This article will introduce the concept of Advanced Manufacturing Engineering, or AME. It will explain what AME means, what it encompasses, what challenges it can bring, and how to best tackle those challenges.
Previous articles have already covered the basics of manufacturing facilities. In those articles, the focus has been on finding the best solution for vehicle manufacturing facilities in a more general sense.
However, the really important questions arise when discussing the vehicle development and production itself, and the requirements needed for a fledgling automotive business.
A SHORT INTRODUCTION TO ADVANCED MANUFACTURING ENGINEERING
Advanced manufacturing engineering, or AME, describes all necessary activities to ensure the manufacturability of the complete vehicle and consequently its systems and parts.
Some functions covered by AME include the definition of ideal joining sequences for a vehicle’s body work, and the joining techniques that should be used for it. It also covers the creation of accessibility studies to ensure that singular parts can be joined easily by either workers or machinery, and conducting ergonomic analyses to make sure that workers can consistently do their tasks without impairing either their health or their productivity.
In short, the key goal of AME is to ensure that individual parts fit into one serially produced vehicle in the most efficient way. A carefully laid out AME concept lowers the total time and cost requirements for serial production, while keeping the product quality consistently at the highest level. “Consistently” meaning that even if the same sequence has been repeated 99.999 times, at the 100.000th time, it is still performed as accurately as on day 1 of serial production.
AME and factory planning
It should be pointed out at this section, that AME concepts can only work if their requirements are also considered in the factory planning. The various experts planning the implementation of the necessary technologies into their factory concept also have to work under the frame set by the AME planners. Specifications, such as joining sequences, provide the basis of the future processes and plants necessary to serially produce a vehicle later on.
WHY ADVANCED MANUFACTURING ENGINEERING MUST BE PLANNED ON DAY 1
While production happens at a fairly late stage of a complete vehicle project, it needs to be taken into account during the development process in order to create a functional AME strategy.
The key to AME lies in consistent optimization
Vehicle planning should not be seen as a strictly linear task in the first place. Sure, production comes after development, but a good concept team concerns itself with every step of the way forward as early as possible, and then sets up all processes in parallel.
Considering AME and involving the production planners from day 1 on ensures that the production needs can be taken into account during the development phase. The team is involved early and coordinates with the various other teams on a regular, even daily, basis. Concepts are consistently examined changed and optimized, until step by step, the complete vehicle concept, including the AME strategy, takes shape.
This synchronous way of working saves time in the project. When AME is considered in parallel with other phases, its requirements and the expertise of its planners can influence and improve other fields, and vice versa.
THE MAIN ACTIVITIES OF ADVANCED MANUFACTURING ENGINEERING
With that, let’s take a closer look at what the development areas of a vehicle look like, and where an AME concept steps in to ensure that this serial production chain is – and remains – efficient:
At Magna, our manufacturing concepts are clustered into six fields. Five of those fields directly mirror our production sequence. The sixth – tolerance management – takes on a more cross-sectional function:
Stamping/Press Shop
Stamping is the process of forming body parts out of sheet metal. The most important questions of stamping concern formability, as well as surface quality, dimensional accuracy, and yield rates.
The metal parts have to be stamped with the highest levels of quality and accuracy, because these parts will later be joined together. Even a minor miscalculation impacts the quality of the complete vehicle down the line.
The AME team needs to therefore ensure that the parts can be molded within the limits of the raw material and are feasible for optimum surface quality and correct dimensioning.
Body Manufacture/Body Shop
After stamping body parts, the next step is to devise a way they can be joined.
The main focus in the body shop is the specification of this joining sequence, and the specification and examination of various joining techniques and technologies.
Furthermore, the maintenance of tolerances, investigations, and accessibility studies for body manufacture are an essential part of the AME strategy.
The seamless execution of this process ensures that the planned quantity can be produced with the highest quality standards and lowest time and cost efforts.
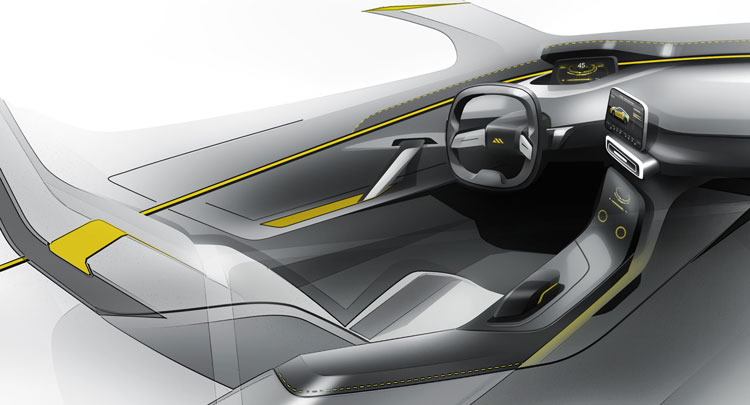
Painting/Paint Shop
Even the most modern paint shop requires a great many activities during the development phase. The AME team must consider factors like water and weather management, waxing, sealing, measures for corrosion protection and tightness, and accessibility from an early concept phase on. In order to ensure a good paint job, the AME team must accessibilities and processes to ensure that both protection and design fit.
Corrosion & Tightness
Protection from water and dirt is one thing – it is an entirely different thing to ensure that the vehicle’s surface does not wear away over time. A vehicle should not be affected by leakage or corrosion, so its quality and functionality can be ensured over a long period of time.
The tasks of AME in terms of those protection efforts revolve around developing a functional corrosion and tightness management, which analyzes the different types of abrasion and implements appropriate protection measures, e.g., with passivated coating.
General Assembly
General assembly describes the process of, well, assembling the complete vehicle. The previously assembled and painted car body is now being completed in the interior and exterior until step by step, the complete vehicle is formed.
Tasks for AME in this phase revolve around ensuring accessibility for workers. This includes factors such as conducting ergonomic analysis, finding the optimal assembly sequence, or defining production tolerances.
Tolerance Management
The tolerance management experts hold a cross-functional role within the AME Team.
Their task is to create, analyze, and optimize vehicle tolerance concepts – for individual parts as well as for the complete vehicle. This is done through the use of specialized software, as well as various planning models for the vehicle’s interior/exterior.
HOW TO GET ADVANCED MANUFACTURING ENGINEERING RIGHT
The most fundamental challenges of implementing an AME concept revolves around the conflicts of goals between developers and planners. This means that the targets set by the vehicle developers may run diametrically opposed to the requirements set by the AME planners.
Those conflicts can revolve around a number of different issues. For example, a certain vehicle module may come in a specific design in order to achieve the weight or cost targets of the project. However, as a consequence, the part may lead to production difficulties because of its design.
Accessibility is another point of conflict. Assembly parts need to be aligned with the complete vehicle in mind, but also with the workers and machinery that assemble them in mind. If the worker who must join the components can no longer reach the attachment point, the manufacturing engineer must either find a different tool, change the worker’s fitting position or – in the worst case – rethink the development concept.
Magna as your partner for AME
Luckily, new entrants and existing OEMs have the option of teaming up with a manufacturing engineering partner that can take over the planning and implementation of the vehicle’s production site. Magna has the distinct advantage of offering AME support as part of our one-stop-shop service for vehicle production. Teaming up with Magna provides new entrants with a partner that has long-standing expertise in automotive planning, development, and production, as well as drafting and realizing the manufacturing infrastructure to match.
WHAT'S NEXT?
To summarize: AME describes all activities over the course of the development process to ensure optimal production from a factory-focused point of view. A key factor here is the early involvement of AME experts in the development team. Together, the two teams manage to face this challenge as one front, leading to a considerably smoother transition from concept development to production.
AME concepts face several challenges over the manufacturing chain. From stamping to assembly and tolerance management, several points of conflict may appear when development concepts and targets have to be implemented in (serial) production. AME can only be successfully implemented with close cooperation across vehicle development and factory planning. Of course, teaming up with an experienced partner also greatly improves the quality of an AME concept.
AME is a very complex topic that can't be fully explained in a single article. And although serial production only becomes an active part of the vehicle process much later, it is vital to recognize and solve the many facets and challenges of Advanced Manufacturing Engineering as early as possible. The process of manufacturing hundreds of thousands of vehicles does not allow any room for error – therefore, it must be planned during the development phase.
Stay connected with Inside Automotive!
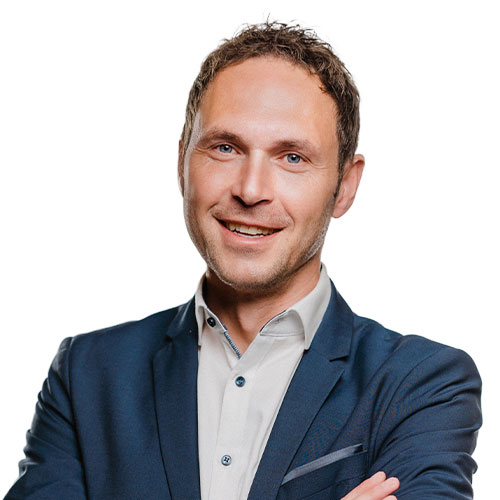
Gernot Trücher
Gernot Trücher has been with Magna since 2000. He held several positions in the areas of Logistics, Manufacturing Engineering and Contract Manufacturing. Since 2017 Gernot Trücher is Director Industrial Services.
We want to hear from you
Send us your questions, thoughts and inquiries or engage in the conversation on social media.
Related Stories
Stay connected
You can stay connected with Magna News and Stories through email alerts sent to your inbox in real time.